Advanced Sensing Solutions for Cost-Effective Machine Building
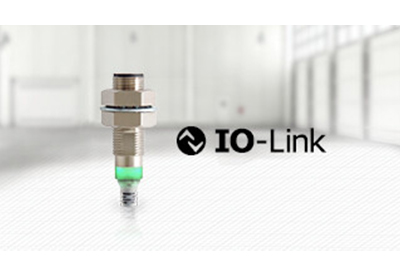
August 24, 2020
By Michael Hamoy, Product Manager – Sensors, and Felix Klebe, Marketing Manager – Sensor and Advanced Sensing
Here’s how the right sensors can cut machine-building costs, improve flexibility and boost customer satisfaction.
Sensing technology has a major presence in manufacturing machinery. It provides the foundation for maintaining consistent quality and detecting any lapses in machine performance. If subtle changes in the physical properties of a machine can cause it to fail, then the sensors responsible for detecting those changes can save manufacturers lengthy downtime and repair costs.
In addition to helping cut maintenance costs, sensors also present an opportunity to make the machines more cost-efficient. Whether through their resistance to harsh chemicals or their ability to reduce the overall machine footprint, the right sensors can make a huge difference. In this article, we’ll discuss several ways in which intelligently designed sensors can make machine design more cost-effective.
1. Sensors with remote I/O blocks minimize wiring and machine complexity
To collect as much data as possible on the quality of works-in-progress and the level of machine functionality, it helps to include numerous sensors on the machines. This poses a new challenge, however, since more sensors leads to more wires, and an increase in wires leads to a more expensive machine design. Excess wires also add complexity, meaning that it will take longer to commission a new machine and troubleshoot any issues that arise.
Customers expect machines to offer greater performance in a more compact design, and they want those machines to be delivered more quickly at attractive prices. Sensors with built-in networks or remote I/O blocks helps control cabinet size and reduce machine complexity thanks to the resulting reduction in wiring. With conventional sensors, it’s necessary to run the wires all the way back to the PLC.
2. IP-rated sensors ensure greater longevity in challenging environments
In industries like automotive manufacturing and food and beverage production, sensors face all sorts of potentially destructive chemicals and processes. Dairy production, poultry processing, beef processing and similar applications use intense washdown treatments to eliminate the growth of bacteria and fungi. These washdowns incorporate harsh chemicals, high heat and high-pressure sprays.
Sensors used in these industries need to be rated IP69K for washdowns, both for the sake of overall longevity and cost-effectiveness, and also because they – like everything else on the production line – must be cleaned regularly to prevent dangerous levels of bacterial growth. If sensors are too delicate to be washed down, they’re more likely to be damaged in the cleaning process, fail prematurely and cause manufacturers to experience unplanned downtime that would otherwise be avoidable.
In automotive applications and metal pipe cutting, a common cause of sensor breakdown is cutting oil. Oil-resistant sensors that are rated IP67G provide rugged durability for harsh environments so that manufacturers who use the cutting fluids can eliminate oil ingress by any path, which in turn will minimize unexpected machine downtime and lower the cost of ownership of their equipment. These sensors successfully keep oil out by means of fluororesin cable sheaths that provide extra-strong resistance to deterioration and boost protection at joints and moving sections.
3. Smart sensors improve predictive maintenance and minimize downtime
If a machine is starting to have problems functioning, the sensors will be the first to know it. That is, they’ll be the first to gather any abnormal data that could point to machine trouble. However, if this data isn’t properly communicated and analyzed, the deteriorating machine function could easily go unnoticed.
Smart sensors, considered to be a major component of the Industrial Internet of Things (IIoT) or Industry 4.0, can help end users monitor machine performance in real time. Because they don’t need to send data through an I/O point like conventional sensors do, they can communicate more complex data than a simple on/off status. They can return runtime information, approximate temperature, and output data over time, this data can offer insight into whether a part of the machine might fail in the near future.
By giving clearer, more detailed insight into how the system is working, smart sensors can make predictive maintenance much easier and much more effective. Manufacturers can catch problems while they’re still relatively easy to fix and thereby avoid long periods of downtime. In industries like automotive manufacturing, where downtime can cost $10,000-$12,000 per minute, smart sensors can be an extremely cost-effective solution.
4. IIoT-ready sensors improve machine-to-machine communication
The benefits of smart sensors go well beyond predictive maintenance. With the adoption of IIoT technologies increasing worldwide, machines require greater bandwidth. Ethernet is the new standard for machine-to-machine communication thanks to its numerous advantages, including easy scalability, faster speeds and network simplification.
The foundation of IIoT is data – specifically, machine-level data that is collected at the sensor level. The higher-level analytics and benefits of an IIoT solution depend upon the quality and versatility of the data that is collected at the machine level. Smart sensors can help manufacturers reap the benefits of an IIoT solution, including lower costs and reduced downtime, because they provide more data overall to the manufacturing execution system.
To offer some examples of data provided by Omron’s latest IIoT-enabled sensors, the E2E NEXT family of proximity sensors can communicate when an object or target is getting too close to the sensor and could potentially damage it. Additionally, Omron’s newest time-of-flight photoelectric sensor, the E3AS-F, can provide measurement data via IO-Link.
Putting it all together
Efforts to make machine building more cost-effective should never overlook the sensors. When machine builders choose the right sensors for the needs of their customers, they can ensure that those machines will have greater longevity, a smaller footprint and more effective predictive maintenance. Sensors play a significant role in every aspect of machine functionality and resistance to wear and tear.
In summary, machine builders can employ the following strategies to keep their machines cost-effective and reliable:
- Use smart sensors or sensors with remote I/O blocks to eliminate wires and reduce machine complexity while collecting as much data as possible on machine function and work-in-progress status.
- Select environmentally robust sensors if required to prevent premature machine failure and unplanned downtime. Choosing the wrong sensor upfront can cost a lot in the long run.
- Improve predictive maintenance by employing smart sensors to give the system the copious data that it needs for analytics.
- Make connected choices. The future of manufacturing is in data, so it’s important to select sensors that will provide the data that customers may need in the future.
Machine builders who take advantage of the above strategies and consider sensing technology to be an important focus for long-term cost-effectiveness will receive much greater customer satisfaction thanks to dramatic improvements in ease of use, flexibility and overall productivity.
https://automation.omron.com/en/us/blog/advanced-sensing-for-machine-building