Omron: Robotics Integrated Controller
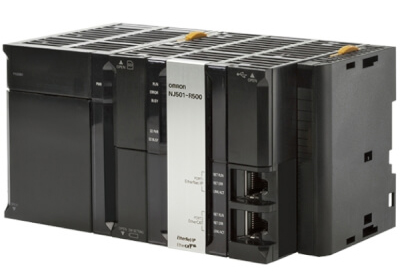
November 21, 2022
An all-in-one control platform for applications requiring high-speed processing, machine control, safety, reliability and maintainability.
The Omron Robotics Integrated Controller (IC) perfectly synchronizes automation technology so that customers can improve the speed and accuracy of their production, simulate entire production lines, simplify maintenance, and reduce time-to-market.
The Robotics Integrated Platform is the next revolutionary step in the SYSMAC ecosystem that seamlessly integrates the full Omron Fixed Robotics product line. Omron’s one controller approach integrates robot control, in addition to sequence and motion control, to a single controller. This enables synchronized control of robots as well as other devices and results in higher performance compared to typical network based configurations. It also enables users to collect information on devices aligned to a common timeline which not only improves overall system response times and accuracy but also greatly aids in troubleshooting activities.
Key Benefits
Faster solution evaluation
- – Early ROI calculation and design validations thanks to simulation software
- – Changeover improvements of future products can be validated by simulation.
- – Investment cost can be calculated in advance.
- – Cycle time estimation
Lower commissioning time
- – Reduced integration time with programming off-line.
- – Optional “Applicaton Manager” add-in software reduces integration time and learning curve.
- – Reduced mechanical and electrical design burden by emulating full cells through the Sysmac Platform.
Lower cost of ownership
- – Real time synchronization between robot, PLC and all EtherCAT connected devices improve productivity.
- – Recipe manager makes modifications easy and minimize the product change over time.
Key Features:
- – Multiple robot control per single CPU
- – Integration of Robotics, Logic, and Motion in one CPU
- – Conforms to IEC 61131-3 (JIS B 3503) standard programming and PLCopen function blocks for motion control
- – Conforms to IEC 61131-3 (JIS B 3503) standard programming and traditional V+ scripting for robot and motion control
- – Programming with variables allows users to create complex programs efficiently
- – Models with SQL DB Functionality
- – Offers speed without compromising on reliability and robustness expected from PLCs.
- – Linear and circular interpolation.
- – Electronic gear and cam synchronization.
- – Fast and accurate control by synchronizing all EtherCAT devices, such as vision, servos, robots, and IO with the controller.