Beckhoff: AL8000 Linear Motors – Highly Dynamic Linear Motors With Flexible, Modular Design
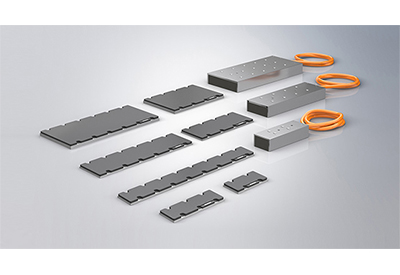
December 14, 2020
Backed by a wealth of expertise in the development of rotary servomotors, Beckhoff has added an innovative product to its portfolio in the area of drive technology. This new generation of high‐performance and modular linear motors was developed in cooperation with its dynamically growing subsidiary Fertig Motors.
The new AL8000 product family is based on a modular system design consisting of linear motors and magnetic plates. Users can choose between three widths: 50 mm (AL8x2x), 80 mm (AL8x4x) and 130 mm (AL8x6x). In addition, each width category offers a broad range of different linear motor types in terms of overall length, type of winding and cooling type. The standard product portfolio therefore contains a total of 28 different linear motor types for implementing highly dynamic and powerful linear axes to suit specific application requirements. Depending on the size of the linear motor, peak forces of 120 to 6,750 N can be achieved as well as maximum speeds of up to 12 m/s.
Like the established AM8000 rotary servomotors, the AL8000 family of linear motors is fully developed and manufactured in Germany. A consistently high level of production quality is therefore guaranteed as well as high availability and short supply chains for realizing durable and highly reliable applications with linear motor technology. Further advantages include outstanding service and support, ensuring that customer requirements can be fulfilled quickly and flexibly.
Modular coil design
In keeping with the modular system principle, the entire coil part is composed of individual, identical segments. This construction is especially favorable from a production perspective: Depending on which linear motor the customer orders, the production process can be adapted quickly and easily to the relevant number of segments. This positively impacts both delivery times and the ability to adapt to customer requirements. If users do not find what they are looking for in the standard product portfolio, a custom motor can also be developed and produced without major additional cost and effort. Any number of coils can be implemented in steps of three up to a maximum of 45 coils, in order to fulfill individual application requirements.
Yet another advantage of the modular coil design is the precisely symmetrical structure of the linear motors. There are uniform intervals between the mounting holes of the linear motors throughout the entire AL8000 series. This makes it easier for machine manufacturers to construct the machine slide and automatically ensures screw mounting compatibility with the other linear motors of the same width. In addition, the symmetrical structure ensures consistent force and temperature distribution within the motor, thus avoiding critical hot spots.
Another special feature of the AL8000 relates to the connection technology: The linear motors feature a combined cable with a fixed cable length. This combined cable contains both the power supply and the temperature sensor. Because the power transmission is combined with thermal protection, there is no need for a thermoprotection cable either directly on the linear motor or in the drag chain up to the control cabinet. This reduces material costs, potential error sources and installation costs.
The AL8000 linear motor series uses the same cable and connector plug as the AM8000 rotary synchronous servomotors, which means identical standard motor cables are used for both product series. This not only simplifies logistics, but also ordering on the part of the machine manufacturer – in cases where a machine is to be equipped with both rotary and linear servomotors from Beckhoff. The linear motor cable is optionally available pre‐assembled with matching connector or an open cable end with free cores.
Fully integrated in the motion system
The AL8000 linear motors are fully integrated into Beckhoff drive technology and optimized for use in combination with other system components. The series is also adapted accordingly to the technical specifications of the AX5000 digital compact servo drives and the AX8000 multi‐axis servo system, meaning that an ideal drive system can be designed for each application.
Both the design and commissioning of the AL8000 linear motors are straightforward and user friendly through the use of standard TwinCAT 3 software tools. This simplifies application calculations and the dimensioning of the drive components (motor, servo drive and other accessories) when designing the drive system using the TC3 Motion Designer (TE5910). Users can scale the rotary and linear drive technology of their entire machine to suit their needs. All they need to know in this respect are the details of the loads to be moved and the required dynamics. They can then use this data to create a full load profile and either independently select the best motors for their application or have this indicated using the optimization function of the TC3 Motion Designer. Users also have direct access to technical data sheets, dimensional drawings and motor characteristics.
Following completion of the design, the system is commissioned using the proven TC3 Drive Manager 2 (TE5950) engineering software. This tool fully supports the AL8000 and systematically guides users through commissioning. The drive parameters can also be displayed, adjusted and their impact on the drive response examined during operation for optimization efforts.
Advantages of linear motors
Loads can be transported within a machine using a variety of different systems. Either conventional drive systems, such as rack-and-pinion, spindle or toothed belt drives, can be used or linear motor systems. The respective systems offer different advantages depending on the application requirements. Apart from costs, key factors when choosing the best solution include requirements in relation to the masses to be moved, the length of the travel path, the positioning accuracy and the required dynamic.
The conventional drive mechanics are powered by a rotary motor and generally use its encoder for positioning. However, since the mechanical conversion of rotary movement to translational movement is always dependent on backlash, the positioning accuracy is impaired. To achieve highly accurate positioning, a second external encoder system is therefore required directly at the load, though this comes at an additional cost. In addition, use of a conventional drive mechanism often necessitates a gear unit to adjust the mass inertia ratio, which again involves additional costs. Apart from the acquisition costs, the running costs owing to regular maintenance have to be taken into account with conventional drive mechanics. Irrespective of this, drive systems can be classified as follows:
- – Toothed belt drives can transmit a high dynamic in terms of speed and are attractively priced. However, owing to the elasticity of the toothed belt, the transmitted forces, the precision and the control accuracy of the system are restricted.
- – Rack-and-pinion drive systems can cover long travel paths, high dynamics, and the transmission of high forces. The achievable accuracy is likewise restricted, by the backlash between the rack and pinion.
- – Spindle systems on the other hand achieve very high transmittable forces owing to their system translation as well as high positioning accuracy. The travel path and dynamic in terms of achievable speeds are the limiting parameters in this case.
Linear motor systems are therefore especially advantageous when very strict requirements have to be fulfilled both in relation to dynamic and positioning accuracy. Because there is no mechanical conversion from rotary to translational movement, there is no backlash on the connection between the load and the motor. The position sensor can therefore also be connected directly to the motor so that backlash-free, highly dynamic and precise position control is possible. The direct translational movement of the linear motor together with a high-resolution position feedback is the basic prerequisite for achieving high-precision machines.
https://www.beckhoffautomation.com/english.asp?press/news6020.htm