Allied Ask the Expert: Selecting the Right Electrical Enclosure for the Right Environment
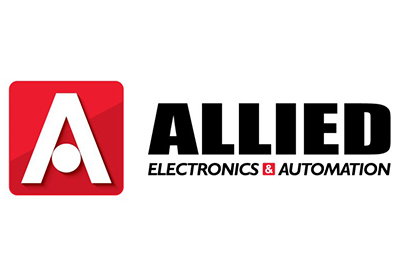
September 21, 2021
In this edition, we talk with Tom Ballou, sales and marketing manager for Hammond Manufacturing, about the factors involved in choosing an electrical enclosure to suit the environment it will be placed in and how playing it too safe can lead to unnecessary expenses.
What are the most important factors in selecting an electrical enclosure?
There are a number of factors involved in selecting an electrical enclosure. The most important are generally:
- Protection rating – Choose based on how effectively the enclosure needs to protect against ingress of water, dust, oil, or chemicals.
- Certification & approvals – Based on the location, usage, and equipment inside, what certifications or approvals (such as UL, NSF, CSA, NEMA) will you need to ensure safety and compliance with industry regulations? Hammond offers enclosures to fit all types of certifications and approvals.
- Size – Determine the minimum dimensions needed to house all components, with the depth of the deepest component often driving the choice.
- Access – The interior of an enclosure is generally accessed through a front door or cover. These can be closed with quarter-turn latches, clamps, handles, or screws. The ideal choice will be driven by the frequency of access, security concerns, and planned device mounting on the door (e.g., handles take up more door space).
- Temperature – This includes the temperature indoors or outdoors where the enclosure will be located, as well as the temperature or heat generated by the equipment inside of the enclosure.
- Corrosion resistance – Understand what conditions the enclosure will be subjected to based on its location, such as weather, temperature extremes, seawater, chemicals, frequent washing, etc.
- Cost – Different materials and ratings can vary widely, so it’s important to not over-specify the enclosure and overspend.
How does the environment the enclosure will be located in factor into the selection and buying process?
Enclosures are used in many different environments, and they come in various materials like stainless steel, aluminum, and fiberglass-reinforced polyester to help endure these environments. It’s important to consider where the enclosure will be installed and the ambient temperature inside the enclosure. If the enclosure is located in a very warm environment, this could affect the enclosure’s ability to disperse heat generated by the equipment inside. Therefore, it may be important to select a larger enclosure than needed for the equipment itself to allow air to circulate inside and around the equipment to prevent component failure.
In some environments, the material and corrosion resistance of the enclosure becomes more important. For example, if the enclosure will be on an oil rig in a marine environment where saltwater waves may be splashing across it, you will want 316 stainless steel, which can stand up to such conditions. In a very cold environment, you would choose fiberglass-reinforced polyester.
The material you choose affects the cost. Non-metallic materials, such as fiberglass-reinforced polyester or polycarbonate, can be less expensive than 304 or 316 stainless; however, depending on the application, fiberglass may not be the right choice.
The shape of the enclosure may also come into play. In food processing environments, high-pressure, high-temperature washdowns are a frequent occurrence. A sloped top, such as in the Hammond Waterfall series, keeps water from pooling on the enclosure. Pooled or standing water could lead to rust and corrosion on the enclosure, as well as bacteria buildup that can jeopardize food safety and compliance.
If the enclosure will be in a harsh environment where corrosion resistance is critical, what construction material is best, or can I simply choose any enclosure that is rated NEMA 4X?
NEMA 4X is a good starting point, but other factors come into play. Enclosures made of a few different materials can carry the same rating, so you really need to know more about what material is best for each environment and balance that with cost. Not all NEMA 4X rated enclosures offer the same level of resistance to certain chemicals, for example. 304 stainless steel is good for areas that are hosed down frequently, like food processing. 316 stainless is suitable for marine oil rigs, offering a higher degree of protection against saltwater. Fiberglass-reinforced polyester is good for chemical-laden areas and very cold temperatures.
It’s important to do a little research to ensure the material you choose matches the intended environment. NEMA 4X is a big bucket that indicates the enclosure is corrosion resistant in some way but does not get specific in terms of which chemicals or elements the enclosure resists.
What is the biggest mistake buyers make when selecting an electrical enclosure?
Most often, the mistake I see is over-specifying the enclosure they need. Most times, this is because the company is trying to play it safe, but playing it too safe can significantly increase the cost of the enclosure. For example, in an industrial factory, you want to keep sensitive equipment safe from circulating dust. You could choose a NEMA 4x enclosure made of 316 stainless steel, and it will certainly protect enclosed equipment in that indoor industrial environment. However, because the enclosure will not be subjected to driving rain, powerful water jets, or saltwater, like in the extreme environments it’s designed for, you don’t need the 316 steel. It costs a lot more than a Type 12 enclosure, which is designed for protection against dust and would be more suitable for this factory environment.
You want to pay a lot of attention to matching the enclosure box (material and features) to the environment. There is an enclosure for just about every type of environment. Obviously, the higher-rated ones that can withstand extreme conditions, like sleet, or temperatures would also protect against lesser conditions, but the cost difference can also be extreme. So, it’s important to use them based on what environments they are made to withstand.
What are some of the things that can happen if you choose the “wrong” enclosure
Choosing the wrong enclosure – or one not suitable for the environment – can lead to a much shorter service life for the enclosure and, at worst, can lead to component failure in the equipment inside the enclosure. This can lead to entire systems going down, which then leads to safety issues and financial impact for the company. Using the oil rig example, if you use a mild steel enclosure (meaning plain steel with paint on it) in that harsh marine environment, you would quickly see surface rust, and eventually, that corrosion will go through the material, allowing water to get into the equipment. Once the equipment is exposed to seawater, that could put workers in danger and cause the oil rig to go offline. This scenario would cost the company a lot of money to get that oil rig back online and restart production. A much better solution is to take your time in the beginning and make sure you specify the right enclosure for the environment. In this case, the 316 stainless steel is specifically designed to handle the marine oil rig’s environment and will last long term.
Hammond Manufacturing has over 6,000 standard electrical enclosures and accessories available. What is the most efficient way to narrow down the search to find the enclosures most well-suited to a buyer’s particular needs?
Hammond tech support can help anyone select the right type of enclosure for the application and environment needed. Our website is an excellent resource for that as well, with lots of technical data that can be downloaded. If you talk to a Hammond technical expert or use our site and determine you need a stainless steel enclosure with a 4x rating, it’s very easy to go to Allied’s site and filter down by the material and ratings and find the exact enclosure you need. Their site is very efficient at sorting enclosures by different parameters, enabling you to narrow your search pretty quickly.