How To Uncover (And Fix) Control System Issues In Real-Time
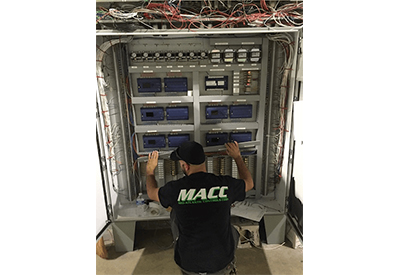
February 19, 2021
There’s always the potential for control system issues to arise, in older facilities and even in new construction. From faulty sensors to loose plugs, addressing the small issues within a building automation system (BAS) could stop big problems from developing later on.
MACC proudly claim to deliver a superior BAS maintenance service that includes finding (and fixing) control issues in real-time. Here’s how they do it.
What Causes Control Issues?
Building automation is complex. There are hundreds of components—fans, chillers, valves, sensors, wiring, and more—all working together to keep your BAS running correctly.
“Mistakes happen. Installers are human and could have hooked the wrong wires up. For example, the status of exhaust fan one could be mistakenly attached to the alarm input of exhaust fan two.” ~ VP of Technical Services for MACC
Any connected device with a glitch could trigger a control issue. Here are a few of the reasons why problems start:
Construction errors
It shouldn’t happen, but with hectic schedules and a looming deadline, even the most diligent builder can make a mistake.
Equipment vibration
The vibration from normal operation could be responsible for shaking loose the connections on plugs, cables, and screws.
Defects
Wiring, sensors, and other devices may have defects unnoticed by the original manufacturer.
Setpoint drift
Over time, sensors drift from their calibration settings and provide incorrect readings.
Building upgrades & retrofits
During renovations, workers can accidentally (and unknowingly) damage the BAS wiring or other components.
Finding the Root Cause
Your BAS tracks information about equipment performance, sensor readings, alarm status, and more. And when the trends are off normal, something’s wrong.
Compensating for trouble – Sometimes the system seems to function normally when it’s actually experiencing an issue. For instance, if a hot water valve is stuck open, the water from a faucet will be too hot. Adding cold water gets the temperature right but doesn’t fix the real problem.
Deteriorating parts – Control issues happen when components age—valves stick and wires shake loose. Preventative maintenance reveals minor issues that a technician can correct today before it requires a major service callout tomorrow.
Using a quick fix – Incomplete solutions mask larger issues. Consider sensor drift, which can be corrected using an offset. The underlying problem, however, may be the sensor itself or the wiring connecting the sensor to the BAS.
Access difficulties – Sometimes, equipment doesn’t receive proper attention simply because it’s not easy to access. There’s usually that one valve in the ceiling, somewhere that nobody was ever able to reach since it was installed. Inevitably, it’s the one that needs attention.
Fixing Control System Issues in Real-Time
BAS control problems lead to wasted energy, uncomfortable tenants, and excessive wear and tear on the equipment. The way to keep things working properly is to find and correct deficiencies in real-time.
During maintenance, MACC technicians take the time to go through a system step-by-step, searching for and investigating each component sequentially.
First, a technician reviews the trends using the BAS interface, looking for abnormal or unexpected readings or alarms. Then they move on to examine the physical equipment and verify that it’s working the way it’s supposed to.
Searching below the surface
Even though things might look good on screen, that’s only a tiny part of the story. Proper maintenance requires hands and eyes on the equipment itself.
BAS technicians can solve plenty of problems simply by tightening screws, fastening plugs, and re-pulling damaged wires—things that aren’t obvious by looking at a laptop. MACC’s technicians focus on inspecting equipment to find the root cause of a problem.
For example, if a sensor drifts off its setpoints, applying an offset is a quick and easy way to correct it. However, by disconnecting the wires to the sensor and examining it, a technician may be able to find—and fix—the situation that caused the drift in the first place.
Thorough planning, thorough solutions
Using customized maintenance checklists, MACC systematically examines and signs off on every part of a system. If they discover a deficiency, they address it immediately (if possible) or note it on a separate work order.
Keeping comprehensive records is an integral part of future maintenance planning. When technicians know what to expect, it helps them plan for the time and parts to get the job done right.
For example, getting scaffolding prepared to safely inspect that valve in the ceiling that doesn’t get much attention.
Get MACC’s Expert Technicians Working For You
MACC have decades of experience installing, servicing, repairing, and retrofitting BAS systems for clients across the Mid-Atlantic region. As proponents of open systems, they are not tied to any one manufacturer.
MACC’s thorough BAS maintenance approach helps extend equipment life and ensures your system delivers superior performance and energy savings.
https://info.midatlanticcontrols.com/blog/uncover-control-system-issues-in-real-time