Two Excellent Production Line Uses for RFID
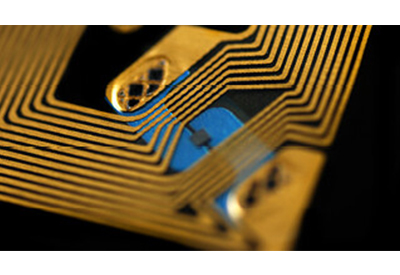
February 1, 2021
Radio-frequency identification (RFID) isn’t something that every manufacturer takes advantage of, but it can nonetheless lead to greater operational efficiency in a variety of applications. Even if you’re currently finding your needs met with barcoding, safety light curtains and other strategies, it might be worthwhile to consider how RFID might make some improvements.
How does RFID work?
An RFID system consists of a tag, an interrogator or reader with an antenna. The tag is made up of a microchip and an antenna, with the latter being tuned to receive electromagnetic waves emitted by the reader. The tag draws power from field created by the reader and uses it to power the microchip’s circuits, and the chip then modulates the waves that the tag sends back to the reader and the reader converts the new waves into digital data.
RFID-based solutions for traceability
Unlike the barcodes in direct part marks (DPMs) and printed labels, RFID tags let you write information as well as read it. If you need to update information regularly as part of your traceability solution, you might want to consider RFID, since it gives you more options for gathering data to help with process optimization.
For instance, if you have several tools performing the same function, and you need to figure out which one does the best job, you can record production test results and the identifier of the particular tool used into the RFID tag. Then you can aggregate the data to visualize quality trends for thousands of parts throughout the line and the tools used to make them.
RFID also gives you much more flexibility with respect to positioning. With barcodes, it’s essential to remove any obstacles between the code and the reader. With RFID, on the other hand, you can have objects standing between the reader and the tag as long as they aren’t made of metal and don’t have a high level of water content.
For more ways that RFID can improve traceability options, check out this blog post on the topic.
Non-contact door switches using RFID
A non-contact option for safety door switches can make standards compliance much easier. According to ISO 14119:2003, certain measures must be taken to ensure that machine operators have no easy way to get around the safeguarding installed on hazardous equipment. Unfortunately, single-keyed door switches can be easily bypassed.
Fortunately, non-contact door switches that use RFID technology (like the Omron D40R Series) are an easy way to upgrade machine safety solutions, meet risk reduction strategies, and keep operators and maintenance staff safer without lowering productivity. (This is described in detail in a past blog post.)
The IP69K-rated D40R Series combines RFID coding technology with standard mounting sizes. Both basic and uniquely coded models are available, the latter of which provides high tamper resistance in accordance with ISO 14119. Using RFID lets manufacturers choose a unique codification on a door so that it can’t be bypassed without the exact code.
https://automation.omron.com/en/us/blog/uses-for-rfid-technology