What’s Just Around the Corner in Visualization?
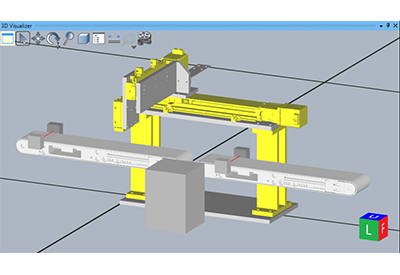
December 7, 2020
Omron are always looking towards the future and taking steps to get there. They know that manufacturers could benefit greatly from stimulating their production equipment’s functionality before constructing it. Although this is a challenging endeavor, Omron are tackling it by bringing logic emulation and machine simulation under a single umbrella.
Traditional solutions typically require multiple software packages or must be externally tied to a physical programmable logic controller (PLC). These tend to be cumbersome and error-prone, particularly when the user must toggle back and forth between windows to view different parts of the system and make the necessary changes.
Going forward, the goal is to combine everything into a single software package so that the user can import 3D CAD models directly into one integrated development environment (IDE) and test out an idea with just a few mouse clicks. Let’s take a look at how that could work.
From 3D simulation to “digital twins”
Digital twins are self-updating models of physical systems that integrate artificial intelligence algorithms and data from Internet of Things (IoT) technologies (such as smart sensors) with spatial network graphs. As the physical counterpart changes, the digital twin changes in real time to match the source’s status.
Ideally, the visualization of a production line will constitute a true digital twin. To create what could be considered a digital twin, a simulator must accurately capture accurate cycles times with physics calculations and replicate the performance of all hardware components. A fully functional logic simulator is also required to verify a process’s ladder or structured text logic
Since visualization depends on data gathered from simulation and emulation, it’s essential for both of the latter processes to be as accurate as possible and to be tied together seamlessly. This means that “fudge factors” – assumptions that are made because the actual values are unknown – need to be minimized.
Why combine everything in one?
Given the significant challenges of achieving complete motion and robotics visualization, it begs the question of why we should bother to do so. There are several reasons. First of all, today’s consumer demand requires increasing amounts of customization, and manufacturers need less expensive and less time-consuming ways to test new changes in their production sites.
Secondly, many companies are trying to get work done remotely whenever possible. If everyone involved in a project needs to have an actual PLC sitting on their desk, remote testing gets expensive. It’s much more cost-effective for programmers to leverage a strong PLC simulation program and share complete 3D visualization models with each other.
Omron’s Sysmac Studio simplifies visualization by combining all automation needs under a single platform.
https://automation.omron.com/en/us/blog/3d-simulation-visualization-sysmac