What is Panel Mount?

June 15, 2020
By: Wendy Jane Preston, Marketing Engineer at Harwin
Definition of Panel Mount
Panel mountis a mechanical feature or features built into the design of a connector half. It allows the connector to be secured to an equipment panel, external case or enclosure. Often (but not always), connectors fitted with panel mount features will be cable connectors.
How does panel mount work?
There are three types of panel mount positions:
- External or rear-face mounting (first image below) – the bulk of the connector is on the outside of the equipment box, and the panel is in contact with a rear surface of the connector.
- Internal or front-face mounting (second image below) – the bulk of the connector is on the inside of the equipment box, and the panel is in contact with a front surface of the connector.
- Side mount (third image below) – the connector housing is attached to the panel in a ‘horizontal’ orientation, more of a securing method than a connection from the inside to the outside of an enclosure.
When is it not panel mount?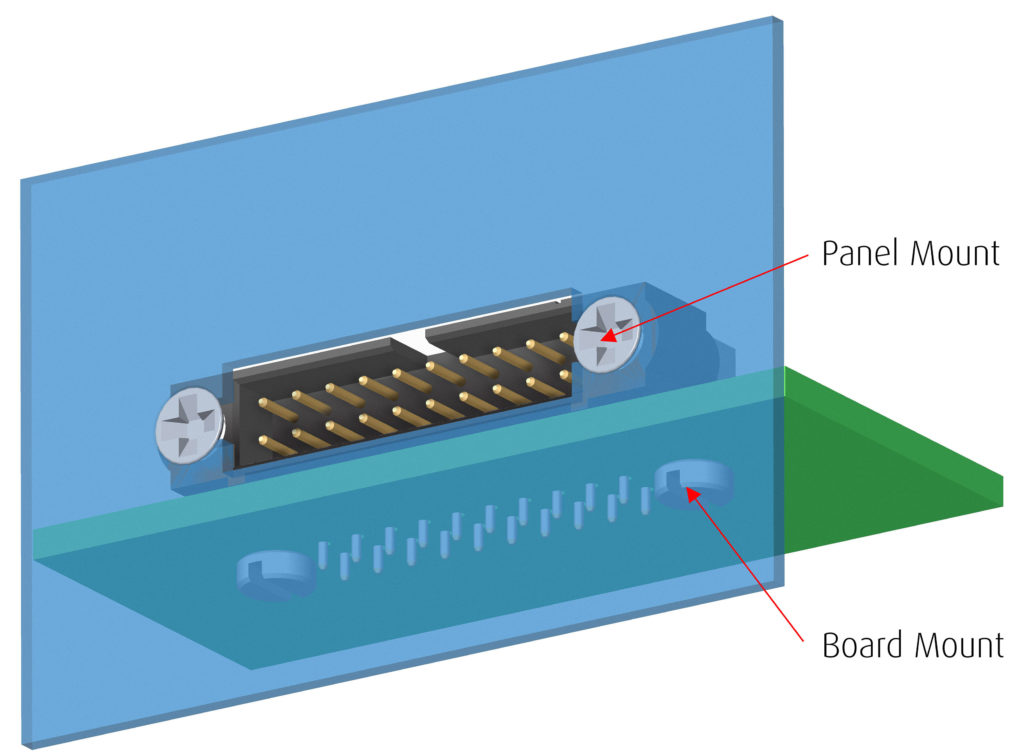
Most manufacturers distinguish between panel mount and board mount.
Board mount devices are additional screws/bolts/nuts or latching mechanisms fitted to a throughboard or surface mount connector – not a cable connector. These secure the connector to the same PCB where the electrical soldering connection is made. Board mount helps lower stress on the solder terminations by transmitting forces through a separate mechanical connection to the PCB.
It’s possible for a connector design to incorporate both panel mount and board mount, fixing to both a PCB and an external enclosure at right angles. It’s also possible to use the same hardware as panel mount hardware – if it’s not reducing stress on the solder joints, but just fixing the connector to the PCB, it’s panel mount.
When do I use panel mount?
When you want to make a connection between the inside and the outside of an enclosure, you need to have a hole in the enclosure wall (or panel) to feed the connection through. If the whole system is fit-and-forget (install once and never replace anything), then there’s no reason why you can’t have a bunch of cables going through this hole to transfer your signal and/or power. It works for your satellite/cable TV/antenna at home! Just make sure you line the edges of the enclosure hole to protect the cables.
However, if you want to be able to plug and unplug your enclosure at any time, or they are being made at different locations, then the most convenient method is to have the connection half built into one side of the enclosure. The enclosure will have a hole or cut-out for the connector to sit in (specified by the connector manufacturer). The inside electronics are wired to the back of the panel mount connector, and the connector is then fixed into the cut-out.
What are the advantages of panel mount?
- By having the connector attached to the panel, there is no external strain on the electrical connections on the back of the connector. This will lower the risk of failure and improve the life of your device.
- You can safely allow untrained users to connect and disconnect cables – think of the connections in the back of your PC, these are all panel mount.
- It’s also possible to design whole modules as replaceable items in smaller enclosures, and keep the devices inside each box safe from tampering.
Are there any disadvantages to panel mount?
Panel mount connectors will require a bigger cut-out in your panel, more than just a hole for the cables. On very small devices, it might make sense to feed the cables out through the panel hole and have a mating cable connector hanging off the end.
This panel mount has no mechanical fixing
Connectors can also be panel mounted with glue or other adhesive methods (rather than mechanical fixings). Or, the PCB with the connector is mounted very closely and precisely to the opening in the panel. For example, your USB and headphone connections in your smartphone and similar devices.
However, for applications in more demanding environments, we’d recommend mechanical panel mount to prevent the connector moving away from the panel at the first bump. It’s important when specifying your panel connections to understand your environmental considerations.
For more information on panel mount connetors, visit: https://www.harwin.com/