Will Industrial HMIs go touchless?
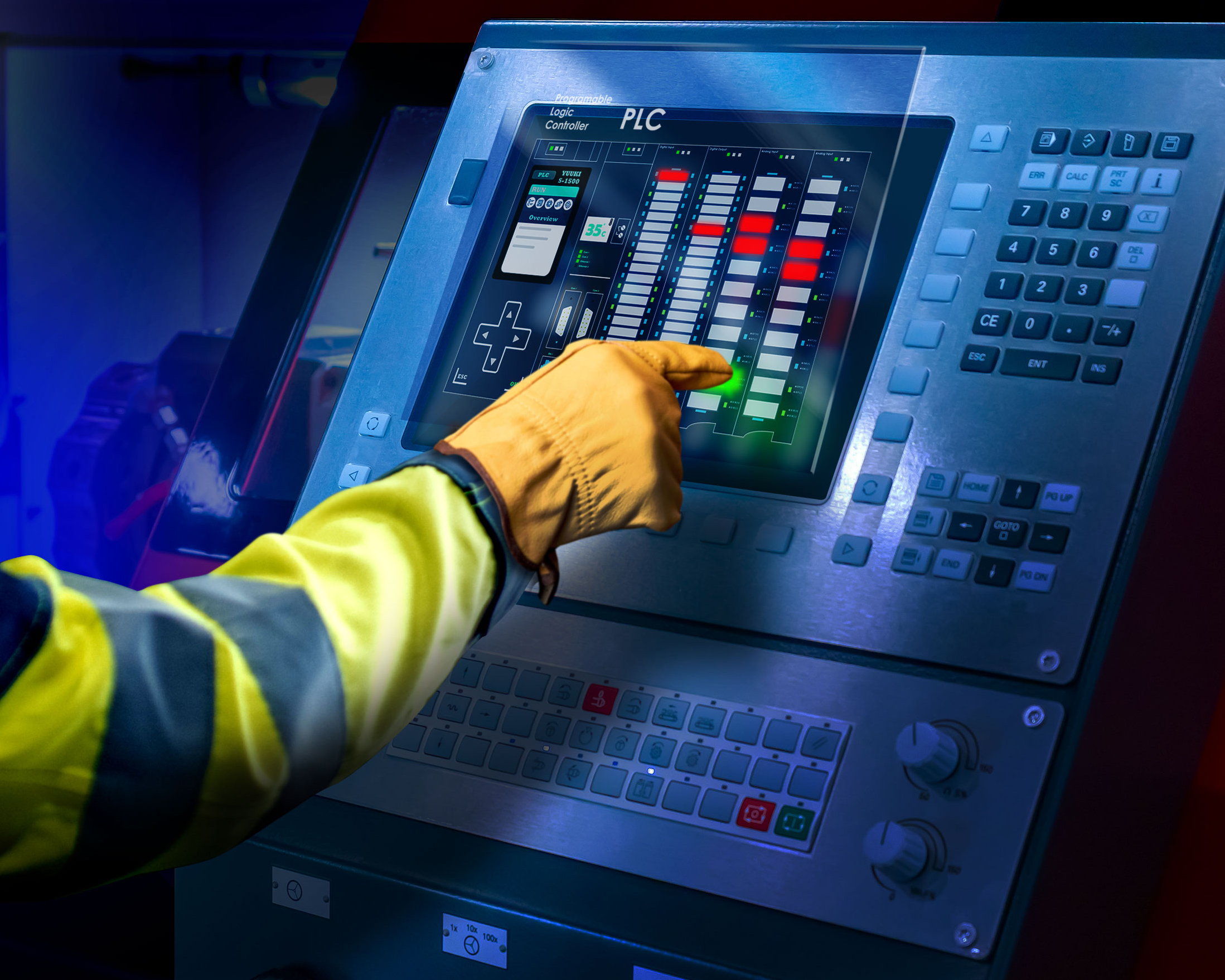
July 17, 2023
Human-machine interfaces (HMIs) are a crucial component of industrial control systems, as they allow operators to interact with and monitor the performance of industrial equipment. In recent years, there has been a growing interest in touchless technology, which eliminates the need for physical contact between the operator and the interface. This technology has many benefits, such as improved hygiene, greater reliability, and increased safety. As a result, the question of whether industrial HMIs will eventually transition to touchless technology is a pertinent one.
Benefits
The biggest advantage of touchless technology is improved hygiene. Industrial settings, such as factories and power plants, can be dirty and hazardous environments, and traditional HMIs can be a breeding ground for bacteria and other harmful microorganisms. By eliminating the need for physical contact with the interface, touchless technology can help reduce the spread of germs and other pathogens.
Another benefit of touchless technology is improved reliability. Traditional HMIs rely on mechanical components, such as buttons, switches or touchscreens, that can be damaged or wear out over time. Touchless technology, on the other hand, relies on non-contact sensors, including infrared and ultrasonic sensors, which are more durable and less prone to failure.
Increased safety is another benefit of touchless technology. Industrial settings can be dangerous places, and traditional HMIs can present a safety hazard, as operators may have to reach over moving machinery or into dangerous areas to access the interface. Touchless technology can help eliminate these hazards, as operators can interact with the interface from a safe distance.
Challenges
The implementation of touchless HMIs in industrial settings can be challenging, as the technology is relatively new and still developing. Touchless technology has limitations, such as cost and complexity. Touchless technology often requires specialized hardware and software, which can be more expensive than traditional mechanical interfaces. Additionally, touchless technology can be more complex to implement and maintain, which can present a challenge for some industrial facilities.
Despite the challenges, more and more companies are exploring and implementing the use of touchless HMIs in industrial settings.
Technology
There are several technologies that are enabling touchless human-machine interfaces (HMIs) in industrial settings. Some of the most commonly used technologies include:
• Infrared (IR) sensors: These sensors emit infrared light and detect the reflection from an object to detect the presence and position of an operator. IR sensors are widely used in touchless HMIs because they are inexpensive, reliable, and easy to implement.
• Ultrasonic sensors: These sensors use high-frequency sound waves to detect the presence and position of an operator. Ultrasonic sensors are commonly used in touchless HMIs for industrial applications because they are relatively inexpensive, reliable, and easy to implement.
• Image-based sensors: These sensors use cameras and machine vision algorithms to detect the presence and position of an operator. Image-based sensors can be more complex and expensive to implement than IR and ultrasonic sensors, but they can provide higher resolution and accuracy.
• LiDAR sensors: LiDAR (Light Detection and Ranging) sensors, uses laser beams to detect and track objects. LiDAR technology can enable touchless HMI by using the 3D mapping and scanning capabilities.
• Facial Recognition: Some touchless HMI systems are using facial recognition technology. This technology uses cameras and computer vision algorithms to identify a person based on their facial features.
• Gesture recognition: this technology uses motion sensors such as infrared cameras and depth sensors, to track the gestures of a user. This can be used to navigate and control the interface without touching it.
• Voice Recognition: some touchless HMI systems are using voice recognition technology. This technology enables users to interact with the system using voice commands.
The technology used for touchless HMI systems depends on the specific requirements of the application, the environment and the desired level of accuracy and interaction. Some system may use a combination of these technologies.
Applications
Touchless human-machine interfaces (HMIs) have already been implemented into many industrial applications. Common industrial applications utilizing touchless HMI technology include process control, manufacturing, and energy management. For example, in process control, touchless HMIs can be used to control the flow rate of liquids or gases, adjust the temperature of industrial processes, and monitor the performance of equipment. In manufacturing, touchless HMIs can be used to control the movement of robots and other automated equipment, monitor the quality of products, and adjust production lines.
Additionally, in the Energy Management domain, touchless HMI’s have been used to monitor energy consumption, control lighting and temperature and even access control to the facility.
Conclusion
While touchless technology has many benefits, such as improved hygiene, improved reliability, and increased safety, it also has its own limitations, such as cost and complexity. It’s a matter of evaluating the pros and cons, and determining if the benefits outweigh the costs in the specific case of a factory or industry. It is likely that touchless technology will become more prevalent in industrial settings, but it may not completely replace traditional HMIs. Instead, it is likely that touchless technology will be used in conjunction with traditional interfaces, as a complement rather than a replacement