What is a Digital Twin?
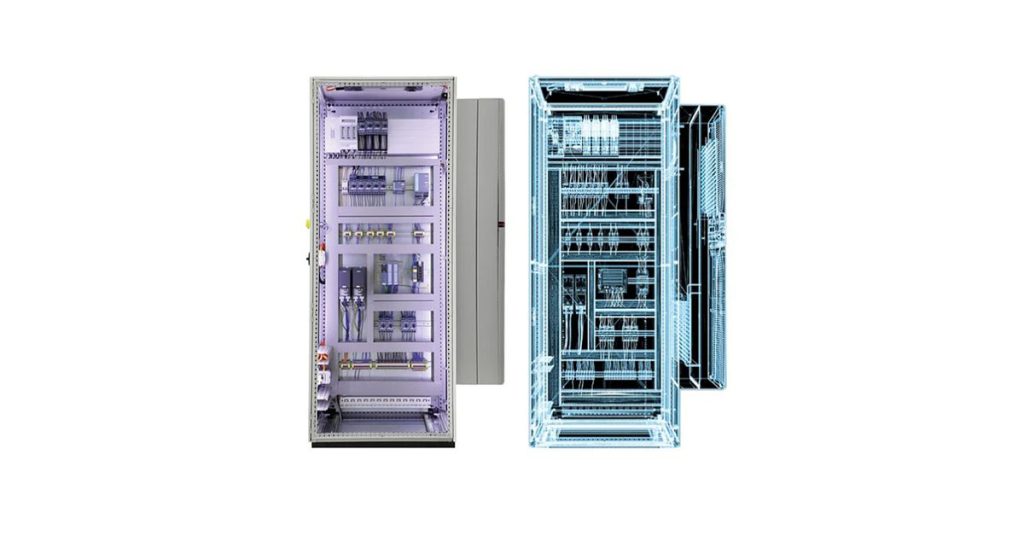
December 4, 2023
By Sean Mulherrin, International Solutions Architect, EPLAN
A digital twin is a virtual representation of an object or system that contain real-time data and information that allow engineers to assess a design without the need for a real-world object.
1. How are digital twins used?
This digital version can be used to measure, analyze, predict, control, or optimize its placement in the physical world – i.e., during product development or inspection, and postproduction to enable effective troubleshooting while minimizing downtime.
Digital twins can also be used to facilitate communication between different stakeholders who may need access to a product or system in different locations. Using Augmented Reality, the digital twin can be brought to life prior to being built.
2. How detailed are digital twins?
Digital twins can include a range of advanced features, such as 1:1 scale 3D models of the physical object. The level of detail and like-for-like accuracy are tailored to the needs of the application. Digital twins are used in a wide range of industries, from engineering, manufacturing and healthcare to ‘smart city’ urban planning.
3. How is digital twin technology used in electrical engineering?
Digital twin technology is gaining popularity as a valuable design tool for engineering, asset management and predictive maintenance applications. Within electrical engineering, digital twins are designed and created using special electrical computer-aided design (ECAD) software that is tailored to the individual application. This type of engineering software normally uses a combination of 3D design tools and other data sources to create a highly accurate representation within the software environment.
Digital twin technology has immense potential for driving innovation in product design and development for manufacturers, as well as generating efficiencies in operations and maintenance. With its accurate data, digital twins are transforming how businesses develop, manage, monitor and optimize their products or services, to reduce costs and enhance customer experiences.
4. Digital twins in product development
Digital twins enable engineers to conceptualize and build better products in a shorter time by reducing their dependence on physical prototypes – which can be expensive and time-consuming to produce. With digital twins, organizations can also assess a wider range of possible scenarios than would be feasible in a physical testing environment, reducing the overall design cycle and lowering overheads. By leveraging the power of digital twins to streamline the design and engineering processes at every stage of manufacturing and operation, businesses can significantly raise their productivity and market responsiveness.
In engineering and manufacturing, digital twin technology is mostly used to create two types of digital applications: Component Twins/Part Twins and Asset Twins:
1) Component Twins/Part Twins are digital representations of individual components, parts or subsystems, such as a PLC card, circuit breaker or mechanical components. Within a 3D ECAD software environment, these components can be easily viewed and assessed before being placed into an electrical enclosure.
2) Asset Twins are digital models that replicate an entire asset such as an electrical enclosure. Asset twins provide valuable insights into how an asset may function within its intended environment, for example, by highlighting potential hotspots that help optimize energy efficiency and performance and minimize risk.
Other benefits of using asset twins in electrical panel design include collision control, which ensures all components will fit into an enclosure, and connection features which allow designers to find the most optimum wiring route and decrease wire wastage.
5. Digital twin engineering from EPLAN
EPLAN gives design engineers all the 3D tools they need to create complex and highly detailed digital twins for electrical control cabinets. The software allows engineers to visualize how components will fit into the cabinet, identify possible collisions, find the optimum wiring route, highlight required mounting clearances, and check provide cooling to the potential hot spots.
