Case Study: Forced-Air Ventilation of Electrical Enclosures in a Food Processing Facility
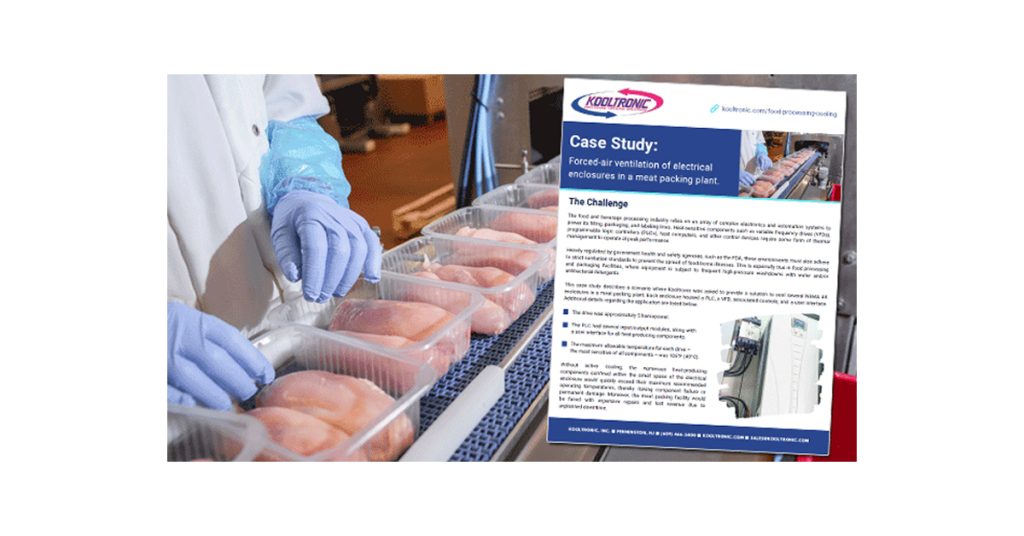
June 12, 2024
The Challenge
The food and beverage processing industry relies on an array of complex electronics and automation systems to power its filling, packaging, and labeling lines. Heat-sensitive components such as variable frequency drives (VFDs), programmable logic controllers (PLCs), host computers, and other control devices require some form of thermal management to operate at peak performance.
Heavily regulated by government health and safety agencies, such as the FDA, these environments must also adhere to strict sanitation standards to prevent the spread of food-borne illnesses. This is especially true in food processing and packaging facilities, where equipment is subject to frequent high-pressure washdowns with water and/or antibacterial detergents.
This case study describes a scenario where Kooltronic was asked to provide a solution to cool several NEMA 4X enclosures in a meat packing plant. Each enclosure housed a PLC, a VFD, associated controls, and a user interface.
Additional details regarding the application are listed below:
- The drive was approximately 5 horsepower.
- The PLC had several input/output modules, along with a user interface for all heat-producing components.
- The maximum allowable temperature for each drive – the most sensitive of all components – was 105°F (40°C).
Without active cooling, the numerous heat-producing components confined within the small space of the electrical enclosure would quickly exceed their maximum recommended operating temperatures, thereby risking component failure or permanent damage. Moreover, the meat packing facility would be faced with expensive repairs and lost revenue due to unplanned downtime.
Narrowing the Options
With the electrical components of the meat packing plant being housed in a stainless steel NEMA 4X-rated enclosure, it was required that the Kooltronic thermal management solution also be rated NEMA 4X. Installing a NEMA 4X-rated cooling unit would provide the highest level of protection for the heat-sensitive components and ensure compliance with regulatory agencies.
To reduce the damaging heat within the electrical enclosure there were two possible solutions:
- The first option was the use of a very small closed loop air conditioner, designed for NEMA-type 4X enclosures and sized to output enough cooling capacity for the cabinet’s heat load.
- An alternate means for remediating the excess heat was to use an air-moving product to circulate clean (filtered) ambient air from the room environment throughout the enclosure, while not permitting the maximum internal temperature to exceed the requirement.
Choosing the Right Solution
After consultation, Kooltronic engineers learned two important factors about the application:
- The enclosure was not insulated. It would, therefore, continuously dissipate some heat through its sheet metal surfaces. This heat loss could be supplemented by moving a sufficient volume of filtered air through the enclosure (over the heat-producing components) and transferring it into the facility’s air handling system.
- Under most conditions, the VFD was not operating at its maximum horsepower and, by using less energy, its heat loss and subsequent heat gain to the enclosure was minimal.
With this additional insight, the Kooltronic engineering team was able to recommend a solution that would accomplish all project requirements with several added benefits.
The enclosure cooling solution consisted of a single inlet Filter Grille and two Guardian Series Filter Fans (pictured above) positioned at opposite ends of the enclosure. With a NEMA 4X rating, the stainless steel Guardian Series Filter Fans and Filter Grille can be washed down without water ingress to the electrical enclosure. Kooltronic engineers took the solution a step further by incorporating a thermostat that automatically cycled the filter fans off whenever the temperature inside the enclosure reached a desired range of 75°F to 80°F (23°C to 27°C).
Summary
After carefully considering the project specifications and environmental factors, Kooltronic delivered an enclosure cooling solution that exceeded the customer’s expectations by offering lower cost, greater reliability (due to the simplicity of air-moving devices), and more energy efficiency
