Safely Navigating the Deployment of Autonomous Mobile Robots in Your Facility
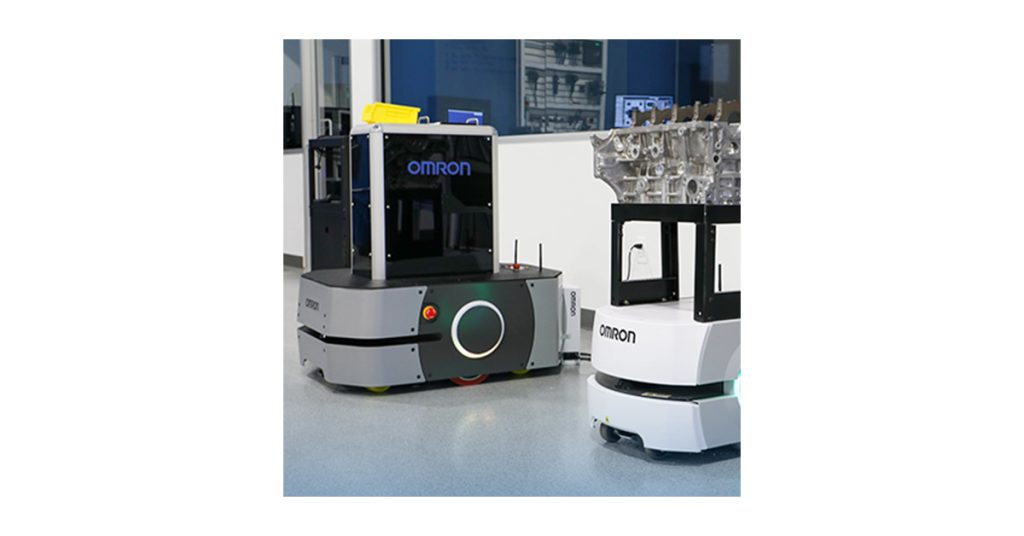
November 6, 2023
The integration of Autonomous Mobile Robots (AMRs) into your facility’s operations can offer a multitude of benefits, such as increased efficiency and productivity. However, ensuring the safety of these robots and those who interact with them is paramount.
This blog post will delve into key safety considerations for organizations and end-users when deploying AMRs in their facilities, with a focus on the application environment.
Assess Your Facility’s Unique Environment
If you’re deploying AMRs in a busy manufacturing facility, you’ll want to consider the layout of machinery, assembly lines, and the flow of materials. In a hospital setting, the presence of patients, medical equipment, and narrow corridors must be considered.
Action: Conduct a comprehensive facility assessment, mapping out potential hazards and bottlenecks. Identify areas where AMRs will operate and where employees or visitors are most likely to interact with them. Whatever the facility type or application may be, think about where the AMRs will operate both during loading and unloading operations, as well as areas of travel.
Identify and Address Potential Hazards
In a warehouse or manufacturing facility with forklifts, there’s a risk of collisions due to blind corners AMRs cannot sense past or by inattentive drivers. In a healthcare setting or laboratory setting, the robots may be tasked with the transportation of sensitive medical equipment that could be damaged, or samples posing contamination risks.
Action: Tailor your safety measures to the specific risks associated with your application. Consider how AMRs will navigate around potential obstacles and how they’ll interact with other equipment and personnel. You may need to implement additional safety measures beyond the AMR itself to reduce the chances of potential hazards. If there is an intersection, implementing programming to control how an AMR approaches the intersection, adding a signal for fork truck drivers, as well as personnel training are possible ways to reduce potential issues.
In a hospital or laboratory setting where sensitive equipment or samples are being transported, you may need to add provisions to the AMR topper equipment to prevent tampering with the payload when in transit. You could also implement additional tracking routines to alert staff to act if AMR encounters an unforeseen issue that prevents it from completing its task. It’s easy to set up an AMR application to address the expected process when things go as planned, but to make sure your application is successful, planning for unexpected situations is crucial.
Assess Environmental Factors
AMRs are very versatile and can operate in many different facility types, but there are environmental conditions that could create a safety hazard. In a machine shop or manufacturing facility that uses cutting fluids, puddles are common. This can affect a mobile robot’s ability to safely stop if it were to navigate through a puddle due to reduced friction of the drive wheels on the floor.
Many manufacturing facilities and warehouses have loading docks or ramps without guarding where an AMR could potentially drive off. This could not only damage the robot and its payload, but also endanger personnel in the area. Additionally, areas that have low ceiling clearances or equipment with open space underneath like conveyors could result in collisions with AMRs that have taller toppers and payloads.
Action: Assess the environment your mobile robots will be working in and put measures in place to either manage or eliminate hazardous conditions. If puddles are possible, implement increased floor cleaning activities or adjust AMR maps to avoid areas where puddles are common. In facilities where floor drop offs exist, adding guarding to those areas and/or adding sensors to the AMR to detect drop off areas. Similarly, for low hanging obstacles, the addition of sensors to the AMR, such as side lasers, allow the robot to avoid objects not normally detected by a standard AMR.
Prioritize Human-Robot Interaction
Mobile robots can be set up to work without any human interaction, but they can also be powerful tools for human-oriented applications. In a retail environment or restaurant setting, AMRs may move among customers as they deliver pick to order goods or meals to restaurant goers. In a manufacturing plant, robots may work alongside human operators as they drop off components to personnel or pick up finished goods.
Action: In public settings like a retail store or restaurant, you cannot count on people to know how to behave around AMRs, so speeds likely need to be limited. There needs to be an extra margin of safety to account for the unpredictable actions of those people. In a more controlled setting of a manufacturing facility, defining clear boundaries and safe zones for AMRs and personnel.
As well as employee training on safe AMR interaction can reduce possible unsafe conditions. Additionally, in any application where mobile robots will work in close proximity to humans, the addition of audible and visual cues to the AMR that communicate the AMR’s presence and intentions to people nearby can also be helpful in reducing potential safety issues.
Emergency Preparedness
Emergencies can occur in nearly every AMR application, but unlike other automation that is fixed in a location, AMRs operate in areas often shared with facility personnel and vehicles. For example, if there is a fire in a facility that requires evacuation of personnel an AMR in operation could become an obstacle for personnel who are trying to vacate the building. Alternatively, in a situation where a person needs urgent medical attention, an AMR could become an obstacle for medical personnel who are trying to get into the facility.
Action: Implement emergency stop mechanisms that can be activated immediately such as routines that instruct AMRs to move to safe locations that do not obstruct critical exit and entrance paths. Train personnel on how to respond to emergencies, including shutting down AMRs safely and addressing hazardous situations.
Integrating AMRs into your facility requires a thoughtful approach to safety that considers the unique application and environmental challenges you may encounter. By conducting a facility-specific risk assessment, adapting to your environment, prioritizing safe human-robot interaction, and planning for emergency scenarios, you can harness the advantages of AMRs while fostering a safe and secure work environment for all.
A well-planned deployment that prioritizes safety can lead to increased efficiency, reduced risks, and enhanced productivity in your facility.

https://automation.omron.com/en/us/blog/safely-navigating-amr-deployment