Protect Your Electronics With OKW’s UV-Resistant Plastic Enclosures
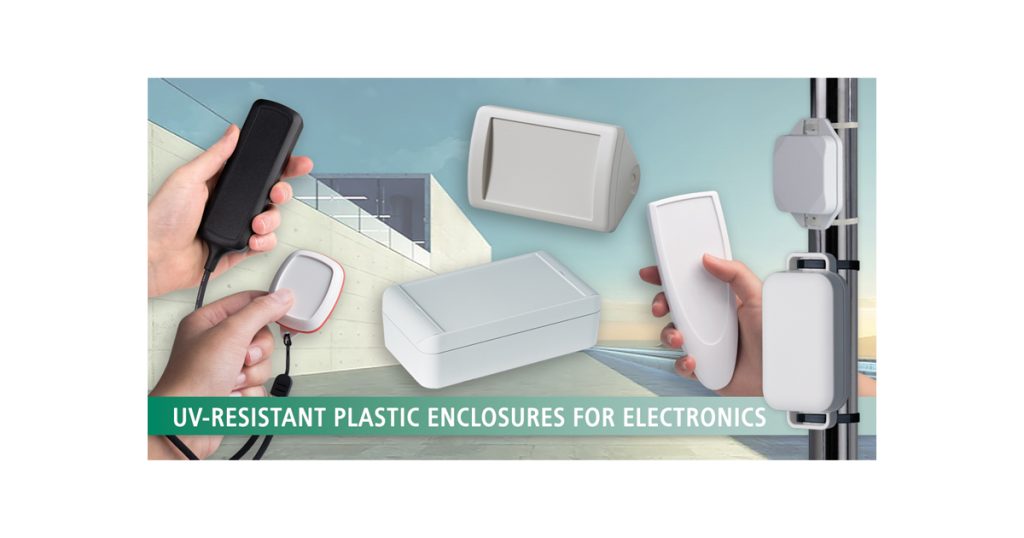
January 6, 2025
UV RAYS – THE INVISIBLE THREAT
Prolonged exposure to sunlight can discolor and degrade plastic enclosures. The ultraviolet (UV) rays cause a photochemical reaction, breaking down the polymer bonds. This process is known as photodegradation.
And don’t just assume this is an outdoor issue. Even enclosures used exclusively indoors can still be susceptible to damage from sunlight. More than 50% of UVA rays can still pass through standard window glass.
Even a dependable plastic such as ABS – which is widely used for electronic enclosures – will suffer a series of microcracks, affecting its appearance. The solution is to specify a UV-stable plastic as an alternative material for your enclosures.
HOW UV LIGHT DAMAGES PLASTICS
Ultraviolet light, part of the electromagnetic spectrum, is divided into three types: UVA, UVB, and UVC. When plastics are exposed to UV light, the energy from the UV rays can excite the polymers’ chains, causing them to break down. Additionally, the presence of oxygen can accelerate this process – leading to faster degradation.
UVA, UVB, and UVC all have different effects on plastics. UVA (320-400 nm) and UVB (280-320 nm) rays can pass through some types of plastic, causing discoloration and brittleness over time. UVC (100-280 nm) is often blocked by most common plastic materials but when it does penetrate, it can cause significant damage due to its higher energy levels.
IMPACT OF UV LIGHT ON PLASTICS
UV light can cause plastics to change color, often resulting in a yellowing or chalky appearance. This is due to the breakdown of chemical bonds within the plastic, leading to changes in the material’s surface layer.
The breakdown of polymer chains makes the plastic more brittle, causing it to crack or shatter more easily. Also, the surface of the plastic can become rough and less glossy, affecting its aesthetic and functional properties.
Some plastics may show signs of degradation within a few months of continuous exposure, while others may take years. The time it takes for UV light to damage and discolor plastics depends on several factors, including the type of plastic and the intensity of UV exposure.
Environmental conditions can also affect the process. Higher temperatures can accelerate the degradation process by increasing the rate of chemical reactions within the plastic. This can lead to faster breakdown of polymer chains, resulting in quicker discoloration and brittleness.
Humidity can also accelerate the degradation process by introducing moisture into the plastic. This moisture can react with the plastic’s chemical structure, speeding up the breakdown of polymer chains. Additionally, the presence of moisture can facilitate the formation of free radicals, which are highly reactive and can cause further damage to the plastic.
SPECIFY UV-STABLE PLASTICS FOR YOUR ENCLOSURES
Acrylonitrile butadiene styrene (ABS) used to be the go-to plastic for enclosures. It’s a tough and reliable thermoplastic that resists impacts and chemicals, and it has a low melting point so it’s easy to mold. But ABS is vulnerable to UV light – so Acrylonitrile Styrene Acrylate (ASA) was developed as a UV-stable alternative.
ASA copes better with UV rays than ABS due to its composition. ASA replaces the polybutadiene rubber found in ABS with acrylic rubber, which is inherently more UV resistant. This substitution significantly enhances ASA’s UV stability, making it less prone to degradation and discoloration.
ASA retains many of ABS’s desirable properties – such as strength, resilience and ease of manufacturing – while adding superior resistance to UV light. It also withstands heat, rain and temperature fluctuations better, making it a smart choice for protecting outdoor electronics. Furthermore, ASA also has a better flammability rating: UL 94 V-0, compared with UL 94 HB for ABS.
Need a more durable plastic that’s still UV stable? Look for enclosures moulded from an ASA+PC blend. Polycarbonate (PC) is an extremely robust plastic that is used to manufacture riot shields, bullet-proof glass and CDs. Combining it with ASA gives you the best of both worlds.
View guide to plastics for enclosures
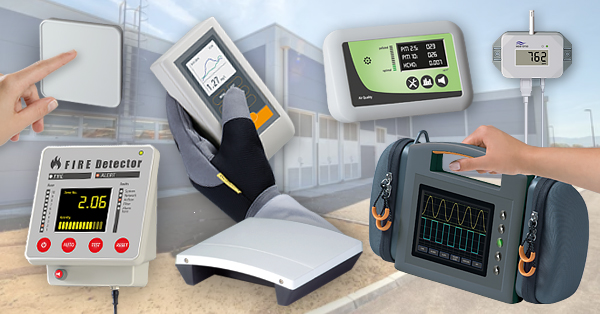
SPECIFYING UV-STABLE ASA ENCLOSURES
In recent years, OKW has specified ASA or ASA+PC – rather than ABS – as the standard plastic for many of their enclosures. They include models such as the wristwatch-style BODY-CASE, EVOTEC desktop and wall-mount enclosures, and CONNECT for wired and battery-powered electronics.
Meanwhile, OKW’s CARRYTEC handheld enclosures provide an interesting opportunity for comparison because they’re available in either ABS (UL 94 HB) or ASA+PC (UL 94 V-0) as standard.
But even if your preferred off-the-shelf enclosure isn’t molded from ASA or ASA+PC, you can still specify these polymers as a custom material (please confirm availability). This also enables you to change the standard color of the plastic at the molding stage of the manufacturing process, rather than later on with lacquering (though that too is a good option that offers you an extremely wide choice of colors, finishes and textures).
List of OKW products currently molded in ASA materials as standard:
1). ASA
UL 94 HB (Material name: ROTEC)
2a). ASA+PC-FR
UL 94 V-0 (Material name: LURAN)
- MINI-DATA-BOX – enclosures for miniaturized electronics
- SMART-BOX – IP 66 sealed industrial enclosures
2b). ASA+PC-FR
UL 94 V-0 (Material name: OKW blended ASA)
- CARRYTEC – large handheld enclosures
- CONNECT – handheld enclosures for wired devices
- DATEC-COMPACT – tough IP 65 handheld enclosures
- EASYTEC – fast-mount flanged enclosures
- EVOTEC – universal instrument enclosures
- NET-BOX – low-profile wall-mount enclosures
- PROTEC – sloping-front desktop enclosures
- SLIM-CASE – slim mobile-phone-style enclosures
- SMART-CONTROL – corner-mount enclosures
- SMART-PANEL – wall-mount enclosures for control panels
Materials are correct at the time of publication and are subject to change without notification. Please confirm material type at time of specification or ordering for your particular product selection.
View full range of plastic enclosures
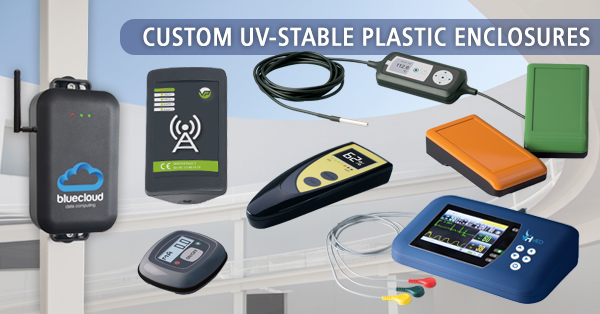
CUSTOMIZED UV-STABLE PLASTIC ENCLOSURES
OKW’s customiszation services also include CNC machining, printing, laser marking, decor foils and RFI/EMI shielding. All the work is carried out in-house. This ensures optimum quality and full accountability throughout the entire manufacturing process. It saves you time, money and administration – and is also better for your indirect carbon footprint because you’re dealing with just one supplier.

https://www.okwenclosures.com/en/news/blog/BLG2501-uv-resistant-electronic-enclosures.htm