Migration Strategies for Supporting Legacy Automation

August 29, 2023
By Scott Martin, KCC Software
When support for legacy systems fades away, there are options to keep them up and running. Experienced systems integrators are well-versed in up-to-date digital platforms to modernize operations with minimal effort.
For a period beginning in the late 1990s, Windows CE was a popular choice as a lightweight operating system for industrial control automation platforms. Now, with the industrial internet of things (IIoT) revolution upon us and new generations of embedded technologies available and rapidly emerging, many end users are in search of a path forward for their legacy systems such as those based on Windows CE. If you can relate, the good news is there are options.
The Windows CE era
In 1996, Microsoft released Windows CE, an operating system for embedded devices. Windows CE, also referred to as Windows Embedded Compact or Windows Embedded CE, emphasized low power usage and minimized memory requirements, making it a good fit to reliably power industrial components in addition to consumer electronics and other uses.

With a user-friendly graphical user interface (GUI), Windows CE enabled industrial devices like programmable logic controllers (PLCs) were able to adopt PC-based controls capabilities such as using flowcharts rather than ladder logic, along with the benefit of additional computing power (Figure 1).
Figure 1: The development of Windows CE enabled development of industrial controllers such as the AutomationDirect WinPLC (left), which provided some PC-like capabilities such as a GUI and flowchart programming, while sharing the same form factor and I/O connectivity as a more traditional AutomationDirect Do-more H2 PLC (right).
One common PLC that ran Windows CE was the WinPLC from AutomationDirect. The WinPLC, in combination with Think & Do programming software, provided a comprehensive package including flowchart logic and visualization. These systems were quite popular in industry, but became less common when Windows CE updates stopped being released in 2013. With support for Windows CE set to expire in late 2023, now is an ideal time to consider options to modernize these systems.
Bridging the gap with modern technology
Even today, many industrial systems continue to run Windows CE. With many of these systems in service reliably for decades, how do you know when an upgrade is really necessary? Aside from the lack of Windows CE support, new hardware availability and data collection are two other factors to consider.
Even though PLCs have long lifecycles—especially compared with PCs—all hardware and software elements ultimately have a limited life. As components are retired and no longer supported, it can be difficult to find replacements. When limited quantities of legacy replacements are available, it’s often at a premium and not economical.
Furthermore, legacy systems running Windows CE are not designed for many of the enhanced data gathering features and connectivity options that are ubiquitous with modern operations. Remote access to legacy systems is rarely possible, and even if it is the cybersecurity concerns alone on an unsupported system are enough to prevent moving forward in this manner.
Timing is everything
The desire to upgrade a system is only one piece of the puzzle, and knowing the right time is another. More often than not, it is best to prepare for an upgrade proactively before your hand is forced. A full system rip and replace—completely decommissioning a legacy system and introducing all new components—can be costly and introduce unnecessary risk, and sometimes this is the only path forward. However, in some cases it is possible to upgrade only the controller, which is usually the most economical and safest way to extend the life of your system and even add new features.
Take advantage of your next planned outage or any upcoming maintenance activities. Combining the upgrade of devices running Windows CE with already scheduled events is less disruptive overall to operations. Another natural time to introduce upgrades is during a move. In these cases, the system will already be offline.
In an industry where the adage “if it’s not broke, don’t fix it” prevails, there are still many good reasons to consider an upgrade. When an opportunity presents itself, it’s best to take advantage.
The power of a long-term approach
One of the most important, yet often overlooked, factors that directly affects future-proofing your operation is selecting the right components. In addition to considerations like overall product features, form-factor, lead-times, cost, technical support, and sustainability, it is crucial to also evaluate industrial automation vendors on their commitment to providing migration strategies as technology, like operating systems, naturally evolves.
A key component in any industrial automation system is the PLC. Widely used for many years, PLC functionality has greatly increased over time, particularly with respect to speed and communication capabilities. It is much easier and cost-effective, if possible, to simply swap out the controller when necessary, rather than also replace the balance of system hardware. However, depending on the supplier this may be easier said than done.
Fortunately, some suppliers design their product portfolios in a manner that addresses this very common scenario, leveraging platforms that leave end users with a viable path forward. One such platform that has proved more than flexible over the years is the DirectLOGIC DL205 Series from AutomationDirect, which is a small modular rack-based PLC platform. This product family is still available and has a massive installed base, although there are other product families which are recommended for new projects.
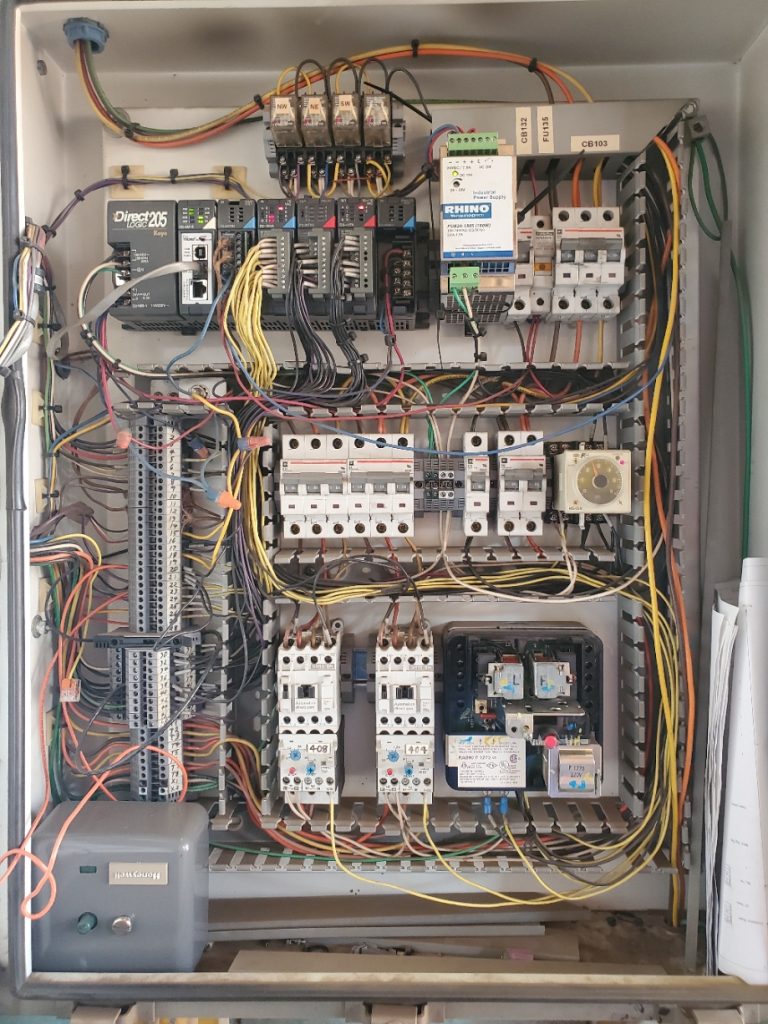
When Windows CE was introduced, the WinPLC was developed as a hybrid PC/PLC controller option for the DL205 family, that added processing power to traditional input/output (I/O) modules of industrial control systems. The WinPLC module conveniently fit into the CPU slot of the DL205 series chassis for seamless integration with DL205 I/O modules (Figure 2).
As Windows CE fell out of favor, the Do-more H2 series of contemporary controllers was released. The H2 series high-performance CPU with significantly faster processing speeds is also compatible with the proven DL205 hardware. The DL205 has ensured the success of legacy systems by remaining adaptable throughout the decades it has been in service.
Figure 2: Because the AutomationDirect WinPLC and the more contemporary Do-more H2 PLC both fit in the CPU slot of the DL205 series chassis, it is possible to upgrade systems to supported technologies while minimizing cutover time and risk.
Leveraging system integrators as partners
Regardless of the industry, it’s critical to have a strategy in place for upgrading legacy control systems. A good strategy minimizes risk, costs, and downtime, while maximizing operations. This challenge is so common throughout the industry that many systems integrators (SIs) specialize in helping end users upgrade their existing automation systems. Partnering with a skilled SI can result in a seamless upgrade without additional downtime. In many instances, even when the programming for an upgrade is manual, it can be performed offsite.
KCC, a SI that focuses on software systems integration, has extensive experience performing upgrades to legacy systems, optimizing the controls for automation systems that produce everything from automotive equipment, to metal fencing, and hard-drive heads.
Recently, KCC was recruited to assist a global appliance manufacturer with several legacy WinPLC Windows CE controllers. This company was relocating operations, and with downtime already planned for the move, this served as an ideal window of opportunity to replace the legacy controllers with a modern and more functional alternative.
KCC and the manufacturer selected the Do-more H2 controller from AutomationDirect, which was an ideal fit with the existing DL205 hardware. The swap yielded significant performance improvements, without the costs of replacing the entire system.

Although the Windows CE controller was programmed using flow chart logic which looks substantially different than PLC ladder logic, it turns out that flow charts are usually heavily documented and readable (Figure 3). With their expertise in software systems, KCC was able to complete most conversion programming offline and the entire project was completed with minimal time on-site for commissioning. This resulted in significant time and labor savings for the manufacturer.
Figure 3: One of the features of Windows CE controllers was the ability to program them using flowchart logic. While there is no automatic method of converting flowcharts into ladder logic when upgrading to a contemporary controller, experienced systems integrators have great success converting these systems rapidly.
Similarly, when a long-term client in the semiconductor industry had an existing installation that included a group of legacy controllers that needed to be compatible with touchscreen human machine interfaces (HMIs), KCC was selected to help. Many of the older touchscreens did not have the corresponding drivers to communicate properly with the newer controllers, but KCC found an easy upgrade path by focusing on modernizing the PLC and then configuring a newer generation of touchscreen HMI for compatibility and functionality. Once again, the Do-more H2 controller was selected as the best fit, with the entire project checking the boxes for a highly functional, low risk, and economical solution.
A clear path forward
If your installation includes the WinPLC or another Windows CE-based legacy controller, don’t despair. Upgrade paths are available and often don’t require extensive downtime or a completely new capital investment. Careful planning now can ensure you have viable options for the future.
Even though support for Windows CE is lapsing, migration doesn’t have to be painful. When it’s time for an upgrade, don’t “win-ce”. Rather, look to proven and trusted suppliers and SIs with a reputation for long-term support of their customers. With AutomationDirect’s extensive portfolio of automation and control products, you’ll have the best options in the industry.
All figures courtesy of KCC Software