How A More Connected Ecosystem Can Help Material Handlers Process More Parcels
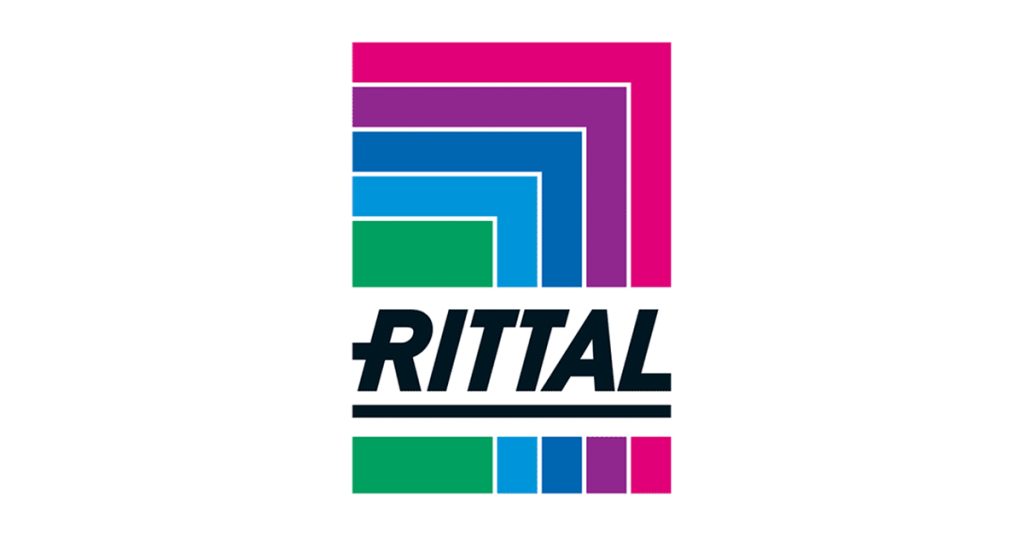
August 8, 2023
If there’s one aspect of the material handling industry that is complicating workflows for warehouses and distribution centers across the country, it’s how difficult it is to predict and plan for sudden increases in the number of parcels in the pipeline. Peak parcel volume can happen at any time, and challenges like labor shortages and increased operational costs only muddy the water material handlers have to cross in optimizing their sorting and distribution processes.
A flexible and versatile industrial automation infrastructure can help material handlers accommodate these shifts quickly and efficiently. However, the ability to scale and adapt automation systems in this manner is made considerably more challenging without a completely digitized, connected ecosystem built on the foundations of Industry 4.0 and IIoT.
With this in mind, let’s look at how a connected ecosystem can help material handlers identify the ideal industrial enclosures for speed, efficiency, and productivity in their warehouses and distribution centers.
A connected ecosystem streamlines the enclosure design process
Speed-to-market is the name of the game in the material handling industry. The faster material handlers can process parcels, or, in some cases, bring new warehouses online either by new construction or retrofitting for automation, the faster they can expand their footprint and grow their market share.
The ability to unlock this speed relies heavily on automation architects leveraging a streamlined industrial enclosure design process that provides unparalleled visibility and transparency into each phase of the planning sequence. This data-driven approach to enclosure design makes it easy to store, retrieve, and share enclosure configuration to accelerate a number of downstream processes.
Rittal’s field-proven approach to standard industrial enclosures — like the Rittal TS 8 modular enclosure or Rittal AX compact enclosure — combined with Eplan’s suite of CAE (computer-aided engineering) software provides automation architects with 3D modeling capabilities to reduce production line errors, account for potential variables in production or customization, and respond to change orders based on considerations such like the need to reduce your automation footprint.
Additionally, Rittal’s emphasis on modular enclosures that use interchangeable parts and panels only increases the configuration flexibility of your automation equipment. And, when paired with a powerful design platform like Eplan, material handlers can overcome a variety of stumbling blocks in the deployment of their automation solutions like prolonged lead times, labor shortages, and supply chain disruptions.
This deeper understanding into the entire enclosure design process also makes it easier and faster to specify the ideal enclosure climate control systems, busbar power distribution panels, and HMI (human machine interface) integrations to optimize the productivity of your warehouse automation systems — and help material handlers process more parcels.
With a connected ecosystem, you can increase the speed, efficiency, and precision of your panel wiring and processing
One of the most mission-critical processes in the industrial enclosure engineering sequence is the processing and wiring of the control panels that help drive the machines in your warehouse. The processing and wiring of these panels requires high degrees of precision in order to avoid machine failures and disruptions in production, and a manual approach is not only time-intensive, but it does not provide the necessary precision or versatility to customize panels based on how they’ll be used in the field.
Rittal Automation Solutions (RAS) provides a suite of tools and fully-automated machines that are designed to reduce the time it takes to manually execute these processes by up to 70%. What’s more, automated panel and wire processing creates a more connected ecosystem by linking the enclosure design and engineering process with the panel wiring process in order to ensure accuracy and quality every step of the way.
For example, the Wire Terminal WT processing and assembly machine can produce 24 to 36 different wires with cross-sections ranging from 0.5 mm² to 6 mm² quickly and with the utmost precision. The new Wire Terminal WT C takes automated wire processing to the next level with a variety of wire output methods, faster throughput times, and the automated labeling, sorting, and transport of wires.
The RAS suite can also help automation create a more connected ecosystem via the automation of the panel modification process.
The Perforex MT MillingTerminal provides fully-automated, fast, precise, and reliable machining (drilling, thread-tapping, and milling) of mounting plates, doors, roof plates, side panels, gland plates, or unibody enclosures. The Perforex MT also leverages an intuitive user interface that makes it fast and easy to operate, and, though the Perforex is compatible with Eplan, it comes standard with its own software to create a more data-driven approach to panel modification.
The acceleration of panel processing and customization can not only help automation architects specifying solutions for material handlers scale their operations based on the quantity of parcels , but it can also help diversify the handler’s operations and create new productive partnerships along the way — for example, Automation and Control Systems LLC (ACS) increased their productivity and customer base by integrating Rittal’s panel and wire modification machines.
Automated industrial enclosure design and panel processing and modification help material handlers process more parcels via a connected ecosystem that optimizes productivity and efficiency. Learn more about how Rittal’s approach to a connected ecosystem can help you unlock new levels of productivity.
