Ready or Not, Industry 4.0 Is Here
January 31, 2023
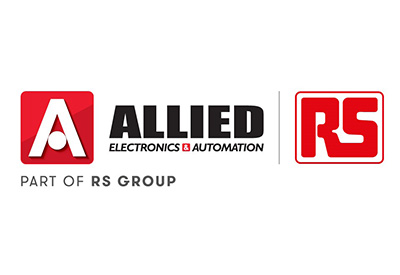
By Abe Fares, OEM Area Sales Manager – Gulf, Eaton
Eaton experts explain how to thoughtfully embrace Industry 4.0 technologies, sharing strategies, considerations, and personal examples to help ensure that your foray into Industry 4.0 starts out on the right foot.
It’s been exciting to see the full potential of the Fourth Industrial Revolution, or Industry 4.0, go from concept to reality. This era’s immediate predecessor, Industry 3.0, represented a quantum leap in manufacturing productivity and efficiency. However, few could have predicted just how quickly the foundations of Industry 3.0 would lead to the technological leaps we see today.
“In the 70s and 80s, we started seeing the advancements of computers and even some introduction of robotics and automation, but if you look at those, they were standalone technologies that were there to maybe complete a task better,” said Eaton’s VP of Industry 4.0 Craig Sutton. “Industry 4.0, however, talks about machines working with machines [known as machine to machine (M2M) communication, which is enabled by the Industrial Internet of Things or IIoT], the collection of data, data analytics, and even the movement into the space of artificial intelligence [AI] and other technologies such as 3D printing.”
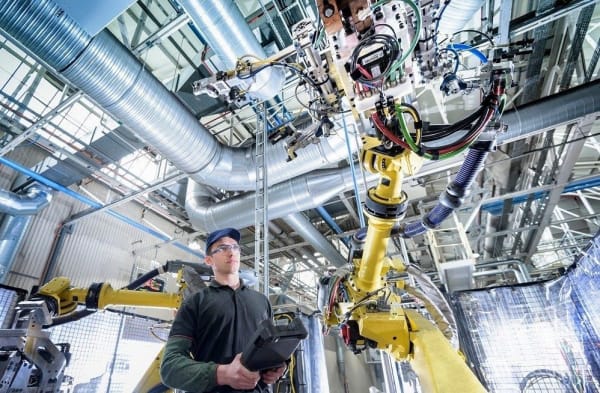
The impact of these trends cannot be overstated. In a 2020 study by The MPI Group, 42% of manufacturing executives surveyed reported an increase in productivity between 6% and 10% from the previous year alone, and 45% predicted a further increase in productivity between 6% and 10% over the next five years. In addition, 19% reported an increase of over 10% from the previous year and predicted an increase of over 10% in the next five years. Company profitability also saw sharp increases; 38% reported a profitability increase between 6% and 10% from the last year, and 42% expected an increase of 6% and 10% over the next five years.
However, at this point in its evolution, Industry 4.0 adoption is about more than just reaping the benefits; it’s become necessary to remain relevant in an increasingly competitive marketplace. According to the same MPI study, approximately half of the executives surveyed said that Industry 4.0 is a competitive differentiator today, and 42% said that it will be in the future.
“The race for digital supremacy is on,” the study read, “and the gap between Industry 4.0 haves and have-nots will likely widen.” If manufacturers don’t thoughtfully consider and adequately invest in Industry 4.0 technologies, there is a good chance that they will soon be left behind.
“It’s not going to be a secret that only Eaton has a handle on,” said Sutton. “We are all in a competitive space, and we all need to be able to prove how we are trying to drive efficiencies and value realization.”
But even if you recognize the necessity of Industry 4.0 adoption, knowing where to start the adoption process is not always as clear. Without careful planning and a proper understanding of your company’s needs, the risk that these costly investments don’t deliver the expected returns can be quite high.
Start With the Data
As much as you might wish there was, there’s no one-size-fits-all approach to successful Industry 4.0 adoption. Therefore, your first steps towards adoption must include a detailed assessment of your operating challenges and the various technologies that could potentially resolve those problems.
“We really want to start with what problems [customers] are having, and what they want to improve,” said Todd Earls, Eaton’s VP of IT Digital Design and Manufacturing. “Is it on on-time delivery? Is it quality? Is it cost? Is it something else within their plant they are having an issue with? And then based on that, we can understand whether a technology, a people, or a process solution is available for each of the problems they may have.”
To cite an example, one of the largest recent challenges shared across the entire manufacturing landscape, including Eaton, was the COVID-19 pandemic. “One of the biggest challenges we had was that not a lot of people were allowed into our factories when the pandemic hit,” said Earls. “We were able to use technologies such as augmented reality and virtual reality to do some things we normally wouldn’t have been able to do.” These things included training that would normally have been done externally, virtual witness testing by customers, and Gemba walks by internal and external parties.
Settling on the right solution for any given challenge, however, will require data — a lot of it. So, data collection, visualization, and analysis should almost always be among the first avenues you consider when planning your entry into Industry 4.0.
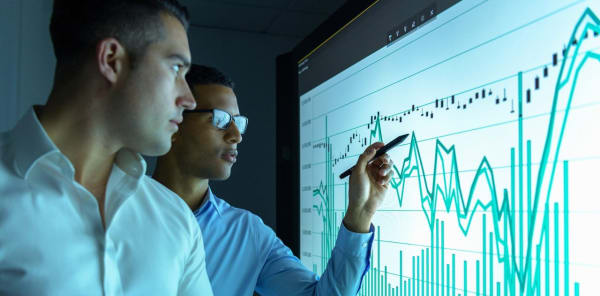
“It’s all based on connectivity,” Earls continued. “That connectivity could include sensors, it could include our own smart products we have at Eaton, or it could include other sources of data dedicated to finding the waste in [customers’] operations for analysis. That’s really where we want to begin.”
This step alone can have enormous benefits. According to Sutton, a recent survey of over 40 manufacturers by McKinsey revealed that factories implementing connected data experienced an increase in output and productivity between 20% and 100%. Additionally, inventory lead time reduction improved between 50% and 60%, translating into clear, direct business impacts on the bottom line.
Keep in mind, however, that radical improvements don’t have to be made overnight. One easy and cost-effective way to begin making marginal connectivity improvements is to upgrade your existing network infrastructure. Eaton offers a variety of products that can help make the transition to a fully interconnected manufacturing ecosystem seamless, including programmable logic controllers, power distribution units, contactors, surge protectors, uninterruptable power supplies, and circuit protection devices as well as its Power Xpert Dashboard user portal and Brightlayer digital platform.
Learn About the New Technologies Industry 4.0 Enables
Data and analysis have inherent value in determining where improvements can be made. Without a broader understanding of exactly what Industry 4.0 technology solutions are now available, it could be difficult to articulate what the perfect solution to an issue might be.
Take, for example, the concept of additive manufacturing, which is more commonly known as 3D printing. Thanks to computer-aided design (CAD) software and 3D object scammers, you now have the ability to create precise geometric shapes in a layer-by-layer form, as opposed to traditional manufacturing techniques that typically require machining or the removal of surplus material.
Additive manufacturing systems can be used to overcome manufacturing challenges including productivity issues, substandard quality control, and even environmental sustainability issues. According to Earls, additive manufacturing can decrease waste and scrap by using only the material required for final products while also opening the door for manufacturers to combine novel materials, designs, and process innovations faster than traditional manufacturing techniques — all of which helps OEMs proactively impact the environment for the better.
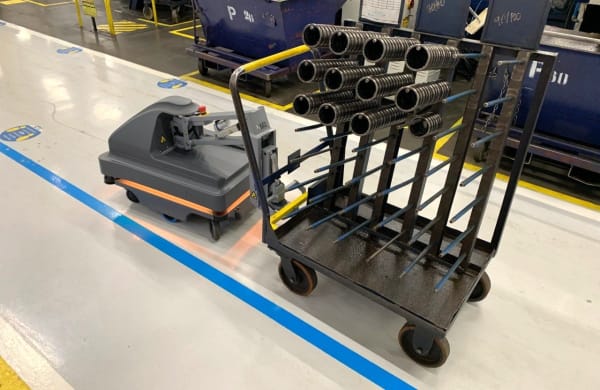
In Eaton’s case, additive manufacturing has been particularly valuable for prototyping tools and quickly creating trial versions of concepts kicked around by product designers or shop floor personnel. With additive manufacturing, “you can try out that idea very quickly without long lead times or lots of investment,” said Sutton. “You can think of it as taking an additive-first approach that allows us to drive down the costs that go into our operations.”
Other topics that are making waves in Industry 4.0 discussions are the advancements being made in the field of cobots (collaborative robots) and autonomous materials movement. Cobots are designed to work alongside humans to improve employee safety while improving quality and productivity, and they all but eliminate the traditional disconnect between humans and automated industrial machinery, which was typically isolated in a cage or cell. Autonomous material movement refers to the use of autonomous guided vehicles (AGVs) or autonomous mobile robots (AMRs) that efficiently move material around factories.
Depending on your needs and challenges, exploring and implementing one or both of these Industry 4.0 technologies can lead to drastic increases in productivity and efficiency.
Don’t Overlook the Risks of Industry 4.0 Adoption
Reward rarely comes without risk, and Industry 4.0 solutions are no exception. It’s important to address these risks in the early stages of embracing Industry 4.0; otherwise, all of your investments could be for naught.
“Connectivity is really the central theme of Industry 4.0,” said Earls, “and connectivity entails connecting in devices such as sensors and machines and other things that contain software. With any software comes vulnerabilities that could impact our entire network at Eaton.”
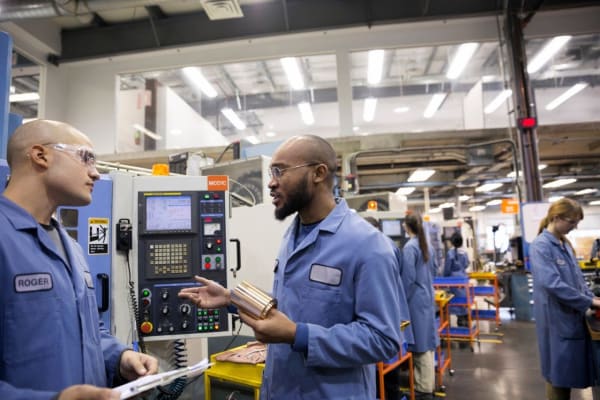
To shore up such vulnerabilities, manufacturers can implement firewalls and other technology controls to prevent cyber breaches from occurring. But it’s even more important to take the added step of ensuring the integrity of the connected devices before use. “During any Industry 4.0 project, we make sure everything is safe and clean before we connect it in, ensuring a secure networking environment within Eaton against any external cybersecurity threats,” Earls continued.
Finally, although many questions remain on this front, it’s also important for you to keep a finger on the pulse of the evolving regulatory environments associated with Industry 4.0 initiatives, including AI, additive manufacturing (which raises some important issues regarding trademarks and copyrights), and cybersecurity. It can sometimes be helpful to involve external and internal auditors to provide assurance, verify conformance to applicable laws or standards, and ease the collaboration between manufacturing executives and their legal departments.
Industry 4.0, A Challenging but Bright Manufacturing Future
It’s no secret that some people have mixed feelings about how quickly Industry 4.0 is changing the manufacturing landscape, and that’s perfectly understandable. Change in any capacity can be difficult, and even overwhelming at times. So, these perspectives are not without validity. In fact, it might be concerning not to feel at least at least some apprehension. But instead of letting these emotions hinder your company from embracing the future, let them fuel your desire to approach Industry 4.0 with care. Don’t make quick investments not rooted in analysis, and don’t adopt what another company is doing just because it works for them. No two Industry 4.0 solutions will be exactly alike.

https://www.alliedelec.com/expert/ready-or-not-industry-4-0-is-here/