Food & Beverage Manufacturing at Scale with MES
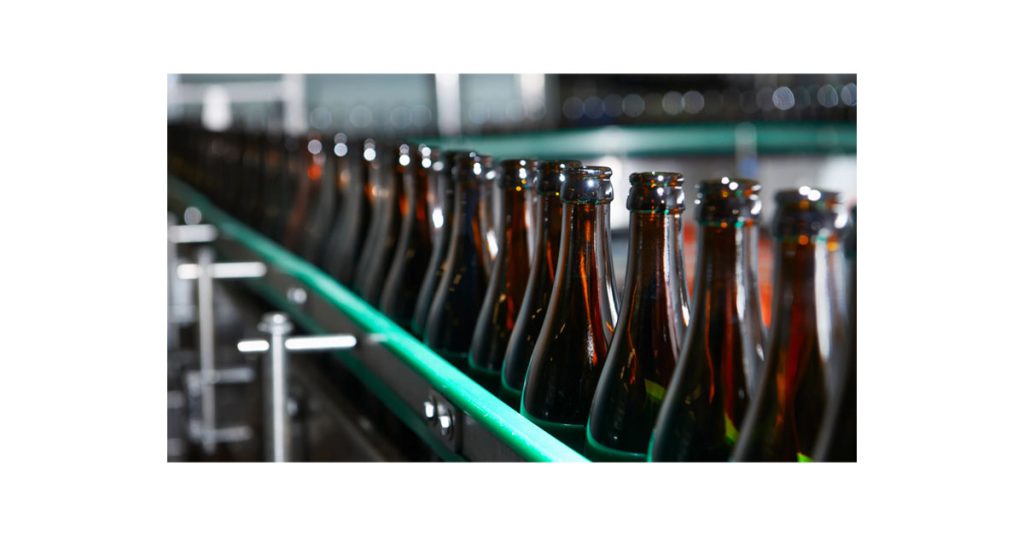
April 5, 2024
By Hayden Foot, Senior Product Manager, Rockwell Automation
External pressures and internal challenges continue to mount for food and beverage and Consumer Packaged Goods (CPG) companies.
Keeping up with evolving and increasingly stringent food health and safety regulations can be complicated. Regulations such as CFR 21 Part 11, Hazard Analysis and Critical Control Point (HACCP) changes and the U.S. Food and Drug Administration (FDA) Food Safety Modernization Act all have increasing requirements on electronic record keeping of quality and traceability records in manufacturing.
Add in ever changing consumer preferences and market challenges like labor shortages, supply chain issues, and the rising costs of ingredients, cybersecurity threats and sustainability requirements all contribute to the squeeze on margins in the CPG industry.
CPG companies are addressing customer expectations for new products and “farm to fork” trends while operating 24/7 at high speeds and high volumes.
Manufacturers often feel limited by their current technology approach and are looking for strategies and technologies to ensure they can modernize and deal with their business challenges and the evolving regulations, while continuing being able to scale and grow their businesses both organically and inorganically.
Common Technology Approaches Often Fall Short
Home-grown systems and legacy technologies may have worked in the past, but don’t have the modern capabilities required to keep up with today’s dynamic environment. It can also be difficult to continue using home-grown systems as your business grows because they are typically not designed to handle high-speed transactions and complex, global operations. These systems can become difficult to maintain and keep up with the constant threat of cybersecurity vulnerabilities.
IoT solutions can address the need for connectivity and real-time insights, but often lack dedicated, industry-specific manufacturing execution system (MES) capabilities such as recipe templates, genealogy, order management, user quality workflows, and data archiving.
Limitations Of Home-Grown Solutions
- Lack of end-to-end visibility and single source of truth: Home-grown solutions typically don’t provide granular details on execution information, limiting your visibility and traceability of complex ingredient mixing models for continuous, batch and discrete processing in CPG manufacturing.
- Significant in-house resource requirements: Building and maintaining one-off solutions requires specialist development expertise. They can be difficult to scale to new lines and facilities and keeping these systems running often hinges on the knowledge of a few people, which introduces risk if there is turnover. Commercial pressures mean manufactures need to prioritize their investments and having resources that develop and maintain solutions often doesn’t align with their core company purpose.
Limitations Of Legacy Solutions
- Risk of errors: Compared to purpose-built solutions, in-house solutions are often less structured and more prone to errors that can result in quality anomalies and production loss.
- Minimal cybersecurity protection: Common cybersecurity practices like penetration testing or threat modeling are not being utilized or are difficult to implement to protect the home-grown solutions exposing ongoing threats.
- Difficulty scaling operations: It can be difficult to continue using home-grown systems as your business begins to grow because they are not designed to handle high-speed transactions or scale to complex, global operations in a modular way.
As a result of these limitations, additional systems are needed to enable the right level of orchestration and automation. This increases complexity, cost, and risk both from upfront integration and ongoing support and maintenance.
Scalable Modern Approach for Modern Times
CPG Manufacturers who need to scale are driven to operate highly automated and highly available plants to meet demand and get the most valuable return on their capital investments. This is why manufacturers need a modern MES solution that can truly suit these needs. The approach should be based on industry standards and best practices to allow for scale, and ease of support and integration to common dependent systems such as ERP and process control systems.
Modern MES solutions are designed to support a full spectrum of enterprise needs including dispatching production, quality operations management, process management, tracking of inventory, with the expected result being accurate and reliable electronic records to achieve productive quality, traceability, and regulatory compliance.
Structured approaches with best practice modeling of equipment and routing supports scale for new lines and plants at both site and enterprise levels. Standards-based integration patterns mean sites and equipment can be integrated in a modular, scalable way.
The benefit of utilizing a dedicated MES solution from a single provider is that all these capabilities would be connected, supported and secure, providing a more holistic visibility into end-to-end processes and a much lower risk approach at scale than would be available utilizing adapted technology approaches.
Learn More
FactoryTalk CPGSuite integrates information among processes, facilities, business systems and suppliers to improve quality enforcement and simplify compliance. It maximizes yield, increases profit margins and has capabilities to adapt faster to market changes. As a result, FactoryTalk CPGSuite is proven to reduce production costs by as much as 18%, improve first pass quality by up to 12% and improve yield while minimizing losses by up to 10%.
Find out how the right MES can connect all processes across locations, enabling data-driven operations, improved productivity, and improved profitability. Register now for the webinar, Optimizing Production at Scale with FactoryTalk CPGSuite.

https://www.rockwellautomation.com/en-us/company/news/blogs/food-and-beverage-mes.html