What Food and Beverage Manufacturers Should Look for in a Wall Mount Enclosure
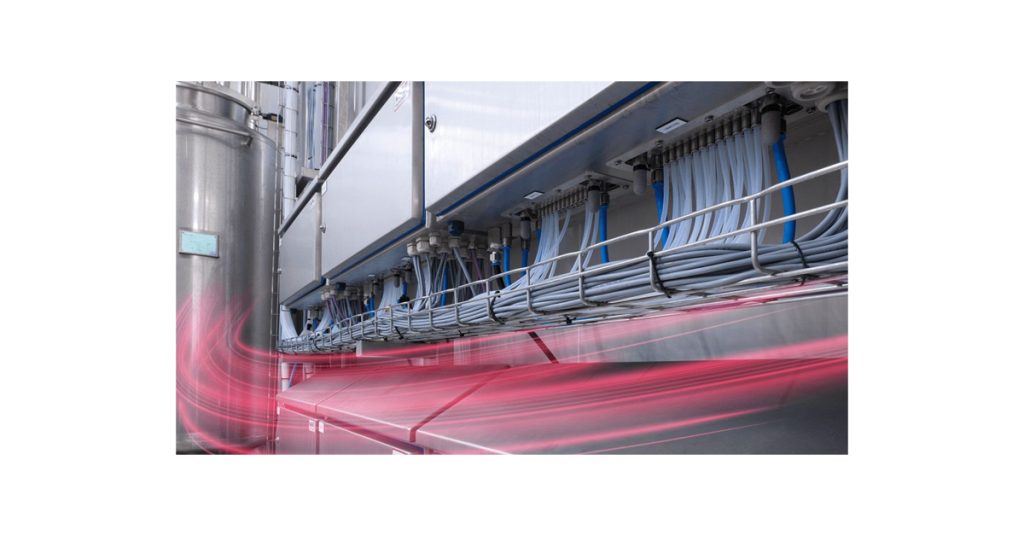
July 19, 2024
Food and beverage manufacturers are currently faced with several unique challenges. Labor shortages, cost increases, and the demand for more varied products — primarily meat and dairy alternatives — are pushing food manufacturers to prioritize agility and flexibility in how they orchestrate their automation infrastructure.
Of course, the hygienic requirements of food and beverage production means manufacturers also need to specify enclosure solutions that help promote high degrees of sanitation and cleanliness.
The combination of these considerations can complicate the process of choosing the right wall mount enclosure to optimize production processes. However, there are a couple of key elements manufacturers can look at to help simplify the decision-making process, and, here, we’ll look at what food and beverage manufacturers should look for in a wall mount enclosure to create a flexible automation infrastructure with the highest hygienic standards.
Wall mount enclosures need to be easily scalable
Scaling production based on market demand is just part of doing business in the food and beverage industry. Whether it’s emerging food trends or the massive growth of the pet food market, manufacturers must be able to scale production or introduce new product lines quickly to keep pace with the competition.
This kind of scalability is dependent on a couple of factors. First, the ability to scale based on demand starts with an end-to-end digitalization of the enclosure design process for real-time insights and visibility into everything from material sourcing to the creation and alteration of panel and enclosure schematics. This approach also creates a more connected ecosystem that allows for real-time schematic changes that enable downstream alterations to enclosure configuration without costly errors or downtime.
This kind of scalability also depends on simplified engineering that allows for rapid enclosure customization and configuration on the facility floor without creating bottlenecks in production.
Rittal’s line of wall mount enclosures can be configured and modified in the Eplan suite of Cloud-based design software for a fast, error-free design process that significantly reduces the need for manual intervention. Digital twins and 3D control panel visualization provide panel builders and installers with streamlined workflows for installing power distribution panels and wiring.
Rittal’s AX line of wall mount enclosures can be easily accessed from the bottom for easy cable and wiring management, and system expansion can be easily done by adding rails to the door, or on the side of the AX enclosure, even for dynamic loads.
Wall mount enclosures need to be corrosion-proof and easy to clean
In more traditional food production plants or high-pressure processing (HPP) facilities, manufacturers need enclosures that can help enhance hygienic standards, while also providing high levels of durability and reliability. What’s more, manufacturers need wall mount enclosures that can seamlessly integrate with existing automation solutions across multiple hygienic zones.
Stainless steel is the construction material of choice for wall mount enclosures in food production facilities for a variety of reasons. Not only does stainless steel help prevent the ingress of water or other potentially harmful solutions, it also helps protect against corrosion or damage from rigorous and frequent washdowns, many of which use harsh solvents and chemicals.
For example, the stainless steel construction of Rittal’s AX KS SS creates a more robust enclosure that can handle the rigors of harsh production applications. For example, the AX KX SS utilizes a slimline enclosure edge fold in combination with a seamless PU foam seal to provide IP 66 protection. In addition, stainless steel engineering offers NEMA 1, 3R, 4, 4X, or 12 ratings.
Stainless steel construction offers the durability and reliability necessary for challenging deployments, and the smooth nature of the stainless steel makes both the AX and KX SS easy to clean and maintain. This makes the AX and KX SS corrosion-proof and easy to clean, which helps manufacturers reduce the likelihood of unplanned maintenance intervals and costs.
Wall mount enclosures need simplified mounting and configuration capabilities
The time and resources required to adequately mount an enclosure can make it difficult for manufacturers to maximize uptime or scale their automation infrastructure. Not only can the mounting process require specialized tooling, it can also limit internal wiring and cable configuration or capacity. Plus, once the enclosure is mounted, it can be challenging to integrate enclosure accessories to optimize performance or adapt to changes in production parameters.
The highly competitive nature of the food and beverage space exacerbates these pain points, which is why producers need to choose wall mount enclosures that are quick and easy to mount. This helps accelerate speed-to-market, and it also helps overcome labor shortages and reduce the costs and resources necessary to deploy wall mount enclosures.
Rittal’s wall mount enclosures use a simplified mounting panel that is easy to pre-attach and secure. A standard pitch pattern makes component assembly faster and easier than ever before without the need for specialized tooling or equipment.
What’s more, punch points embossed on the rear panel streamline the mounting process, and the tool-free nature of the door assembly process further accelerates the ability to mount and integrate the enclosure into an automation system.
With the right wall mount enclosure, food and beverage manufacturers can optimize productivity and efficiency while also serving up a better quality product to consumers. Rittal’s approach to wall mount enclosure engineering can help these producers get to where they need to go.
