What Food & Beverage Manufacturers Need to Know About Energy-Efficient Enclosure Cooling
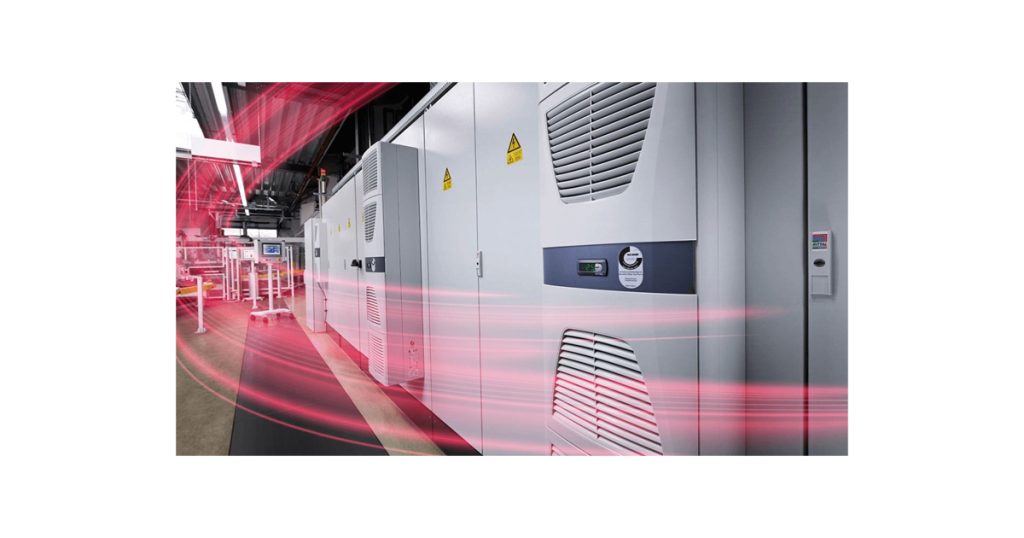
October 15, 2024
The importance of energy-efficient enclosure cooling cannot be overstated in today’s manufacturing environment, both in terms of enhancing sustainability efforts and reducing energy costs. According to a recent report, one of the biggest challenges manufacturers face is leveraging new technologies and processes to power their product programs more efficiently.
This challenge is particularly pertinent for food & beverage manufacturers given the amount of energy required to facilitate 24/7 production to keep pace with consumer demand. Plus, the diversification of the food & beverage space to include products like meat and dairy alternatives means producers are often operating multiple production lines under the same roof, increasing the amount of energy necessary to facilitate production.
Industrial enclosure cooling is one of the biggest sources of energy consumption in a food & beverage facility. This article will look at a couple of things food & beverage manufacturers need to know about energy-efficient cooling to help producers reduce energy consumption and optimize productivity.
Smart(er) climate control helps increase cooling flexibility
Flexibility in enclosure climate control in the food & beverage space is key to reduce energy consumption and costs. However, relying on more traditional cooling systems that don’t leverage Industry 4.0 and IIoT principles can be challenging, particularly when it comes to the ability to adjust outputs quickly to meet cooling demands.
Smart climate control systems can help manufacturers create a flexible, strategic cooling infrastructure that provides precise enclosure cooling at the right time and place. Plus, a digitalized cooling model makes it possible for manufacturers to control and adjust cooling outputs in real time based on the scale of production which helps maximize performance and optimize energy consumption.
Features like network notifications and app-based climate control capabilities also simplify and ensure leak-free operation 24/7, 365. If a hazardous leak is detected, smart cooling systems can be shut down instantly to help reduce waste. Rittal’s Blue e+ line of enclosure climate control units is designed using Industry 4.0 and IIoT technologies to create an efficient, seamless digital connection between cooling systems and plant operators.
Digitalized cooling unit design creates more precise cooling outputs
Digitalizing an industrial cooling unit with intuitive user interfaces, real-time performance data, and mobile monitoring has helped manufacturers deploy more targeted, efficient cooling. Additionally, the digitalization of these systems can help manufacturers leverage precise cooling outputs to create a more energy-efficient climate control system.
With a digital design platform, manufacturers can create or modify custom cooling units to precise specifications for unique or challenging deployments. What’s more, a digitalized design process helps accelerate enclosure cooling unit configuration to increase speed-to-market and help food & beverage manufactures better scale production.
For example, Rittal’s RiThem climate control design software includes a variety of exciting new digital design capabilities, including:
- Calculations and recommendations for suitable enclosure climate control systems for all environmental challenges
- The option to specify altitude (this influences cooling output), which is ideal for outdoor manufacturing conditions
- Precise calculation for bayed enclosure suites
- Recommendations for suitable and corresponding accessories for your enclosure climate control system
Digitalizing your cooling unit design process enhances visibility and transparency to paint a clearer picture of the ideal climate control solution for virtually any food & beverage application.
Prioritize simplified, streamlined maintenance processes
Maximizing uptime is key for food & beverage manufacturers, especially given the highly competitive nature of this industry. A big component of consistent, reliable production is the ability to ensure optimal operational conditions for the industrial enclosures that drive manufacturing sequences. Reducing maintenance intervals and costs plays a large role in helping manufacturers achieve this elevated productivity.
This means choosing enclosure cooling units that prioritize simplified, streamlined maintenance processes. The capacity to quickly address maintenance issues helps food & beverage manufacturers cut energy consumption and waste by reducing the likelihood of unplanned cooling unit downtime, which accelerates how fast cooling units can be brought back online after servicing.
Using heat pipe and inverter technology, Rittal’s Blue e+ S provides robust cooling without the need for a compressor, expansion valve, or other regulating elements, thus significantly reducing the amount of energy required to run the unit. In fact, the Blue e+ S can reduce overall energy consumption by 75%. Additionally, this simplified design streamlines maintenance tasks to help ensure more consistent, reliable enclosure cooling.
A streamlined design doesn’t mean reduced cooling flexibility or capacity. The Blue e+ S offers lower output categories of .3 kW, .7 kW, and 1 kW without sacrificing the adequate cooling necessary to keep enclosures at optimal operating temperatures.
