Corrosive Applications Are What These Industrial Enclosure Features Are Meant For
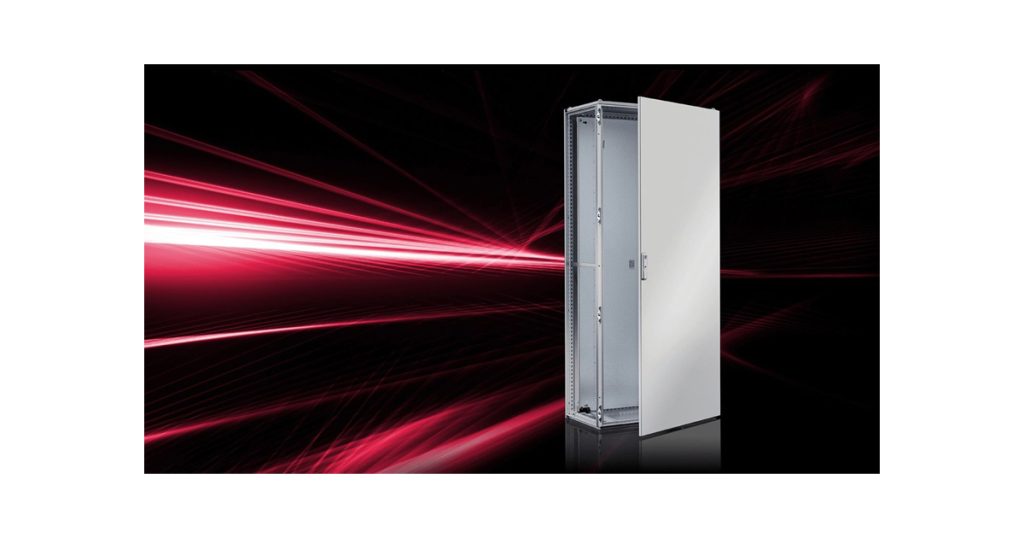
March 3, 2025
By Joel Ferasol, Energy & Power Business Development Manager, Rittal
Harsh environmental conditions – especially of the corrosive persuasion – are just part of the picture when specifying industrial enclosures for outdoor applications. Wind, moisture, and cold are fairly common weather elements designers need to account for, but combatting the potential for corrosion — from natural weather conditions or chemical agents used in production — is also key in designing a durable, reliable automation infrastructure that is built to last.
Choosing an enclosure designed for corrosive environments compared to one that is not can help manufacturers increase productivity and revenue, and it can also help reduce maintenance intervals and repair costs. Let’s look at what we mean when talking about corrosive applications, and then we’ll look at the enclosure features to look for when specifying solutions for these manufacturing applications.
Common types of corrosive manufacturing applications
Most of today’s highly corrosive manufacturing applications take the form of power generation and storage stations, oil & natural gas processing facilities (both offshore and land-based sites), chemical production facilities, and those in the maritime space, both freight and passenger vessels.
What makes these applications so corrosive is high levels of salinity from natural sources like the ocean or groundwater found in the refining and processing industry, or from chemicals found in treated water used in hydroelectric energy production. Sodium chloride can accelerate the oxidation process, and this increased oxidation weakens metal’s protective capabilities. Consistent exposure to high concentrations of high-salinity liquids can increase the likelihood of water ingress.
The ingress of corrosive materials poses a range of hazards to the panels inside the enclosure, from failure or breakdown to electrical fault, which can cause significant damage to an automation system and harm to site personnel.
This case study featuring an oil & gas processing company outlines some of the common challenges in building an automation system in a corrosive offshore environment — it also looks at the right solutions to overcome these challenges and how partnering with Rittal made these solutions possible.
Features of an enclosure designed for corrosive applications
An industrial enclosure that’s designed specifically for use in corrosive applications will utilize a steel construction as other materials like aluminum offer little protection or durability. While stainless steel is the most ideal construction material, carbon steel can be just as effective if the steel features zinc plating and is powder coated.
The stand-alone configuration of unibody enclosures makes them ideal for the elevated levels of strength and durability necessary in corrosive environments. Plus, unibody enclosures that use a single-door configuration reduce areas for potential ingress, and they provide added protection against related environmental elements like wind, rain, or airborne particles.
Aside from construction materials and configuration, there are a handful of certifications to look for that can help designers understand an enclosure’s viability in corrosive applications. One such approval is ISO 12944, which is a global standard for corrosion protection of steel structures with protective surface coatings.
Specifying enclosures designed to this standard can help optimize productivity and ROI in the face of corrosive applications by maximizing service life and reducing regular maintenance intervals.
Rittal’s new VX C4-H enclosure can meet the challenge of any corrosive application
Leveraging the strength and durability of Rittal’s VX enclosure frame, the new VX C4-H enclosure features a zinc-magnesium plated frame and a powder coated carbon steel surface to offer superior protection in environments with high salinity content. C4 environments are classified as highly corrosive, and the new VX C4-H can withstand up to 720 hours of salt spray testing, making it ideal for deployment in offshore or maritime applications.
The door, roof, and rear panel of the new VX C4-H are also powder coated for enhanced protection, and the mounting plates are zinc-plated for top-to-bottom durability.
Rittal’s new VX C4-H also provides high degrees of protection via UL Type 1 and 12 approvals, along with a IP 55 rating.
This superior performance in corrosive environments doesn’t come at the cost of flexibility and versatility. The new VX C4-H features a reversible door hinge to help manufacturers adapt to unique deployment specifications and reduce their automation footprint, both of which are critical in almost any of today’s industrial applications. What’s more, the VX C4-H can be configured quickly without the need for standardized tooling to save time and money in the assembly and installation phase.
The VX C4-H enclosure demonstrates Rittal’s commitment to providing industrial enclosure solutions that can tackle the rigors of any industrial application, particularly those in outdoor environments.
