How Digitalizing the Design of Your Industrial Enclosure Cooling Units Can Help Reduce Your Carbon Footprint
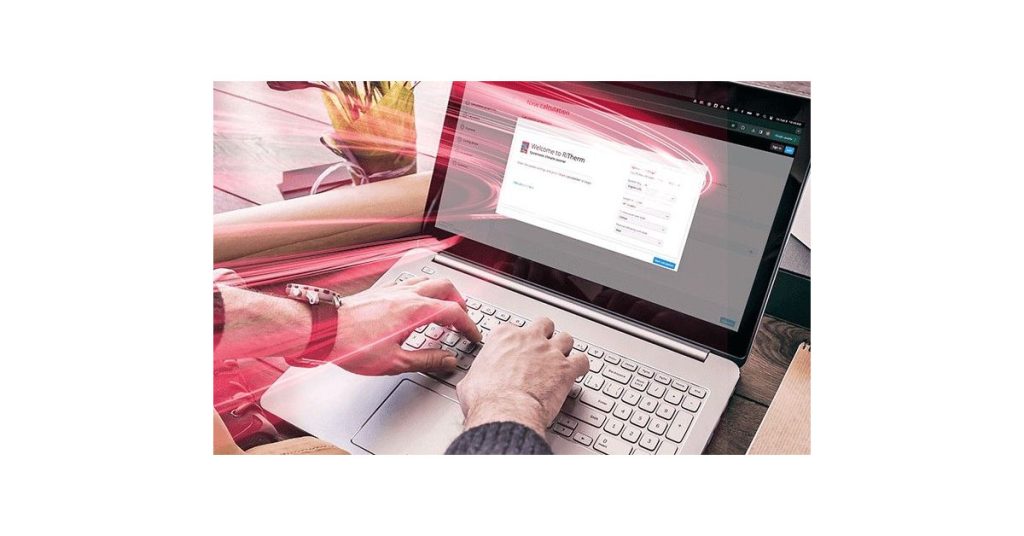
April 26, 2024
The modern manufacturing space is becoming “greener” than ever before. A recent survey of more than 200 manufacturers found that adopting new technologies in service of reducing their environmental impact is a top-tier concern in 2024 and beyond. While a more sustainable approach to manufacturing that reduces your carbon footprint certainly includes more traditional methods like reducing energy consumption, digitalizing the design and configuration of your industrial automation infrastructure can also be key in hitting sustainability benchmarks.
This is particularly true when it comes to digitalizing the design of your industrial enclosure cooling units. Not only can this help configure cooling units that offer more targeted, efficient cooling, it also creates a more connected ecosystem that increases the transparency and visibility of the design process.
Here, we’ll look at a couple of ways how digitalizing the design of your industrial enclosure cooling units can help reduce your carbon footprint, and how partnering with Rittal can help manufacturers achieve a more green approach to production.
Digitalizing the cooling unit design process can produce smarter climate systems
Smart enclosure cooling units help manufacturers create a more sustainable climate control infrastructure by producing more targeted cooling precisely where and when it’s needed. The ability to control and adjust cooling outputs in real-time based on the scale of production programs not only helps to maximize performance, but also helps optimize energy consumption.
What’s more, smart enclosure cooling units that are engineered using IIoT principles help manufacturers leverage a more flexible approach to enclosure climate control via network notifications and remote monitoring. This gives manufacturers the ability to respond to fluctuations in cooling demand on a 24/7 basis to reduce energy waste and costs.
Digitalizing your cooling unit design process can help you configure smart climate control units that offer enhanced operational flexibility via real-time monitoring, network alerts, and notifications. This helps manufacturers leverage more targeted cooling outputs precisely where and when cooling is required, a move that helps reduce overall energy consumption.
For example, our RiTherm climate control design software is housed entirely in the Eplan Cloud to increase the speed and efficiency of configuring or modifying custom, energy-efficient cooling units. This free online tool includes a variety of exciting new digital design capabilities, including:
- Calculations and recommendations for suitable enclosure climate control systems for all environmental challenges
- The option to specify altitude (this influences cooling output), which is ideal for outdoor manufacturing conditions
- Precise calculation for bayed enclosure suites
- Recommendations for suitable and corresponding accessories for your enclosure climate control system
These kinds of smart enclosure cooling units help designers meet the cooling output requirements and sustainability goals of each individual customer and provide tailored climate control solutions for a variety of industrial applications.
Digitalizing the enclosure cooling unit design can help manufacturers take a proactive approach to climate system maintenance
A big challenge for manufacturers that deploy a large number of enclosure cooling units is reducing unplanned maintenance intervals due to cooling unit breakdown or failure. Not only can such occurrences hamper the ability to provide cooling outputs that promote peak performance, sub-optimal cooling performance can increase waste and actually increase your carbon footprint.
For instance, a cooling unit efficiency analysis of Ford’s Cologne production facility revealed that out of the 220 cooling units deployed throughout the plant, 25 were defective and not operating at peak efficiency. The deficiency in the plant’s climate infrastructure was increasing energy consumption and costs, a result that could have been avoided had the plant taken a more proactive approach to cooling unit maintenance.
Digitalizing the enclosure cooling unit design process via an online tool like our RiTherm design software produces digital documentation of cooling unit specifications and optimal performance conditions based on the application. This makes it easier to establish a preventive maintenance schedule that maximizes uptime and reduces the chance of unplanned downtime.
Rittal’s RiTherm also simplifies the creation and storage of compliance documents. As part of the design process, the RiTherm tool generates certificates of heat-dissipation compliance to help save time and money in cooling unit deployment, and this also streamlines the process of ensuring that your cooling units are adhering to regulatory requirements around sustainable manufacturing practices.
Aside from creating more sustainable enclosure cooling, this more integrated approach to climate system design and engineering saves time, money, and resources by accelerating your speed-to-market and delivery windows to help you facilitate more consistent production.
Take the first step toward more sustainable, targeted enclosure climate control that helps reduce your carbon footprint.
