Century Aluminum Upgrades Mt. Holly Facility With Siemens Drives, Increasing Uptime by Over 50%
January 9, 2024
Aluminum caster improves cooling tunnel performance with upgrade of drive hardware, PLC to internet gateway and data analysis
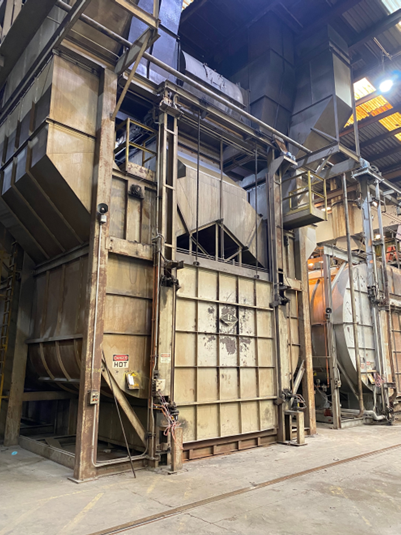
The Mt. Holly, South Carolina smelting facility of global producer Century Aluminum houses casting equipment to process nearly 230,000 metric tons of material into standard-grade ingot, HDC ingot, extrusion billet and other products. As the first primary aluminum plant in the world to achieve the ISO 9001 Quality System Standard, Mt. Holly has the highest standards for production efficiency, energy utilization and environmental control.
Recently, as Cast House Technician Sam Wilson explains, “We were faced with an increase in downtime on our two cooling tunnels due to legacy controls that were getting beyond their functional limits. The older drives would have required major rebuilding as they were able to track only speed, delivering the data to the PLC. We required more data and faster processing of it.” These tunnels are used for cooling aluminum billets after they’ve been homogenized, reducing the temperatures typically from 1,000° to 90° F. The drives on these units control the main fans to bring cool air to the loads and circulate it throughout the aluminum bundles.

Wilson contacted Miguel Ortiz, Product Manager at Electrical Equipment Company, a local distributor, who represents Siemens in the area. Ortiz and his team, Outreach Resources, did an assessment of the situation and devised a solution that met and exceeded Wilson’s expectations. The new drive and communications system involved the retrofit of a competitor’s drive with a Siemens SINAMICS G120 drive, an intelligent operator panel (IOP-2) and a unique Remote I/O (RIO) to EtherNet/IP gateway, co-designed by Siemens and SoftPLC. This device is specifically designed to enable easy migration from the legacy drives to the new drives, plus the data transmitted now includes current and torque, a significant advantage for the customer.
The results of this improvement, according to the team at Century Aluminum, included a tracked reduction in downtime of over 50%, which enables more reliable cooling of the aluminum materials, proper data analysis due to additional electrical information being transmitted and programs being saved on the IOP-2 for faster recovery. With no tools required to wire one drive to another, due to the plug-n-play feature, significant time was saved in the implementation of the new hardware. As Wilson notes with pride, “This upgrade truly brought our casting house into the modern age.”


Ortiz further details this successful upgrade. “One of the big advantages on this job is that we were able to take a demo unit into Mt. Holly and show Sam and his team how to configure the gateway without disconnecting the legacy PLC-5 controller. We could scale, readjust and map the start/stop activity, plus being able to install and test run the new equipment without changes to the PLC-5 controller program meant the system on the first retrofitted cooling tunnel were ready to roll much faster and at a lower overall cost.”
Since these cooling tunnels run 24/7/365, according to Wilson, it was critical the changeovers be as smooth as possible. In fact, Ortiz reports, both control cabinets were done in eight hours.

Using the IOP-2 and its memory for programs, Wilson and his team can use the Siemens Totally Integrated Automation (TIA) Portal to further minimize downtime, as the tunnel performance can be set to ramp-up per the known batch of product incoming.
In full operation now, the new Siemens control system is allowing a cooling scenario on a 75-ton load in half the time as previously required, which translates to 300,000 more pounds per day processed.
As a further energy saving, the motors on the tunnel conveyors now operate more efficiently in a standard vs dynamic mode.

Wilson notes another appealing feature of the new drives. “With the legacy drives, we got only the current data back to the PLC. On the IOP-2, we get to see real-time, current, RPM and the DC output. If there’s something wrong, we know it immediately and can initiate corrective action.” An additional inventory advantage was also cited by Wilson, as the 150 hp drives can be purposed for use in the carbon plant run by Century, also located in Mt. Holly, where 75 hp is the standard motor in use.
Ortiz comments on the training provided. “In addition to the demo unit we used, about 10 days prior to the install, we did an event at the customer’s facility where we gathered the technicians and some of the engineers to give them an overview of the drives, the IOP-2 and how to troubleshoot from the TIA Portal software. The training gave them both practical knowledge and a higher comfort level, as the majority of those present had lots of experience with another brand of drive products. We were able to show them how to seamlessly connect the new and the remnant legacy products.”
He also complimented the Century team for going the extra mile to take the maintenance and management classes Siemens offers.

Overall, the conversion on this application took less than 60 days. Today, as Wilson observes, “The plug-and-play technology plus the substantial program storage on the IOP-2 make our training of younger techs and operations personnel much easier. With the older equipment, line code upgrades were very time-consuming, while they’re automatic on the Siemens equipment.” Wilson muses, “The younger employees have that fast and easy modular mindset, which is great, as it matches the plug-and-play technology. Saves us a lot of time and money. I thankfully was on an old boat in the Navy and some old Los Angeles class submarines, so I know a bit more about the history of the legacy gear.”
