Automation in Food and Beverages

April 19, 2024
Traditionally, the automotive sector has been the driving force behind robotic investment and development. However, as technology has advanced, automation has become far more versatile. For a good example of that versatility in action, look at the food and beverage industry. During Q2 2023, food and beverage robotics orders totaled $21,800—and shipments in that same sector totaled $30,900. It’s clear that food and beverage companies have thoroughly embraced automation.
Consider the sheer amount of products and services that food and beverage companies provide and it’s easy to see why. This business handles everything, from development to consumption. Automation makes every part of that journey easier.
THE BIGGEST FOOD AND BEVERAGE CHALLENGES JUMPSTARTING AUTOMATION ADOPTION
A bag of sliced white bread may feel like one of the simplest things to buy at the supermarket. Yet as anyone familiar with the business can tell you, its journey to store shelves is anything but.
Consider food safety. The average can of root beer or bag of frozen fruit now involves ingredients from all around the world. Each source has its own production standards. Maintaining food safety across all those sources is a significant undertaking.
Operational efficiency and productivity, logistics in packaging and shipping and high energy costs are also big challenges. To compete in the modern market, companies proactively find areas where they can work more quickly and cost-effectively. They have to streamline their logistics in order to spend less and ship more. And as energy grows more expensive, they need to get the most out of every watt used in their facilities.
TYPES OF AUTOMATION USED IN FOOD AND BEVERAGE INDUSTRY
An industry as varied as food and beverage, unsurprisingly, uses a wide variety of automated solutions, including (but not limited to):
- Robotics
- Conveyor systems
- Automated guided vehicles and AMRs
- Vision systems
- Packaging equipment
- Process control systems
- Cleaning and sanitizing systems
What challenges can these solutions help with? Read on.
SAFETY AND SATISFACTION
Artificial intelligence has advanced considerably in the last few years. One exciting result of that growth is “deep learning,” a subset of AI that uses neural networks to “learn” to process information like we do.
That has exciting applications in food production. Machine vision systems can use deep learning to classify, segment and detect abnormalities to a degree that once seemed impossible. From flagging foreign objects in bulk raw ingredients to identifying bad apples (literally), food and beverage manufacturers can improve quality control while reducing associated costs.
Automation also means workers no longer have to perform repetitive, menial or dangerous tasks. For example, meat cutting is one of the most hazardous operations in food manufacturing. But, if automation is utilized, this risk is greatly reduced. Meat packing plants are now able to use robotic saws, which use computers to cut difficult pieces of meat while it’s still frozen. AI, while still in its early stages, can assist workers as well. Using tools like this decreases the risk of injury while production is simultaneously accelerated. Automation also allows the workforce to focus on more critical and rewarding tasks that cannot be completed any other way.
SPACE CONSTRAINTS
It’s pretty straightforward: the less space you have, the tougher it is to get the most out of it. But what if you could use vertical space for production via specialized conveyors in order to make workers more comfortable or make equipment more efficient?
New automated solutions offer more flexibility in how space is used and minimize the distance between production stages. For example, folding-arm technology allows six-axis robots to move “through” themselves, requiring less space to move back and forth. And at the end of the line, a robotic palletizer with advanced vision and motion control can pack products together as tight as possible. Every inch an operation optimizes means more money saved.
ENERGY EFFICIENCY
Whether cooking or cooling, energy costs in the food and beverage industry add up quickly. Saving money is one thing, but there’s also demand—from consumers and investors alike—for more sustainable business practices.
The pressure to get a grip on energy usage has never been higher. Experts know automation can help producers in this vein—monitoring and adjusting refrigeration functions to optimize energy use, for example, and now, robotics manufacturers are focused on developing the most energy-efficient technology possible.
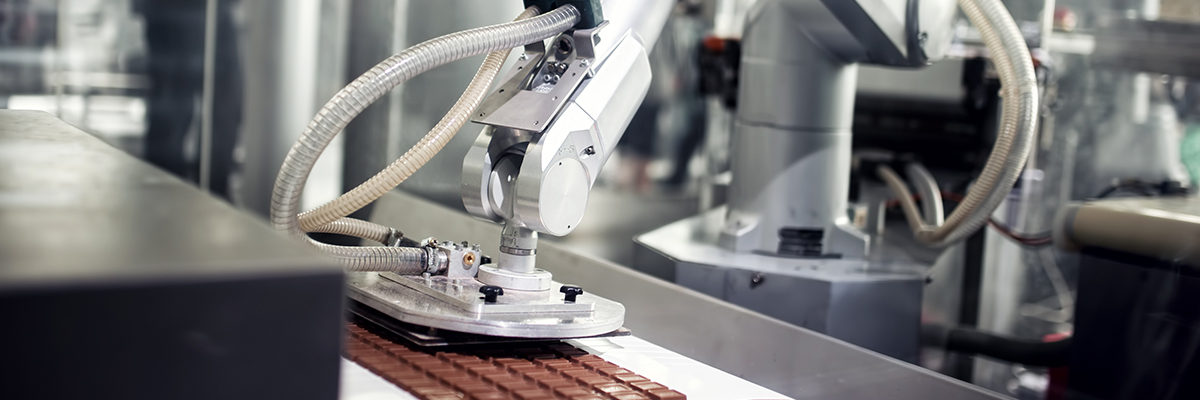
TRACEABILITY
In 2010, people began falling ill with salmonella across eleven states. The FDA determined that eggs from Iowa companies Wright County Eggs and Hillandale Farms were the source of the outbreak. The companies took back over half a billion eggs, but it was too late to prevent nearly two thousand people from getting sick.
With today’s solutions, products like eggs (or sweet potatoes) can be traced throughout complex supply chains. Machine vision and other sensors often spot flawed or spoiled eggs to begin with. And if bad eggs do get out, vision-based track and trace systems or RFID tags can monitor every step of a shipment’s journey. The moment salmonella is discovered, AI could review all available data and determine where each egg ended up. That quickens the recall and narrows its scope, saving a few hundred million eggs—and preventing many people from falling ill.
And traceability is good for more than just recalls. For example, on the back end, traceability can optimize recipe management. On the front end, it can provide proof of quality or authenticity. No wonder the traceability market is projected to grow by nearly 10% between now and 2028.
GREATER FLEXIBILITY AND SCALABILITY
The industry has faced rapid changes and serious disruptions in recent years. Customer demand for some goods drops, while surging for others. Energy costs skyrocket, then even out. The most successful food and beverage companies have to turn on a dime when the market requires it, forecast and be able to boost production of specific goods quickly.
Automation can help with all of those things. For example, smart AMRs like the ones made by Aformic Inc. can be reassigned to different jobs where they’re needed most. That makes ramping up production of specific goods easy, even for smaller operations. There are also automated inventory management systems, which order strategically to optimize stock levels at all times.
QUALITY CONTROL
When buying any product regularly, consumers want consistency. This is especially true when buying food. Flavor and texture are a big part of the experience and should be consistent each time someone consumes the same product. Automation can help with this by eliminating the chance of errors, so you get the same result every time. It also reduces the risk of product recalls.
Think about Robotic Process Automation (RPA), in which software “bots” quickly process large amounts of data. Those bots can monitor and control food production equipment. Imagine a large, mostly automated chocolate factory. Unnoticed fluctuations in temperature or humidity can quickly ruin a batch of chocolate, causing blooming or unpleasant textures. An RPA bot can not only detect environmental fluctuations, but also adjust equipment to fix the issue without humans having to step in.
FOOD PACKAGING
Whether you’re packaging craft beer cans, bagged produce for restaurants or peanuts for airlines, you need repeatability and accuracy at all times—and the efficiency to ship as much product as possible. That’s tough for humans to do all on their own. Fortunately, automation, already great for packaging, has gotten even better.
Thanks to advances in machine vision, 3D sensors and robotic gripping, it’s possible for robots to quickly package more items. Consider grocery store chicken. In the past, robots weren’t great at sorting or placing chicken parts. Humans would still need to stare down at a conveyor belt, placing breasts or drumsticks on styrofoam trays.
Now, companies like Soft Robotics make automation packages that can place and wrap that chicken faster than ever. That’s more chicken on shelves (and fewer strained wrists).
BETTER SUPPLY AND DEMAND MANAGEMENT
In this business, waste is always an issue. According to the EPA, in 2021, the food processing sector alone created 34 million metric tons of food waste. That’s terrible for the environment and for balance sheets. Companies need to accurately project their needs so they never overorder or overproduce. They also need to be able to adjust their ordering in real time to account for sudden shifts in demand.
Automated software comes in extremely handy here. Consider AI-based inventory management, which has already been seen at work in warehouses and distribution. It can analyze ordering patterns, current market trends and other factors to create demand forecasts. Companies can keep production aligned to actual demand, so fewer ingredients go to waste—and since AI can update forecasts constantly, you’ll have ample warning for when you need to ramp up or cut down.
SPEED, SPEED, SPEED
From the farm to the table, the faster things can be done, the better food is and the happier diners are—and automation is constantly offering new ways to speed things up. Consider McDonalds’ first conveyor-belt-equipped drive-thru, which allows prepaid customers to simply drive up, wait for their food to roll out on a conveyor belt and drive away.
Such convenience isn’t just reserved for ordering burgers, though. “Turnkey systems”—custom-made, ready-to-use automated solutions—are growing in popularity. A turnkey system provider can make a custom canning system for your brewery. Then, you could get a machine vision solution from a vendor like EZ Automation Systems for quality control.
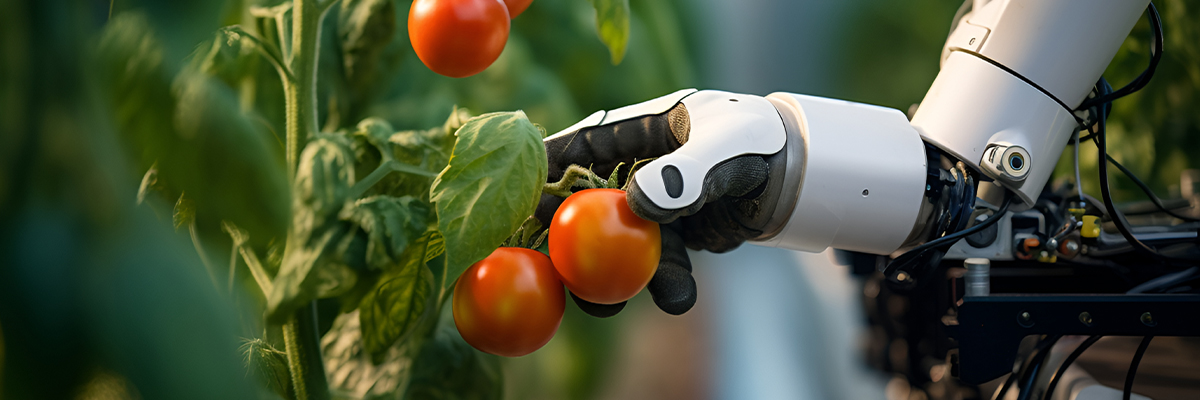
WHAT’S NEXT
Clearly, there are a lot of amazing automated solutions out there—and there are always more on the way. 3D printing, for example, is finally making a splash in food and beverage. Soon, you might see boxes full of pasta with strange geometries, or walk past a window full of customized chocolate shapes.
On the more practical side of things, there’s the blockchain, which can create a transparent, secure record of a product’s supply chain. Internet of Things (IoT)-equipped storage containers might monitor food temperatures as produce is carried across the ocean. Workers might even use augmented reality headsets that leverage vision software to improve efficiency at warehouses (unsurprising, then, that the market’s showing a nearly 57% annual growth rate).
Some of these solutions are just over the horizon; many are already here. You can learn all about it at the Automate Show. Join Automate in Chicago, IL, from May 6—9, 2024 to see new tech in action, talk with fellow professionals from across the industry and build your competitive edge.

https://www.automateshow.com/blog/how-automation-can-give-the-food-and-beverage-industry-a-boost