Cable Selection in Industrial Steel Mills
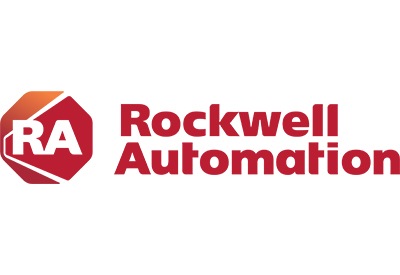
August 19, 2022
By Steven Stanford National Sales Manager, Industrial for Service Wire Company
The steel industry has faced a whirlwind of challenges—a hiatus in construction projects, worldwide pandemic, supply chain disruptions, and market fluctuations—but increased demand for domestically produced steel is creating opportunities for U.S.-based manufacturers.
The steel mills driving this growth are enhancing and developing their complex operations and processes to run more efficiently. Such developments include new electric arc furnace (EAF) technology that uses scrap as the main source of raw material and electricity as the main source of energy. This technology allows mills to produce high-strength steel without bringing in new ore or creating raw material on-site. Instead, they can recycle a product into high-strength flat-roll steel for the automotive and infrastructure industries while following a corporate-level sustainability model.
A key component to these plants running efficiently is selecting the right low voltage copper wire and cable to power the various steps in the steel-making process.
Installing Low Voltage Copper Wire and Cable in Steel Mills
Medium voltage cables connect substations and transformers. Transformers step this down into 480, 240, 208, 120, and other low voltage circuits. The low voltage copper wire and cable is run underground into the building’s switchgear where it will be stepped down even further into motor control centers and cabinets to control each process inside the facility. This includes furnaces, hot- and cold-rolling, cooling beds, cooling towers, water processing, cutting lines, trimming, and more.
Low voltage cables can be installed in a combination of conduits and cable trays to reach their final destination. In steel mills, End Users prefer to keep as much cable underground as possible to help protect the cables from heat and physical damage. Contractors could easily run 100,000-plus feet of single conductors in an underground conduit from the transformers to the individual processes. When running cable overhead and between floors, multiconductor tray cable and shielded drive cable are preferred solutions.
Considerations in Selecting Low Voltage Cable
Low voltage power cables used in steel mills must be able to handle constant exposure to high heat, water, abrasions, and environmental wear and tear. Additionally, many mills require multiple variable-frequency drives in their processes, creating another layer of complexity in selecting wire and cable.
Temperature Ratings Matter
The ambient temperatures in a steel mill alone can average 150°F. Combine that with the actual processing temperatures, and cables must be built to withstand this high, fluctuating heat. Thermoplastic insulations, used in products like THHN/THWN-2, are not built to handle this. With long-term exposure, the plasticizers can break down allowing the insulation to become brittle, affecting the integrity of the cable. On the other hand, thermoset insulations, used in products like XHHW-2, USE-2, and RHW-2, are made of crosslinked polyethylene. These compounds use a curing process that causes a chemical reaction, allowing the polymers to cross-link. Once cured, thermoset compounds retain their shape and will not remelt when heat is applied. This excellent insulating material has a higher emergency overload temperature and maximum short circuit temperature than thermoplastic products. See the chart for a direct comparison of thermoplastic products (THHN/THWN-2) versus thermoset products (XHHW-2).
Multiple VFDs in a Process
By contrast, water and other solutions are used to cool the final product throughout the various steps in the steel-making process. Mills will often have their own water treatment plants on site to move large amounts of water and purify it before reentering it into the process.
These water cooling and filtering applications can use medium voltage drives and employ multiple 250 – 350 horsepower motors driven by low voltage variable-frequency drives (VFDs). A facility could have anywhere from 15, 20, or more low voltage VFDs in one plant process alone, varying significantly by the size and type of the facility. Having multiple drives so close to one another can wreak havoc and increase the risk of harm in the overall system if the right cables and termination methods are not properly implemented.
Preferred Wire and Cable Solutions
With these considerations in mind, steel mill specifying engineers prefer low voltage thermoset XLPE conductors, UL dual rated tray cable, UL Type MC armored cable, and VFD shielded tray cable.
XLPE Thermoset Inner Conductors
XLPE thermoset conductors are made of crosslink polyethylene instead of PVC nylon. Because of the chemistries involved, modern XLPE is far less toxic than PVC if there is a fire or corona discharge and is more resistant to chemicals, ozone, and abrasions.
Thermoset products have a dielectric constant of less than 3.5, giving the cable a greater ability to resist leakage current and providing substantially higher insulation resistance. This allows the cable to handle more spikes and inrushes over longer periods of time while helping to protect critical circuits at risk of electrical interference from high leakage currents.
XHHW-2, USE-2, and RHW-2 also have a higher maximum and lower minimum temperature rating than thermoplastic alternatives, helping to protect the cable in open air installations. These thermoset cables have five times the crush resistance of PVC, proving to be a more durable cable.
XLPE single conductors can be used in conduit, cable tray, duct banks, and for direct burial installations.
UL Dual Rated Tray Cable
In many industrial applications, End Users are moving to cable tray for ease of installation and lower installed costs. XLPE tray cables are suitable for installations in cable trays, supported by messenger wire in open air, raceways, channels, conduit, and ducts.
Engineers may specify UL 1277 approved tray cable for installation in steel mills. This UL listing requires tray cables to use a recognized 1kV rated conductor and pass a higher voltage AC Hipot test on the completed cable. Each insulated conductor in a finished cable must withstand a specified voltage range for 1 minute without breakdown to be suitable for 1kV use.
These 600V/1kV rated cables offer a cost-effective alternative for applications that require a lower voltage cable but are at risk for potential voltage spikes. For example, 1kV rated tray cable can withstand greater electrical adversity, the impact of a disruptive event on the cable is smaller, and the recovery time is faster than in a less resilient system.
UL dual rated tray cable also offers flexibility in newer constructions. With new 575V and 690V motors appearing, a standard XHHW-2 tray cable can now be used because of its increased 1kV rating. Additionally, a dual rated tray cable has a smaller outside diameter than traditional 1kV tray cables, making it preferable in space-constrained installations.
Tray cable from Service Wire Company is also TC-ER rated per the National Electric Code. It is permitted to transition up to six feet without continuous support, exposed to free air. This allows the cable to transition from the cable tray to a motor, avoiding the use of flex conduit.
When required, shielded tray cable can be installed in steel mills. The shield can be applied helically or longitudinally over the cable core. Shielding acts as a faraday cage to reduce electrical noise from affecting the signals and to reduce electromagnetic radiation that may interfere with other devices. Of the two variations, helically applied shielding is more common in industrial applications.
UL Type MC
UL Type MC armored cable offers the protection and durability required for steel mill applications without the need for electrical conduit. It can be installed in cable tray, racks, hangers, or as a cost-effective replacement for conduit and wire where specified per the National Electric Code. The metal-clad armor also resists corrosion, making it suitable for areas exposed to moisture.
Type MC cables use a full UL size bare or insulated ground. Unlike Type AC, the aluminum or galvanized steel armor is not used as an equipment grounding, minimize the requirements for anti-short bushings.
Service Wire specializes in galvanized and aluminum interlocked Type MC armored cables. The interlocked armor is helically wound around the conductors for ease of bending. The cable’s s-lock design allows the cable to have increased flexibility and maneuverability in tight spaces and hard-to-reach corners, unlike conduit or even continuously corrugated welded armor.
Type MC is also available with flame retardants, moisture, and chemical-resistant jackets. This cable construction is suitable for direct burial, power circuits in industrial processing plants, and hazardous locations designated as Class I – Division 2 and Class II – Division 2.
Jacket Types
Polyvinyl chloride (PVC), Chlorinated Polyethylene (CPE), and Low Smoke Zero Halogen (LSZH) are the three most common jacket types, providing an additional layer of protection from moisture, chemicals, abrasions, and flame.
PVC is the most common jacket material, but it does not have the properties required for all rugged environments. Instead, CPE and LSZH jackets are recommended for industrial applications.
CPE jackets are designed for uses requiring higher levels of chemical resistance and washdown. LSZH jackets are flame retardant, emit lower levels of smoke and no halogens or toxic fumes, do not drip when burned (helping to prevent fire from spreading to other surfaces), and self-extinguish in an absence of direct flame.
Crosslinked chlorinated polyethylene and low smoke zero halogen jackets use thermoset polymers, unlike standard CPE or PVC jackets. While jacket selection is dependent on the environment in which cable is installed, the properties of the compound, the life of the cable, and the ratings required, thermoset jackets are better suited for industrial applications.
VFD Shielded Tray Cable
VFD cables can be used in a wide range of processes inside a steel mill from cooling to water filtration and hot-rolling. Hot-rolled steel production, for example, uses large rollers to move a product, sometimes up to 200+ rollers, with each individual roller having a 10-horsepower motor powered by a low voltage drive. With so many VFDs inside the mill, specifying engineers must find a solution that addresses electromagnetic interference, common mode stray current, and other issues commonly affecting the longevity of these drives.
The only proven solution is an electrically balanced, helically applied copper tape shielded cable with NFPA 79 compliant crosslinked polyethylene (XLPE) insulation. For the best performance, an XHHW-2 600V/1kV or RHW-2 2kV rated cable design has excellent dielectric properties to resist voltage spikes that are generated during operating conditions.
Proper Termination
While cable selection is important in reducing the effects of high frequency, proper termination and grounding of the system is highly critical. Field testing has revealed that the cable’s copper tape shield must have a 360° termination to earth ground at both the drive and motor end of the cable to accommodate a difference in ground potential. It is critical for the proper termination method to create the current’s lowest possible impedance path and to greatly reduce EMI conducted into the mill.
Termination kits for the cable’s copper tape shield may be used with terminating connectors. Recommended termination kits include two tinned flat copper braided ground straps that provide an additional low impedance ground path. These straps should be installed longitudinally along the copper tape shield, cut to the shortest length, and terminated to the inside of the motor box and the back panel in the drive cabinet.
Service Wire Company offers a comprehensive online course on variable-frequency drive cable, termination methods, and common issues that help prevent VFDs from proper performance, available for free through Service Wire Academy.
Conclusion
A steel mill is a complicated network of processes. The slightest hiccup can have a rippling effect throughout the entire production line. The right low voltage copper wire and cable is a necessary part of this overlapping system, and with proper knowledge and installation, it can help improve the stability and productivity of any industrial plant.
https://www.rockwellautomation.com/en-us/company/news/blogs/service-wire-partner.html