Harsh Environment & Design Consideration
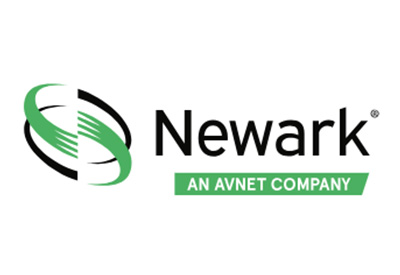
July 18, 2022
The use of sophisticated electronic and sensing devices to improve and expand manufacturing, machining, and production processes in industrial applications is only possible if all components survive the difficult environment. Systems must endure hot, humid, and harsh conditions and destructive electric and magnetic fields.
The specific environmental conditions in which a product is used affects its specifications. Such specifications must be determined at the beginning. Difficult conditions in industrial applications include particulate ingress, extreme temperature, physical impact, Electrostatic Discharge (ESD), Electromagnetic Interference (EMI), and vibration. All these conditions, if unchecked, will destroy electronic equipment over time. This article discusses critical design considerations in a harsh industrial environment.
Harsh Temperature and Semiconductor Thermal Consideration
High temperatures are a major contributor to a punishing environment. A cool climate is a necessity for effective electronic device operational performance. The microclimate inside the automobile hood is a toxic one where the ambient temperature rarely drops below 125 C. Combustion and exhaust gas sensors must work in heated, harsh environments. High-temperature electronics must make up the control circuitry administering the actuators and sensors.
When used in high-temperature environments, electronics must have active or passive cooling to keep parts within their respective operating temperature ranges. This is impractical in most real-world situations. Semiconductor (IC) robustness includes operating temperature range, fault protection, managing high electrical noise, and ESD. Robustness is a crucial performance factor for an extended operation and obtains a reputable, reliable final product. Durability is a must in an industrial ecosystem characterized by extreme operating conditions, with IC temperatures swinging anywhere between -40°C to +85°C. Elevated temperature operation is here to stay, and the automotive industry may eventually witness working temperatures between -40°C to +125°C.
Thermal issues crop up when electronic devices are kept in an air-tight industrial indoor environment. The devices dissipate heat, and rising temperatures will damage devices if improperly managed. Voltage regulators and power ICs use thermal shutdowns to prevent such a scenario. Choosing packages with super low thermal impedances help to transfer heat away from the device. The addition of aluminum heat pipes or heat sinks to the concerned case offers a lower thermal impedance path to air. This reduces operating temperature, greatly improving its longer-term reliability.
Managing Voltage Transients
Incorrect wiring or accidental shorts make voltage transients on power-supply lines. These transients can damage downstream circuitry if the inputs remain unprotected. A simple and discreet circuit consisting of a series fuse with a Transient-Voltage Suppressor (TVS) diode or Zener diode, or Metal Oxide Varistors (MOV) is generally used to protect against most voltage transients.
A more controlled approach to managing overvoltage and transient events is to integrate the reaction circuitry and protection threshold into an IC. Internal diodes and comparators are designed into multiple protection and supervisory ICs to ensure a definitive response every time. A few ICs include high-voltage fault safeguards for data lines. A fault-safeguard device latches on when normal data-line voltage levels are exceeded to shield itself from damage. A good example is the MAX4708 multiplexer family. For more information on transient voltage suppressor products, click here.
Intrinsic Safety Consideration
Intrinsic safety refers to a designed explosion protection method shielding the electrical circuit. Intrinsically safe systems restrict energy even when there are multiple failure conditions. These barriers are employed to restrict the energy discharged if a component or wiring fails. The aim is to stop ignition. A few recommendations for intrinsic safety design are described in the following content.
Batteries used must be sufficiently robust to survive anticipated environmental conditions. There should be minimal electrolyte leakage, which can happen during severe short-circuit environments.
Energy-storing parts like capacitors, inductors, and ferrite beads can be vulnerable to compliance with spark-ignition parameters. The stored available energy in them must be restricted so that there is insufficient energy to ignite an explosive atmosphere. Encapsulation is used to shield circuits against any chances of spark ignition.
Conformal Coatings
Conformal coatings are essential to enhance the long-term performance and reliability of electronic assemblies. The product offers enhanced protection against dust, shock, vibration, chemicals, dirt, abrasion, fungus, moisture, and mechanical stress. Conformal coatings include: one part UV curing formulations, one and two-part silicones, one and two-part epoxies, and a specialized, cost-effective latex system. To learn more about safety tips in harsh industrial environments, download the e-book The Ultimate Guide to Harsh Environment Ratings & Design.
Ingress Protection (IP) and NEMA Ratings
A sealed enclosure is used to prevent the ingress of water or dust. The sealed-off volume of space is used to safe-house electronics within harsh environments. The contextual standard is IEC 60529, as defined by the International Electrotechnical Commission (IEC). This standard designates the number of types and degrees of protection afforded by an enclosure to its electrical equipment. The IP code itself bears the form “IP XY,” where the digits X and Y denote protection from particle ingress and water, respectively. They are commonly used for applications exposed to the elements, along with dust or moisture. Typical user industries include marine, offshore oil and gas platforms, security, lighting, leisure, and food processing.
The National Electrical Manufacturers Association (NEMA) offers a popular protective enclosures standard similar to IP Code (IEC 60529). The NEMA 250 covers a wider sweep of harsh conditions than the IP code. It also includes ratings, both hazardous and nonhazardous, for indoor and outdoor locations. Such conditions include the ingress of foreign objects (like dust or fibers), water, and corrosive agents, including various gases and atmospheres. AE1360 is an example of IP66, NEMA 4 metal enclosure for electrical use in a harsh industrial environment. For more information on IP and NEMA rating products, click here.
Considerations for Connectors
Designers must take into account multiple factors like the influence of temperature, solvents, icing, salt exposure, moisture, corrosion, and fungus during a connectors’ selection. A wrong choice can affect the integrity, performance, and lifespan of the application. A few factors must be considered when selecting connectors for harsh environments.
Communication Protocols is a key consideration for the communication application. Connectors carry different signals like RS232 or I2C serial interfaces, RF transmissions, audio and video signals, power, or high-speed data communications. The level of data rates and characteristics should be taken into account. When it comes to power needs, the designer should check the voltage and current requirements.
Space requirements are exacting in the era of miniaturization. All modern applications continue to switch to chips and technologies that provide advanced functionalities within small form factors. Design engineers should be careful to opt for connectors as per demand.
Termination Style is another consideration. Harsh environment connectors provide metallic sealing along with an electrical connection. This electrical connection is achieved by soldering the connector directly to the board or through a cable termination. Connectors must shield components from all Electromagnetic Interference (EMI) radiations. This radiation may either pass into the box and hinder the device’s functionality or exit the box and interfere with other devices. A few specially chosen connectors fitted with a conductive gasket and plated metal shells ensure optimum EMI performance in harsh environments.
MRD series connectors are an excellent example of industrial harsh environment connectors, available in 2, 3, and 4 position form factors. Housing options include all plastic constructions as well as metal locking bodies for greater durability. Panel mount and cable termination options are available with or without finger-proof protection. They are IP67 water/dustproof and meet environmental, health and safety requirements. For more information on connector products, click here.
https://www.newark.com/harsh-environment-and-design-consideration?ICID=I-CT-TECH-RES-CLL-APR_22