How the Safety Lifecycle Can Improve Productivity
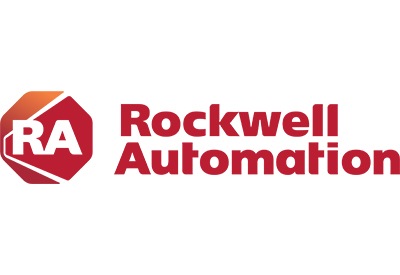
June 10, 2022
The term “safety lifecycle” refers to a formalized engineering process that helps create a safety system that can work effectively throughout its lifespan. For example, industrial and manufacturing facilities use safety lifecycles to keep their functional systems operating smoothly.
The safety lifecycle is described in international standards set by the International Electrotechnical Commission (IEC). By standardizing the safety lifecycle, the IEC provides a benchmark for industries and companies that want to meet an acceptable occupational safety level.
Incorporating the safety lifecycle into your operations can increase the effectiveness of your machines while mitigating risks and decreasing operational and engineering costs.
What is the Safety Lifecycle?
The safety lifecycle can be thought of as a series of phases. Each phase is designed to maximize productivity while also improving safety for employees by identifying what steps are necessary for assessing and mitigating risks.
Here’s an outline of a five-step safety lifecycle as defined in IEC 61508 and 62061.
1. Perform a risk assessment
This phase will identify hazards and estimate the risk associated with them. A risk assessment will determine the required Performance Level (PLr) for safety functions. The specific services involved in a risk assessment include:
- – Conformity audits
- – Guarding evaluations
- – Basic safety assessments
- – Term-based risk assessments
- – Development of a corporate safety program
2. Identifying steps to mitigate risks
Based on the risk assessment results, you can determine the functional safety system’s requirements to mitigate any identified risks. This process considers machine interactions and modes of operation. Use industry-acceptable solutions to evaluate the safeguarding options available.
3. Design and verify the system
Once a system is determined, you can choose its architecture. During this step, you will also document the safety circuit design. Finally, the design is verified to meet all requirements, including software and programming.
4. Install and validate the system
After installing the safety system, you will verify that it operates within the defined parameters and complies with standards. This step may involve bringing specialists on-site who can help perform validation testing and document the process.
5. Maintain and make improvements
A safety system must be monitored and evaluated frequently. You will need to verify that the system requirements operate within specified parameters for production, and make system upgrades and improvements as necessary.
After step 5, the cycle repeats itself as you start planning for new functional safety processes to implement.
A Real-World Look at Using the Safety Lifecycle
Here’s an example of how the safety lifecycle can be implemented at an organization.
An industrial company had, over the years, accumulated multiple aging machines. They were older models and had no safety systems in place. These machines were spread out over numerous locations, which made it challenging to systemize or standardize procedures.
So, the company called a vendor to help them improve their safety performance. The company also needed the vendor to train their staff on the new safety systems.
The vendor went through the five-step process of the safety lifecycle to create a consistent mitigation strategy and implement new safety solutions, which they validated. Then, they trained the plant staff on the safety procedures.
By the end of the project, all machines had fully operational, high-performance safety systems in place. These systems were consistent across the company’s multiple locations. Employees at each site were knowledgeable of the new procedures and were fully trained on them.
By taking the time to implement the safety lifecycle into machines that were not standardized and had no safety systems in place, the industrial company improved productivity and mitigated the risks associated with those machines. In addition, by fully training their staff, the company improved the safety of their employees because they understood how to operate and manage the machines across all locations.
https://www.rockwellautomation.com/en-us/company/news/blogs/using-safety-lifecycle.html