Control Panel News — The Good, The Bad, And The Ugly Of Post-Pandemic Lead Times
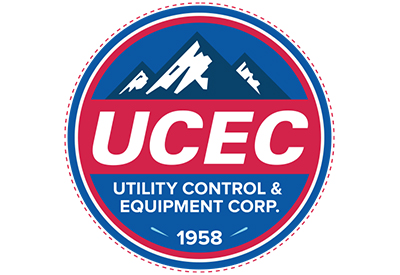
March 28, 2022
It’s finally happening — masks are disappearing and glimpses of normalcy are popping up in certain areas of society. But even as the pandemic starts to appear smaller in the collective rear-view mirror, everyone is left with a larger, lingering ripple effect in front of us all. The world of commerce continues to face effectively broken supply chains from widespread labor shortages, mounting inflation pressures on pricing, and more.
Without a doubt, the global supply chain disruption has wreaked havoc with lead times. Over the past two years, it’s been bad, then ugly. Thankfully, 2022 promises there is some good news to be had. The proverbial light at the end of the tunnel, if you will. (And this time, it’s not from an oncoming train.)
With the right approach and the right partner, you can avoid the uncertainty in lead times and make better informed decisions. But first, how did we get here?
The Bad – LABOR SHORTAGES & QUALITY ISSUES
As was mentioned before, one of the biggest contributing factors to the global supply chain breakdown was labor shortages. Even though ports were packed with record numbers of containers waiting to be unloaded, there simply wasn’t enough available labor to unload and load them.
Supply chain issues like that are compounded by the fact that factories still aren’t at full production capacity yet. The result is the ongoing dearth of certain critical tech components, like computer chips. Computer chips for thousands of cars still might not be ready until the fall. That same problem is now impacting the displays being put into panels.
A secondary impact of labor shortages is the downward spiral in the quality of available labor. When you aren’t able to establish a stable base of trustworthy talent and instead are forced to constantly hire in new people, the continuity needed for consistent quality isn’t able to form.
The Ugly – UNRELIABLE LEAD TIMES & PRICE INCREASES
Now, HVAC contractors and customers are facing much longer lead times. Again, it’s due to a combination of factors, with labor and the supply chain being the two highest profile culprits.
Lead-times have doubled in some cases, so if it is supposed to take three weeks, it is now taking six weeks.
Imagine giving a customer a quote of three weeks in a PO, only for them to find out before ordering that your quote wasn’t even in the ballpark. You not only run the risk of looking like you pulled a bait and switch, but you also risk your reputation quickly becoming sullied.
The reality of the situation is you can’t sell what you don’t have.
Even though demand has skyrocketed, supply is still constricted. It’s created a conflict that’s forced the hands of service providers. Whereas vendors were once only raising prices once a year, they are now having to do it 3-4 times a year just to stay profitable and competitive.
And this is where it’s gotten truly ugly. Because purchasing, costs, supply chain are still massive issues, vendors have basically started raising prices on select items to almost extreme levels to intentionally limit or eliminate demand. It’s an unfortunate side effect of parts becoming commodities.
For HVAC contractors, it’s part of the accepted reality of inflation.
The Good – UCEC KEEPS YOU IN THE KNOW
It’s clear the challenges with the global supply chain aren’t going away anytime soon. But with more than 60 years in business, this isn’t UCEC’s first rodeo, either. Their measured approach meets these challenges head on. UCEC will complete your panel build and allow you to have eyes wide open about available parts and possible delays. Whatever the logistics, you’ll always know ahead of time.
As for pricing, they can lock something in and guarantee it if you make a quick decision. If you come back a month later, UCEC will have to reprice things to reflect the changing market.