Why Replacing Fuses With Breakers Is Right for Industrial Applications
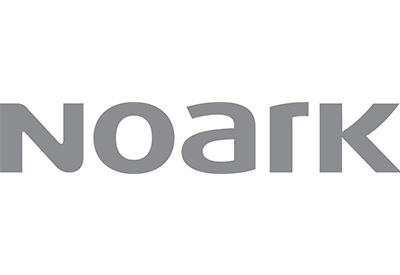
March 15, 2022
As the technology behind circuit breakers continues to improve and becomes more affordable, they’re growing in popularity to protect circuits in industrial applications and keep people safe. What’s more, fuses are less effective and safe compared to breakers. That’s why distribution panels in service with fuses are obsolete and should be replaced.
Yet fuses are still used in Industrial Control Panels, Motor Control Centers (MCC) and load disconnect applications. This white paper outlines the main factors that lead organizations to choose one form of circuit protection over another.
Choose circuit protection based on application requirements
The main selection criteria for circuit protection:
- – Size
- – Cost
- – Interrupting capacity
- – Level of protection
Some designers prefer to use 200kA fuses in all applications to make this selection easy. However, a 200kA fuse might not be required for the application.
Typically, even to get 65kA, a bolted fault is needed, which only truly happens in the UL/CSA Lab testing condition. In real application UL 508A Panels are usually situated away from the main distribution panel and connected by a length of wire. This provides enough resistance to reduce the interrupting capacity needed for a regular circuit breaker to easily handle.
By identifying the appropriate protection level needed for the application, a breaker can be selected to provide features not offered by fuses. Breakers can be competitive with fuses and disconnect combinations, especially when considering all the advantages of a breaker design.
In addition, today’s regulations require panel builders to document the interrupting capacity on their panels. This means the designers need to do an analysis of all components and their respective interrupting capacities on the panel. The device with the lowest resistance is typically the weakest link. For example, motor overloads are usually only good for 5 kA. The breaker is not the limiting factor.
Why choose breakers over fuses
Protection for single phasing
The majority (90%+) of faults in an electrical circuit are single phase. However, fuses don’t protect the circuit for single phasing. In fact, fuses often cause single phasing.
Single phasing happens when one of the phases goes to ground and only one phase fuse blows. The remaining two phases will continue to deliver power to the load. Loads such as motors might continue to work in a single-phase situation, which will lead to the motor overheating.
However, on a breaker system, all three phases will trip – regardless of the type of fault.
Maintenance
There’s a misconception that breakers require more maintenance than fuses. While it’s true that fuses don’t have mechanical components that can fail, the fuse disconnect and fuse clip are mechanical components that require the same level of maintenance as a breaker.
Disconnects have contacts that can weld and fuse clips that can become lost, which can create a hot spot. Both products should be heat scanned for hot spots.
Another consideration is the degradation of protection over time. Both products can degrade with age, but only the breaker can be tested. The only option for fuses is to replace them on an interval schedule before they blow. Otherwise, there’s the risk of a nuisance tripping situation that could lead to production loss.
Worker Safety
Replacing fuses requires the door of the panel to be open. This creates a situation where potential live voltage contact is possible. Some industrial users require personnel to wear an arc fault suit to work on live panels. Arc flash accidents are not uncommon – and they can be deadly.
To make the situation worse, some fuse clips and fuses are completely accessible from the front. Special covers need to be added to prevent a live power hazard. After service, the maintenance team needs to be attentive and assure the cover is properly re-installed.
What’s more, replacing a power fuse requires a trained electrician, which can delay production until one can arrive on site. Some fuse blocks require a fuse puller or a special tool for servicing, which aren’t usually provided or readily available. This can lead to a potentially dangerous situation if someone attempts to remove a fuse with an incorrect tool like a metal screwdriver.
Another issue is the level of global support available. When replacing a fuse, the replacement parts commonly found in North America might not be as accessible in Europe. Many OEMs prefer to standardize products to ensure components have global support.
With breakers, it’s easier to select components that will be universally available and supported in different markets.
Overall costs
The overall cost of a breaker is lower than a fuse, when fuses’ life-cycle costs are factored into the equation. Between the time lost to replace fuses when short-circuits happen, fuse replacement costs, and the extended time required to diagnose problems, the overall costs of fuses add up quickly.
It’s also important to consider the risks that maintenance employees are exposed to when replacing fuses.
In some situations, breakers are the same price as fuses, plus the fuse holder and disconnect switch required to make a complete system. With all these factors considered, fuses are an expensive proposition.
The right applications for breakers and fuses
Fuses can be useful in circuits that need a high interrupting capacity or for sensitive electronic equipment that requires extra fast-acting protection. However, for most UL508 control panels and MCCs, breakers are a better solution. The benefits outweigh the initial investment, especially when downtime is particularly expensive.
There are increasingly more DC circuits in today’s modern panels, with the growing acceptance of alternative energy and the EV market. There’s also a trend toward changing 120vac controls circuit to 24 VDC for safety reasons, in case of accidental contact with live voltage. Breaker technology has improved and is now capable of handling DC circuits.
The only application where breakers can’t efficiently replace fuses is to protect a primary control transformer above 460v. Miniature DIN rail breakers ratings stop at 480Y/277 volts and molded case circuit breakers (MCCB) are too big and expensive to be used in this application.
Circuit breakers: The future of functionality
As machines deliver more feedback and information than ever before, industrial applications need circuit protection that can go the extra mile. Breaker technology is ready for these advanced applications – for today and tomorrow.
An auxiliary contact will indicate if a breaker is on, off or tripped. Breakers can also be remotely operated using a motor operator, simply by switching it off and then on again. This also allows the breaker to work with an operator interface diagnostic page. Now operators will immediately know the location of a problem, which can save precious production time.
Another benefit is the ability to remotely trip the breaker in the event of a safety issue. For example, a circuit can be turned off when another part of the machine is not live to prevent a dangerous situation.
These benefits make the breaker a perfect partner for all industrial applications.