Special-Purpose Machines With Standardized Automation
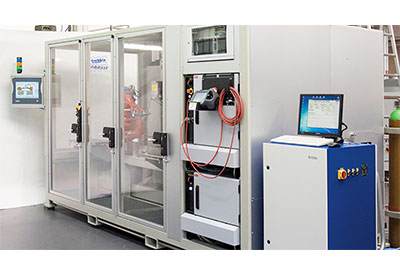
February 14, 2022
Almost all of the systems built by special-purpose machine manufacturer Trebbin are custom-made individual units, because flexibility and inventiveness are essential when providing automation solutions for a huge variety of different industries. This company, located in Eichstätt, Bavaria, builds whatever the customer requests. Trebbin favors WAGO’s automation and interconnection technology more and more often as the standard for their machines. The many advantages WAGO’s technology offers benefit not only the Eichstätt company, but also its customers.
Not all Machine Manufacturers Are the Same
Take a small tour of the Trebbin manufacturing facilities in Eichstätt, Bavaria, and it is quickly apparent that the machines and associated control cabinets the employees are working on meticulously are one-of-a-kind. The two-story factory hall seems more like a traditional workshop than a production facility. Nothing is mass-produced here; instead, they build prototypes and special-purpose machines. In addition to machine engineering and automation expertise, understanding the application the machine will ultimately serve is crucial. A glass display case in the middle of the hall showcases examples to date: lamps, cables, ampules, glass filters, plastic cases and much more. Every item has been handled and produced to the customer’s exact specifications with Trebbin machines. Systems from Trebbin assemble, weld, grind, bend and label – all fully automated, of course. The Eichstätt machine manufacturer has also constructed gas mixing systems and burners, as well as robotic palletizers and stackers – and all with only 50 workers.
An Inventive Spirit Is Needed for Each Machine
“Lot size 1” is the normal situation at Trebbin, as Patrick Schmidbauer, Director of Control Technology, confirms. For him, an order from a lamp manufacturer for six machines of the same type almost felt like a large series. In actuality, an inventive spirit is needed for each machine. Only rarely is one of these highly specialized machines and systems duplicated, according to Schmidbauer. “We are working on one such exception right now,” reports Schmidbauer. “Robu Glasfilter-Geräte GmbH has recently decided to order a second system like the one we designed and built in 2013.” The system is based on two robots and a laser system. With the precision of a master glassblower, they fuse a section of borosilicate glass to a sintered glass filter disk to form a filter crucible. In the last step, the crucible, which is required in chemical and medical laboratories, is labeled. Even though the filter fineness, wall thickness and diameter can vary, the same high quality is maintained throughout. This glass filter production system was long unique. Not only is this inventiveness a source of pride to Trebbin; it is also a unique selling point for its customer, Robu Glasfilter-Geräte. This uniqueness plays a role in nearly every machine conceived in the Eichstätt facility.
Each System a One-Off
Machines for automotive suppliers, lamp producers and medical technology manufacturers top the list of Trebbin one-offs. Hardly any two machines are the same; even their outer dimensions vary widely. “We bundle the technology required to control the system together in the space available to us,” says Schmidbauer, describing the approach. If the customer’s machine hall only has available space in one narrow corner, Trebbin can even fit a system that would normally require three-by-three meters on a one-by-nine meter footprint. “We can handle just about any request,” says Schmidbauer “or install any robot the or control system customer wants.”
WAGO as Partner for Machine Manufacturing
Yet Schmidbauer does have his favorites: Whenever possible, he uses WAGO products for the automation of Trebbin systems. The main reason is that WAGO offers a scalable and extremely modular range of automation products. As versatile as Trebbin solutions are, this lets Trebbin solve any automation requirement of a system. Another advantages point is the expandability of the WAGO system: A module with an additional function can be plugged in at any time. “Our customers benefit immensely from this flexibility.” Many of Trebbin’s customers look for a control concept that integrates safety; thus, they often demand special functions and PROFIsafe modules. Others continue to rely on the old standard, for example, with separate safety controls. “Incorporating safety features directly into the controllers offers many advantages, and not only where space is a factor,” says Schmidbauer. Everything can be connected via the fieldbus, including the fail-safe inputs and outputs – which is an advantage in itself. In particular, the automotive suppliers among Trebbin’s customers are preferring to implement safety functions in the controller more and more.
Saving Space Is Becoming More and More Important
Space requirements are gaining more and more importance in automation technology, says Schmidbauer: “This is where WAGO really has the advantage, because their components are exceptionally compact. With other manufacturers, everything is just a little larger. On many of our systems, the control cabinets are jam-packed.” And Schmidbauer thinks highly of WAGO’s interconnection technology: “The spring pressure connection technology in WAGO’s terminal blocks is absolutely unparalleled. It has many advantages for us and our customers.” Not only are the terminal blocks quick and easy to install during control cabinet construction; during system operation, they are also vibration-proof and maintenance-free. Schmidbauer recalls: “Our people used to have to inspect and retighten each and every terminal block after delivery. On a large control cabinet, that would easily take an hour.”
WAGO’s EPSITRON Power Supplies for Economical Operation
In addition to the I/O System 750, Trebbin also uses WAGO’s electronic fuses. “We can also save significant space in the control cabinets with these fuses,” emphasizes the automation expert. WAGO’s 2-, 4- or 8-channel EPSITRON ECBs provide reliable protection against short circuits; since they are also communication-capable, they can be monitored remotely. Trebbin also installs WAGO’s 24 V power supply units whenever possible. With their low acquisition costs, quick assembly and extremely low space requirements, WAGO’s EPSITRON family of power supplies is ideal for economical operation of a system throughout its entire service life. Thanks to their wide input range, they can be operated in the different power grids in Europe, America and Asia. The Eichstätt special-purpose machine manufacturer chose them as an integral part of their standardization strategy because the demands for a flexible and economical power supply for basic applications is rising steadily. However, another factor in their decision was that some of its customers have stipulated WAGO’s power supply units in their specification. “WAGO is already very well established; nonetheless, every now and then, customer want components from other manufacturers. The terminal blocks are the only area where we use almost nothing else,” reports Schmidbauer, adding: “Unless the specifications sheet states otherwise, we use WAGO components, because with them, the automation of our systems always functions smoothly and safely. We are completely satisfied.”
Solutions for Energy Management – and Soon for Industry 4.0 Too
Trebbin also benefits from the innovations for mechanical engineering that WAGO is constantly bringing to the market, due to its numerous customers in the factory automation sector, such as for energy management. More and more buyers of energy-intensive equipment demand efficient solutions from Trebbin. As Schmidbauer sees it, WAGO definitely has the opportunity to establish itself as the standard here. WAGO’s 3-phase power measurement modules, for example, work very well in combination with the fieldbus technology Trebbin uses – from DeviceNet, to PROFIBUS, to PROFINET. WAGO’s current signal conditioners and Rogowski coils can convert the energy data to standards signals. With WAGO’s energy measurement modules and the comprehensive accessories, Trebbin can find a simple energy measurement solution for each of its customers. “This is definitely becoming a major topic. There’s a good chance we’ll retrofit many of our machines that are already in use now with such solutions. Because our customers want to know where there is still potential to cut costs.” And besides these specific challenges, “we assume the issue of Industry 4.0 will catch up with us sooner or later,” says Schmidbauer, looking to the future, “and when it does, we’re sure that WAGO will have something substantial to offer us.”