National Apprenticeship Week: Two Future Engineers Describe Their School-And-Work Lives
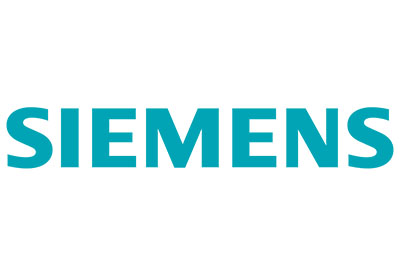
January 3, 2022
By Siemens
Siemens’ success depends on skilled workers around the world—not just within our own company, but among our suppliers and customers, too. We want to help fill the 870,000 open positions in America’s manufacturing sector. We want to connect veterans with jobs that are a perfect match for their skills. We’re listening to voices on the factory floor that are seeking opportunities to reskill or upskill and move to higher roles.
We’re also thinking about those future engineers, factory managers, and technicians who are still in high school. The question we’re asking is, “How can we introduce more high school students to apprenticeships before, not after, they graduate?” We want to make sure students are aware of apprenticeship programs that enable them to earn while they learn and forge a path to a high-quality career in industry, setting the stage to go as far as they can dream both in their education and their career.
The Siemens Foundation is a supporter of the Partnership to Advance Youth Apprenticeships, a multiyear, collaborative initiative that’s helping get high-quality youth apprenticeship programs off the ground and raise more awareness about their value. Additionally, Siemens recently joined the U.S. Department of Labor’s new program, the Apprenticeship Ambassador Initiative, which seeks to create a national network of employers, labor organizations, industry associations, program sponsors, educators, workforce intermediaries, apprentices, community-based organizations, and other stakeholders to serve as champions for expanding and diversifying Registered Apprenticeship Programs (RAPs).
Siemens intends to support the initiative’s goals of expanding pre-apprenticeships, degree apprenticeships, and youth apprenticeships like we launched with Wake Technical Community College (WTCC) at our eMobility manufacturing hub in Wendell, North Carolina. Starting in the 11th grade of high school, this 4-year program focuses on integrated basic training that develops technical, methodological, and social skills, as is part of the North Carolina Triangle Apprenticeship Program (NCTAP).
So, as we celebrate this National Apprenticeship Week, we wanted you to hear from two of our apprentices in Wendell, NC: Madelyn Clark and Ethan Hatch, both seniors at Apex High School and East Wake High School.
Both Madelyn, who says she has wanted to be a mechanical engineer “since I was little,” and Ethan, who says he “fell in love with mechanical engineering” through college-level courses offered in his high school, have accumulated hundreds of working hours on various production lines in the Wendell factory, a facility that manufactures a variety of equipment including SICHARGE UC charging solutions for buses, trucks and heavy-duty electric vehicles. Their apprenticeships put them in hands-on roles on Day 1, and now their schedules are a heady mix of school, work, sports, and music.
How did you find out about a possible apprenticeship, and what are you doing at the Wendell facility?
Ethan: My high school guidance counselor was contacting kids who were in engineering classes to find eligible candidates who had the grades to qualify for it. I was one of them. At Wendell, I’m working on the production line low-voltage motor-control centers (MCC). I’m helping assemble what are called “buckets,” units of 10- to 600-amperes circuit breakers that are inserted into larger structures. I’m experiencing this entire production line from beginning to end. My days are pretty busy—I’m up at 5 a.m. and at the factory by 6, and then go to school at 10. After class I go to basketball practice.
Madelyn: I found out through my high school’s newsletter that there was an apprenticeship orientation program coming up on a Zoom call, and I decided to join it. I work in the part of the factory where we are currently building EV bus chargers. I have helped build the electric-bus cabinets where all the components go to power the EV charging dispensers. I start my day going to school—I’m in class until 10 a.m., and then go work in the factory until 3:30, and then go home and usually have to practice for a musical performance.
Did you recognize the value of an apprenticeship right away, and do you know where you want to go with it?
Madelyn: I was a bit hesitant about it after the first few company tours that I went on, because they didn’t seem like the right fit for me. But as soon as I came to Siemens and I saw what they’re doing at Wendell and who I would work with, my hesitancy was gone. Now, my plan is to finish my associates degree at Wake Tech and work in mechanical engineering after that. I want to get my four-year degree at NC State. And after that, I am hoping to become a field engineer for Siemens so I can travel around to see the different customers that we work with, and maybe get to travel the world, which would be amazing.
Ethan: At first, I too was kind of hesitant about an apprenticeship, but then I realized this opportunity is once in a lifetime. So, my plan is to continue with this program for the remaining three-and-a-half years to work my way up to engineer—I really want my Associate’s Degree in mechanical engineering. That’s also with free schooling in this program. Beyond that, I plan to transfer my credit to either NC State or East Carolina University, and to continue through with mechanical engineering. I do want to find out what I like better—mechanical or electrical engineering—because Siemens does work with both of those.
Once you arrived at the Wendell plant, what were your impressions of that facility?
Madelyn: What has really wowed me was the teamwork at Wendell. I had a job before and it was everybody for themselves—nobody helped me. But as soon as I came to Siemens, I saw everybody was helping each other out and they were helping me out. Everybody that I worked with has taught me how to do the different electrical subassemblies and how to follow the production processes. They went through it step by step to make sure that I got it and were really patient.
Ethan: People put an image on manufacturing facilities like they’re dirty places, not clean, but [Wendell] is very clean, very safe. It’s a great work environment.
You both are part of the workforce of the future, so what excites you about the future?
Ethan: I’m excited about a lot of things going electrical and digital. Siemens right now is working on mass producing bus chargers for electric buses in Raleigh, NC. That eliminates a lot of emissions. I’m big on electric cars, too. When you go from gas to electric, you’re not hurting the environment like you were before, and saving a lot of money as well.
Madelyn: Same for me—I’m really excited about seeing everything going electrical and being way more healthy for the planet. I want to get an electric car at some point. It’s going to be really amazing to see how electrification will grow. I also want a future where everybody my age actually has a job, and they can support their families when they’re older while also creating a great planet while they do it. I want to see people actually be able to have a sustainable future and I would like to see more women in this industry and I have been working through the apprentice program to get more women interested in becoming an apprentice.