How to Choose The Right Safety Network For Your Production Line
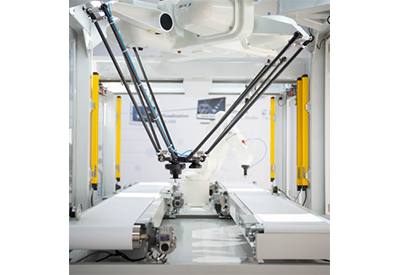
November 22, 2021
Safety networks have been around for a while. Devices are getting more connected, leading to a greater need to collect and share data. In tandem with this, safety networks are acquiring a more significant role in enabling flexible manufacturing and supporting Industrial Internet of Things (IIoT) initiatives.
On the factory floor, where assembly lines need to change in accordance with consumer demand, adding or removing a part to the process can be a challenge. When it’s time to mute a robot or add a new welding station for a particular model, operators are starting to consider machine safety as a key component in facilitating truly flexible manufacturing.
Safety networks support flexible manufacturing
Safety networks, such as CIP Safety over Ethernet IP and Safety over EtherCAT (FSoE), offer a proven way to support flexible manufacturing by reducing wiring while ensuring rapid configurations and safety integrity. By using the black channel approach, a single channel can transfer both standard and safety-critical data.
Let’s take a look at the benefits of both CIP Safety and Safety over EtherCAT, since Omron is currently the only automation solution provider that offers a controller supporting both networks simultaneously under a single environment.
CIP Safety reduces wiring, helps integrate third-party devices, and improves data collection
Excessive wiring adds a tremendous amount of complexity to any machine, and the typical standalone safety solution drastically increases the number of wires required. This in turn makes the system quite difficult to troubleshoot when anything goes wrong. It also increases the time required to validate any changes to the system.
Although both CIP Safety and FSoE help reduce wiring, CIP Safety supports the creation of an integrated safety network that makes wiring reduction easier than ever by letting you mix standard and safety-rated devices within the same network or wire. With CIP Safety, you can integrate third-party devices and collect safety-related data for use in improving the system.
Consider the scenario of integrating an additional robot into the safety system. Without CIP Safety, this could mean hooking up close to 80 wires. With CIP Safety, it’s just a single cable.
Safety over EtherCAT supports shorter reaction times and large network extension
For automated applications requiring high levels of speed and precision, such as packaging machines, printing machines and machine tooling where multiple servos are controlled simultaneously, the EtherCAT protocol reduces the number of different fieldbuses and interfaces by offering safe and standard communication in a single channel.
With Safety over EtherCAT, a safety application can make full use of EtherCAT advantages. These advantages include shorter reaction times, support for high numbers of nodes, large network extensions, cable redundancy options, and greater flexibility with Fast Hot Connect.
https://automation.omron.com/en/us/blog/safety-networks