Fiix: 10 Benefits of a CMMS
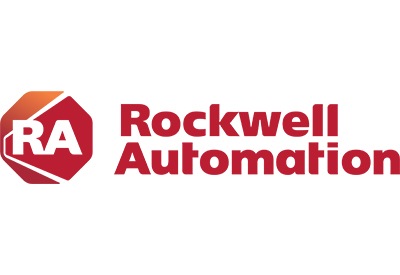
November 15, 2021
Fiix’s computerized maintenance management system (CMMS) helps maintenance and operations teams schedule, organize and track equipment maintenance digitally, connect to business systems and make data-driven decisions while leveraging the power of AI. There are over 3000 maintenance teams in 90+ countries using Fiix to improve efficiency, asset health and even sustainability.
Here are 10 benefits of a CMMS:
- 1. Reduce downtime
- 2. Control costs
- 3. Increase efficiency
- 4. Collect and use data
- 5. Improve health and safety
- 6. Save energy
- 7. Automate work requests
- 8. Standardize maintenance processes
- 9. Make preventive maintenance easier to schedule and complete
- 10. Increase asset lifespans
1. Reduce downtime
Conquering a maintenance backlog is challenging and can lead to unwanted downtime. Some maintenance backlog is unavoidable, but too much can send your operation into a tailspin.
A CMMS balances resources and maintenance costs so backlog doesn’t get out of hand. The software catches small fixes that would otherwise go unnoticed and enables maintenance tasks to be scheduled, assigned and prioritized.
2. Control costs
CMMS software excels at enabling maintenance teams in planning, scheduling and executing preventive maintenance (PM). Not only can you automate tasks with a CMMS, but you can also prioritize and assign PM while tracking key metrics to optimize them. The best way to reduce costs is to avoid unplanned failure by keeping assets running smoothly with preventive maintenance.
Managing your inventory with a CMMS lets you purchase, track and organize parts so you can avoid these costly problems. Tools, like automated purchasing, inventory reporting and AI-powered parts forecasting, can help you make data-driven inventory decisions and eliminate over- and understocking.
Avoiding manufacturing scrap and rework also helps control costs. Both scrap and rework require a huge cost in the form of energy, waste and lost production. The worst part is, it’s difficult to recoup that expense without the production team working overtime.
A CMMS lets you accurately forecast the parts you’ll need for maintenance. Not having an organized inventory system can lead to all sorts of costly problems. Overspending on inventory can add an additional 12% to 20% to the original purchase cost. And, downtime occurs if you don’t have the right parts on-hand when equipment breaks down or you can’t find the parts in a messy storeroom. The results of downtime, including rush shipping and risky stopgap measures, can be expensive.
3. Increase efficiency
Inefficiencies can add up and cost your facility a lot of time and money in lost production. Downtime occurs whenever an asset must be repaired or inspected and it isn’t always avoidable. However, wasteful repairs and PM prolong downtime. These inefficiencies can add up and cost your facility time and money in lost production. For example, when technician schedules are not optimized, preventative work is performed when not needed, or repairs are not coordinated with production.
A CMMS makes it easier to repair and inspect assets. The result is reduced downtime and maximized productivity. Technicians log into a mobile CMMS app from any location. Next, they view an asset’s history, diagrams, location of spare parts and more, so work can be performed faster. CMMS software also helps you find work orders that take too long, spot the cause of the delay and fix it, increasing efficiency.
4. Collect and use data
Finding trends in maintenance metrics allows maintenance teams to collect and use data. Maintenance metrics translate action into numbers so you can measure the performance of technicians, assets and workflows in your operation. These metrics allow you to connect cause and effect so you can make better decisions and improve your operation.
But you can’t track metrics without the right tools, processes and people. CMMS software is the right tool in this equation. It captures the numbers and tracks metrics over time so you can get a long-term view of your performance. CMMS software also makes it easier to analyze the data and fine-tune strategies based on historical metrics.
5. Improve health and safety
Training is a key element of environmental safety and has been shown to reduce injuries by 24. It also leads to fewer breakdowns and unforeseen costs. Although safety training is crucial, everything from bad timing to the need for specialized skills can hinder your team’s best-laid plans.
CMMS software can help remove the obstacles in the way of proper safety training. A CMMS allows you to store and track health and safety information for technicians, like certifications. You can also pull safety reports from the CMMS so you can decide what kind of training to prioritize.
6. Save energy
American manufacturers spend $230 billion on energy every year, which shows that any company can cut costs by reducing energy use. Well-maintained assets are more energy-efficient and are key to lowering overall energy expenses.
Reactive maintenance is a major source of wasted energy at production facilities because it leads to inventory issues, poor scheduling, rework and more. A CMMS can solve these issues by helping establish a better preventive maintenance program with tools like automated work orders and easier work scheduling.
7. Automate work requests
It’s common for maintenance managers to receive work requests via phone, sticky notes, whiteboard or word of mouth. None of these methods are ideal. These outdated processes force maintenance teams to spend unnecessary time creating work orders and inputting data.
CMMS software eliminates the extra steps by automating the work request process. Employees can log work requests, design PM triggers or connect to sensors that create work orders based on the real-time condition of an asset. No time is wasted translating work orders, tracking down operators or rifling through a file cabinet.
8. Standardize maintenance processes
One way to make maintenance more efficient is to use a tool you know works well in a certain situation. Starting from scratch with every PM, repair or report will take longer and lead to extra downtime and costs.
A CMMS gives you the power to build maintenance checklists, workflows, reporting templates and more to make tasks easier and quicker. The maintenance software also makes these resources available digitally. With a CMMS, everyone can access the same information, follow the same procedures and get the job done as quickly as possible.
In fact, companies using a CMMS experience 44% more productive facilities and maintenance teams.
9. Make preventive maintenance easier to schedule and complete
Preventive maintenance catches anomalies before they become a bigger problem, which reduces the number of breakdowns. Maintenance teams know that preventive maintenance is key to limiting downtime, but the question is, how do you schedule more of it?
A CMMS answers this question with automated work orders. PM triggers can be created based on usage, time or condition in a CMMS. These triggers activate a work order, which is then scheduled and assigned. The work order becomes much smoother and preventive maintenance is easier to schedule, leading to less downtime.
Well-planned maintenance schedules waste less time, resources and money. Better planning is possible when you can anticipate every element of maintenance, like asset needs, production schedules and inventory.
Building a better maintenance schedule starts with understanding your assets and resources. Tools like sensors, programmable logic controllers (PLCs) or manufacturing execution systems (MES) help you capture, track, and analyze data about an asset’s performance. Integrating these tools with CMMS software allows you to use this data to fine-tune the frequency of preventive maintenance tasks and deliver maintenance schedules use staff resources as effectively as possible.
10. Increase asset lifespans
The average age of industrial equipment in the US is the highest since the 1940s. Although age isn’t always the reason for failure, it’s often a contributing factor. Maintenance is crucial because it’s not always financially possible to replace old models with new ones.
Keeping equipment in good operating condition for longer means doing maintenance before something breaks. You can’t do that using original equipment manufacturer (OEM) guidelines or guesswork. Integrating CMMS software with sensors, PLCs, supervisory control and data acquisition (SCADA) and MES systems allow you to track an asset’s health in real-time, catch failure before it happens, diagnose problems and schedule maintenance.
CMMS software increases efficiency, opportunity
Every person in a facility has a goal, from completing maintenance to tracking metrics or reducing costs. Regardless of what you’re trying to achieve, CMMS software makes it easier to accomplish. The real value of maintenance software lies not in its features, but in the way these tools are used to eliminate inefficiencies. A CMMS allows you to identify areas of opportunity and maximize the talent at your facility. Fiix makes increased efficiency possible, and more.
https://www.rockwellautomation.com/en-us/company/news/blogs/10-benefits-cmms.html