Three Connectivity Tips from Moxa for Switchgear and UPS Power Quality Monitoring
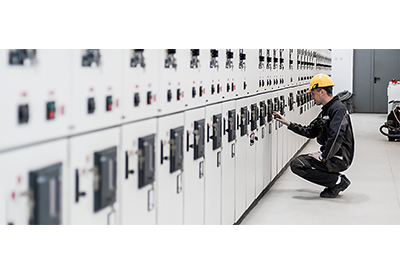
October 18, 2021
As more electrical devices are deployed in industrial applications, the need to protect these critical systems increases. Unexpected power outages lead not only to higher maintenance costs of electrical equipment but also to lower operational efficiency, productivity, and overall business revenue. To ensure a stable power supply, facility managers need to monitor power quality so that electrical devices are protected from unwanted interruptions and damaging fluctuations.
Switchgears and uninterrupted power supplies (UPSs) are two essential pieces of equipment to consider when developing a comprehensive power quality monitoring plan. In general, switchgears are the first stop when utility power flows into factories and data centers. These devices transform voltage, monitor power current, and protect industrial equipment from abnormal fluctuations in electricity. As a result, the facility manager needs to constantly monitor the status of circuit breakers, surge protectors, current transformers, and power quality meters used inside switchgears. In addition, UPSs are valuable for providing nonstop power supply when the main power source fails and the backup power supply, such as a generator, is not immediately available.
To monitor the real-time status of an application’s power quality, switchgears and UPSs need to connect with an energy management system (EMS) so that operators can make instant decisions to minimize system downtime. Establishing a reliable communication system in between allows the operator to monitor power quality and respond to emergencies in time.
Moxa offers these three tips to consider when developing communication systems for power quality monitoring applications.
First, the communication system needs to withstand high EMI. As for electrical equipment, communication systems for power quality monitoring also need to be protected to ensure operators can receive the real-time status of power quality. Communication devices are usually located near power systems that generate high EMI, which can easily interrupt network communications.
To minimize EMI interruptions, use fiber cables that provide strong EMI immunity over long distances and are an ideal option for transmitting data from the power equipment to the control center. In addition, connectivity devices should feature additional protection mechanisms, such as dual-power and dual-port inputs, ensuring nonstop operation if one of the power sources or ports fails.
Second, the communication system requires rapid recovery to reduce downtime. Connected devices for power quality monitoring are usually serial-based and use industrial protocols, such as Modbus RTU. On the other hand, EMSs usually use Ethernet-based OT/IT protocols, such as Modbus TCP, SNMPv3, and BACnet/IP. It usually takes a protocol gateway to enable communication between these devices and systems. When communication errors occur, operators cannot receive the status of power quality in time, making it difficult to spot abnormalities for incident responses. Furthermore, it is challenging for engineers to perform root cause analysis when they lack sufficient information and need to overcome the increased complexity of troubleshooting across different protocols. When choosing a protocol gateway for a communication system, check if it comes with troubleshooting tools that can help quickly identify the root cause of an incident and get the system back online quickly.
Third, plan wisely for the communication network and get power data online easily and securely. A variety of sensors related to power stability are available. When developing a power quality monitoring application, there is a need to collect not only power-related data but also environmental data to ensure a stable power supply without environmental interruptions. Both power and environmental sensors come in a variety of interfaces, so choose connectivity solutions that are easy to install and maintain in a space-limited cabinet.
The network plan should also include connectivity security. When switchgears and UPSs are connected over public networks, they may expose systems to potential threats. Thus, networking devices need to be protected so that vulnerabilities cannot be exploited by hackers.