Energy Data Management for Wood-Fired Systems
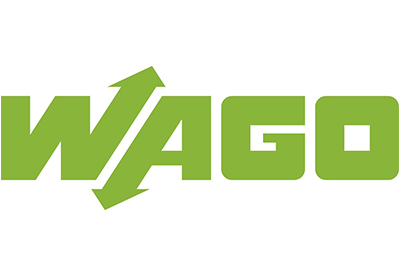
October 12, 2021
The energy transition has brought both challenges and also new opportunities. For example, if a wood-fired system also provides process heat, then lucrative subsidy programs can be utilized. The energy data management system which is, among other things, necessary for to apply for subsidies, can be easily realized, as Endress Holzfeuerungsanlagen GmbH has proven.
Garden centers and wood-processing companies, like carpenters, furniture factories or lumber mills, are often presented with the question of how to usefully use their waste wood. Directly generating heat from it can be an efficient and environmentally friendly practice. Endress Holzfeuerungsanlagen in Burgbernheim in Middle Franconia offers suitable technologies for this. Their 25 employees plan and manufacture complete combustion systems that have outputs from 100 to 1000 kilowatts (kW).
“Our wood-fired systems offer an optimal solution anywhere that fuel is produced as a by-product of production,” states Jürgen Ströbel, Control Cabinet Construction Manager at Endress. The companies actually see a doubled profit, “Carpenters, for example, have to pay to dispose of their wood chips. With our wood-fired systems, they save these costs, and simultaneously generate the heat they need in their operations.” Emissions are also far below legally specified limit values. This is achieved using intelligent temperature monitoring, lambda-controlled combustion controllers and newly developed particulate filters in the Endress combustion systems.
Utilizing Numerous Subsidies
Also of interest for operators: they can apply for various subsidies to pay for the installation of the wood-fired system. Grants from the Federal Office of Economics and Export Control (BAFA) can cover up to 35 percent of eligible costs for systems that satisfy technical rule DIN EN 303-5 for solid fuel boilers. If the new system replaces an old oil heating system, then the grant can come out to as much as ten percent higher. “There is also another subsidy if the heat is used both to heat the building and also for process heat,” explains Ströbel. Operators can receive up to 55 percent of the total costs in grants.
This option is offered, for example, to lumber mills and carpenters, where energy-intensive drying systems are operated. However, other operations, in which process heat accounts for more than half of the total heating energy, can also profit from the additional grants. An important prerequisite for this, however, is that an energy management system is installed at the company and is certified according to the ISO 50001 standard.
Easily Recording Energy and Operational Data
Since documenting the entire energy flow is one of the prerequisites for certification, Endress offers an option for energy data management along with its wood-fired systems. “We rely on Energy Data Management from WAGO for this, since we have had many positive experiences with this vendor in the control technology of our systems,” says Ströbel. It consists of Web-based application software combined with a modular control system. The software is completely programmed and merely has to be parameterized during commissioning. For the hardware, Endress uses a PFC200 controller, also from WAGO. The system can record various energy and operational data, store and visualize the data via an integrated web server. “No programming experience is required for commissioning. We only have to parameterize the meter addresses using the integrated web interface, and it’s done.” Ströbel is quite enchanted with the simple solution.
At Endress, the heat flow meters installed in the system are connected to the controllers via the M-Bus. “This allows the system to record the total output from the boiler, and also the individually used heat flows, for example, in a drying chamber, completely automatically.” The energy data management is not limited to just the heat meters, but is an expandable system that can also record the consumption of other different types of energy. For example, an additional electric meter for measuring electrical energy consumption can be connected using the M-Bus provided in heating systems from Endress. The system stores all data in a local SQLite database and can also copy data to a local SD card.
Standard Compliant Documentation
One of the major benefits of the WAGO Energy Data Management is, in Ströbel’s opinion, that the system requires little operator input, “The system runs reliably around the clock. The operator only has to read out and externally store the data for documentation.” Because the documentation complies with standards, there is nothing standing in the way of a positive certification according to ISO 50001. “And if the company can use this to prove that half of the generated heat energy is used for process operations, then the company can obtain the higher grant, up to 55 percent of the total costs,” emphasizes Ströbel.
This solution has other benefits beyond the ease of operation on site. Remote access is also possible via the web-based interface. “For example, if a customer would like to retroactively integrate another meter, we can easily parameterize this through remote access,” explains Ströbel. Heating systems from Endress, which are equipped with energy data management systems, generally function as isolated solutions, in which data are locally stored on an SD card. For larger enterprises, in which energy data management according to ISO 50001 is more comprehensive, the system can integrate very different bus topologies and record all other energy flows in the company. A connection to the WAGO Cloud is also possible. This offers numerous functionalities related to energy management. For example, consumption of different types of energy, like heat, electrical energy or compressed air, can be documented separately. Energy generated by an in-house photovoltaic system can also be recorded.
Trust in Positive Experiences
Ultimately, Endress had two essential reasons for choosing the WAGO system, “That we could manage things completely without any programming was naturally a positive point in their favor,” says Ströbel. “We have also had many years of positive experiences with the WAGO I/O System 750 in the control and automation technology in our systems.” A 750-890 controller is installed in all Endress heating systems, which is programmed using CODESYS V2.3. It reliably controls all of the functions, from the worm drive for the fuel, through the control of optimal combustion by means of a lambda probe, up to cinder discharge and cleaning of the exhaust air filter.
Suitable input and output cards are available in the WAGO I/O System 750 for all sensors, actuators and components of the heating systems. “If needed, our customers can link the heating system directly into a building control system via Modbus TCP, without needing an additional card,“ explains Ströbel. Endress delivers between 50 and 80 new wood-fired systems to customers each year. WAGO Energy Management is included more often than not.
Parameter Setting – Not Programming
WAGO Energy Data Management – consisting of a software solution combined with a modular control system – records measurement data from different media and variables for energy monitoring and processes them for further analyses, archiving and reporting. The software automatically detects different signals from the connected meters and sensors, making them available to further energy analysis tools via simple parameter settings.
Another benefit: WAGO Energy Data Management is eligible for funding from the “Federal Funding for Efficient Buildings” subsidy of the Federal Office of Economics and Export Control (BAFA).