How to Be Sure You’re Getting a Truly Modular Enclosure
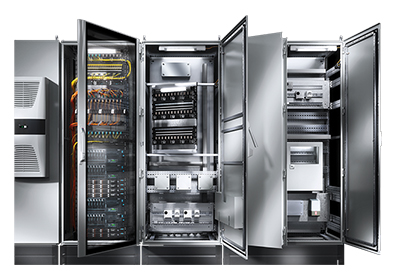
October 12, 2021
Even in 2021, in a time when Industry 4.0 and IIoT have accelerated the evolution of industrial panel and switchgear engineering, there’s still much in the way of misinformation and misconception about how manufacturers should go about defining a modular enclosure and what truly categorizes an industrial enclosure as modular.
Whether it’s a matter of naming convention or just a misunderstanding of the traits and attributes that comprise a modular enclosure system, today’s panel builders, machine builders, and systems integrators need a firm grasp of what constitutes a modular enclosure to fully realize how a modular system can help them respond to market demands, supply chain logistics, and variant-rich production streams with more agility, flexibility, reliability, and speed.
With this in mind, let’s examine what is meant (and not meant) by modular enclosures, the characteristics of a modular enclosure, and how Rittal’s innovative, forward-thinking approach to modular manufacturing can streamline your workflows and make you more competitive in a crowded environment.
What is (or isn’t) a modular enclosure
First, let’s look at a couple of other terms often associated with modular enclosures that complicate an accurate definition. A modular enclosure should not be confused with a unibody enclosure, which is constructed out of several heavy gauge pieces of sheet steel requiring lots of welding to make the enclosure [SS1] . While unibody enclosures are durable and offer high degrees of protection, their rigid design hampers maintenance, repair or modification of the enclosure and the equipment within.
Speaking of modification, the abbreviation mod or mod enclosure, which usually means modified enclosure, is another industry term that is easy to mix up with modular enclosure. While a modified enclosure can certainly have some modular traits or attributes, a modified enclosure is simply an enclosure with custom holes, tapping, milling, or other customizations, and does not necessarily mean it possesses the traits of a true modular design.
A true modular enclosure is: an industrial enclosure where the parts or panels can be reconfigured or rearranged within its standard design offering unique or customized solutions, and also can easily incorporate the use of “turn-key solutions” which can reduce or eliminate costly machining and fabrication.
Characteristics of a modular enclosure
With a definition firmly established, we can now discuss the core elements or components that comprise a true modular enclosure, the characteristics to look for when evaluating whether an industrial enclosure is actually modular, and how these hallmarks provide critical value to today’s manufacturers. The prime characteristics of modular enclosures include:
- – Protection of enclosed electronics: Yes, just like unibody enclosures, perhaps the most mission-critical component of modular enclosures is their ability to protect the sensitive electronics enclosed within. However, modular enclosures provide additional strength and durability through an innovative, steel frame design, which helps combat a larger variety of potential hazards. Any facility manager or systems integrator can easily name the wide range of environmental challenges in each production facility: water, airborne contaminants, unauthorized entry into the closure, and many more. The option for stainless or carbon steel, polycarbonate, or fiberglass constructions provides NEMA and IP ratings on par with unibody enclosures with the capacity for additional protection from UV damage, corrosion, and more.
- – Climate control: The ability to adequately, affordably, and accurately direct targeted cooling to maintain optimal operating temperatures for peak efficiency and longer service life is crucial for a productive industrial automation framework, and modular enclosures are engineered for the seamless integration of digital climate control systems. The capacity for compartmentalization, or the ability to house disparate pieces of equipment each of which may require different climate control needs, allows facilities managers to more precisely direct cooling outputs to where and when cooling is needed most.
- – Ease of modification: This article mentions the M word above, but the capability for modification to exacting specifications is another element of modularly engineered enclosures. In today’s manufacturing landscape, custom solutions are needed for specific environments to help companies overcome unique challenges. The array of construction materials, digital engineering process, and end-to-end visibility in assembly provide a 360° view of the enclosure to better plan for the modifications necessary for any application. In addition, the ease of modification allows manufacturers to scale up or down based on the parameters of the production sequence, customer demand, space, and other factors.
How Rittal’s modular enclosures fit the bill
Everyone is searching for the proverbial magic wand in today’s industrial landscape, that one solution that will solve all their challenges in one shot. Rittal’s line of modular enclosures may very well be the nearest thing to a magic wand for their ability to help companies prevent the ingress of damaging particles, precisely direct essential cooling outputs, and provide the rugged durability necessary for indoor and outdoor applications.
Rittal’s modular enclosures offer manufacturers other important value propositions such as:
- – Enhanced efficiency through rapid, digital configuration; streamlined design and planning; and simplified installation processes. In addition, Rittal’s modular enclosures allow for varied and unique cable configurations inside the enclosure while also allowing for flexible cable entry. This means no matter your wiring configuration or application, Rittal’s modular enclosures can be adapted to meet your needs.
- – An emphasis on flexibility via construction from component parts that can be rearranged without any need to cut or weld even if the dimensions of existing equipment don’t precisely align. This helps conserve space on the production facility floor — which is particularly important in the material handling space — and allows for modularity-engineered climate control systems or accessories to be easily integrated without reducing valuable square footage. For example, the TS 8 modular enclosure, its unique framing system, and its baying capabilities allows for the integration of multiple enclosures in a single unit to house electronics for large applications.
- – Modification is a breeze due to 3D design and engineering, compartmentalized assembly, multiple options for construction materials, and Rittal’s Rapid Modification Center which is not only designed to execute precise cuts, holes, and other modifications through the 5X Modification and primeXPRESS programs, but also through an 85,000 square-foot warehouse and distribution center with a robust inventory of components parts and expedited shipping to reduce delivery times.
{videobox}wH1QBB9xmWg{/videobox}
With cutting-edge design, engineering, support, and modification services, you can rest easy knowing a Rittal enclosure is the epitome of the modular category.