When To Use Multi-Function Safety Relays
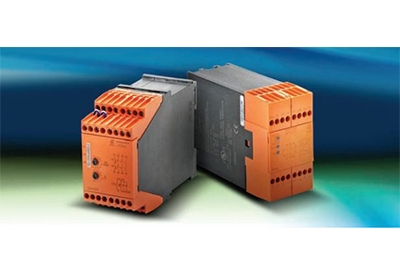
July 13, 2021
By Lenny Filipkowski, Product Manager, Industrial Components, AutomationDirect
Many machines and robots require safety circuits to stop all or part of operation in the event of an emergency. Safety circuits are also used to keep all or part of a machine or robot from running while there is human activity in close proximity, either for normal operations or maintenance.
These safety circuits are typically configured using safety relays, or a safety-rated PLC or other safety-rated controller. But in many cases, multi-function safety relays are a better option (Figure 1). A multi-function safety relay is a configurable device with multiple inputs and outputs. It’s more powerful than a single-function safety relay, and less complex and expensive than a safety-rated PLC.
One or more multi-function safety relays can often be used to replace many basic single-function safety relays, simplifying installations and saving money. In other cases, multi-function safety relays can be used instead of a safety-rated PLC, resulting in substantial savings while streamlining implementation and maintenance.
Relays limit options
Machine and robot builder OEMs, and end users with similar applications, often have to monitor and control many I/O points that include a relatively small number of I/O points performing safety-related functions.
The most common safety circuit for simple machines with up to three safety inputs (such as an E-stop and two gate switches) is a basic single-function safety relay that has redundant contacts and is self-monitoring. As a machine or robot’s safety system requires more safety inputs, an option is to keep adding basic single-function safety relays, or to possibly go to a much more expensive safety-rated PLC.
Adding basic single-function safety relays to monitor and control the safety I/O often results in overly complex installations involving a relatively large number of relays. If zone control is desired, which requires certain parts of the machine or robot to continue operation for particular types of events, then the number of required safety relays can rapidly multiply, and complexity can grow exponentially.
When many relays are used, troubleshooting can be very difficult as each connection point and component need to be examined to determine the point of failure. Modifications are very difficult to implement as they require rewiring and often the addition of more relays.
In installations with four or more safety I/O points, one or two multi-function relays can often be used to replace four or more basic single-function safety relays, simplifying installations and saving money.
The benefits of this approach are listed in Table 1 and described below. Because fewer relays are required, less panel space is needed along with much less wiring. This cuts panel footprint and saves on upfront labor costs.
If changes are required to accommodate modifications to the machine or robot, or to add features, it’s much easier to reconfigure a multi-function safety relay, as opposed to adding more basic single-function safety relays.
Multi-function safety relays are available in a number of styles, including, but not limited to, dual channel monitoring with or without time delay, two-hand control, light curtain monitoring, speed monitoring, motor standstill monitoring, and relay extension to increase the number of output contacts.
These relays come in a wide offering of input and output configurations. A simple base unit can handle a variety of inputs, and expandable input and output modules can be added as needed. Multi-function relays do not need software for configuration or operation, so setup and maintenance is typically very straightforward and simple.
One specific type of multi-function safety relay allows desired functions to be set via a rotational switch at the front of the relay. It is designed to handle a variety of inputs such as E-stops, gate switches, light curtains and/or two-hand buttons—with appropriate outputs to trigger alerts and specific machine or robot operations.
Another type of multi-function relay provides more power through a combination of rotary and DIP switches that are used for initial configuration. This relay type typically can accommodate a much higher number of I/O, up to 24 inputs and 24 outputs, by utilizing separate input and output modules.
A system with an E-stop and two safety light curtains would require three single-function safety relays. Figure 2 shows the same system with a safety circuit consisting of just one multi-function relay, greatly simplifying the circuit while cutting costs and adding flexibility.
Simpler than a PLC
For zone control and other complex safety circuits, another solution is to use a safety-rated PLC to control and monitor just the safety I/O, or even all of the I/O, but this can be very expensive and can add unnecessary complexity.
Adding a separate safety-rated PLC in addition to the main controller requires the OEM to purchase, program and maintain a second programmable system in addition to the main controller. This safety-rated PLC will need its own programming software, with consequent renewal fees. The learning curve for a safety-rated PLC can be steep, and costs are relatively high.
Alternatively, one safety-rated PLC can be used to perform all required control and safety functions. This eliminates the problem of two separate systems, but it increases costs significantly, and generally only makes sense when a very large percentage of the machine or robot I/O is directly related to safety.
One or more multi-function relays can often be used to perform all safety-related functions for a machine or robot, resulting in substantial savings while simplifying implementation and maintenance as compared to a safety-rated PLC. The benefits of this solution are listed in Table 2 and described in detail below.
It’s typically much easier to configure a multi-function safety relay than it is to program a safety-rated PLC. There’s no need to purchase, update and maintain programming software, and a programming PC isn’t required.
A multi-function safety relay is easily integrated into the main control system by simply hard-wiring a few I/O points between the relay and the controller.
Because a multi-function safety relay is much less expensive than a safety-rated PLC, it often can be used to cost-effectively handle all of the safety-related I/O, obviating the need to upgrade the main controller to one that’s safety-rated.
Caveats and considerations
Very simple applications are often best served by one or two single-function safety relays and don’t require the added expense of multi-function relays. A machine, robot or other system that may only have an E-stop along with a set of light curtains or door switches is an example of an application where a single-function safety relay would be the best choice.
Multi-function relays do have their limitations and can only be expanded to a certain practical limit in terms of the total number of I/O points and complexity of function. Cost and particularly complexity can increase to a point where it makes sense to use a safety-rated PLC.
Very complex applications with many safety I/O points and multiple zone control, or applications with requirements that change substantially from machine to machine or over time, may be better served by using a safety-rated PLC, either for just the safety I/O or for all of the I/O.
Multi-function relays result in savings
A manufacturer of limit switches upgraded to a multi-function safety relay system for its production cell to accommodate increased automation of the processes used in the construction of its products (Figure 3).
The original safety circuit design was mostly manual, and thus required substantial operator interaction. The circuit had an E-stop, one set of safety light curtains, and door switches.
The newer automated production system required the addition of light curtain, door switches and safety mats at different locations within the production process. Different interlocking requirements such as speed monitoring of some of the equipment were also needed.
By automating the production process, the manufacturer was able to relocate eight employees to different functions in the company, and to increase production by 40%.
By switching to a multi-function safety relay instead of adding more single-function safety relays, the company saved 30% of the initial cost, and gained a much more flexible safety system.
The manufacturer did look at adding a safety-rated PLC, but the cost would have been more than 60% higher than the multi-function relay system, and the complexity of having to support such a system was not justifiable.
Conclusion
Machines and robots with just a couple of basic safety inputs such as an E-stop and one or two door switches or other safety-related inputs are typically best served by a safety system with one or two single-function safety relays.
When a machine has many I/O points, with a high proportion safety-related, a safety-rated PLC is often the best fit.
But for a machine or robot in between these two extremes, an easy to configure and inexpensive safety system using multi-function relays may be the preferred choice.