As Code Changes Take Effect, Can Your Facility’s Electrical Safety Program Keep Up?
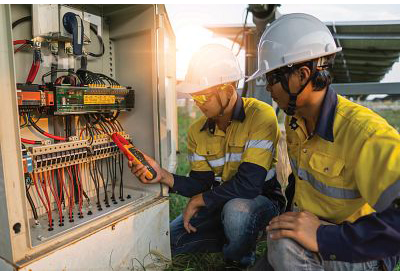
May 25, 2021
After two decades of workplace electrical fatalities trending downwards, the numbers have begun to rise alarmingly in recent years. According to the Electrical Safety Foundation International (ESFI), 2019 saw the most electrical fatalities on the job since 2011.
Many more workers may be in harm’s way. Research shows that for every fatality, a typical industrial facility experiences 300 recordable injuries and 300,000 at-risk behaviors that go undocumented.
Tellingly, two of the top 10 OSHA violations in 2019 concerned electrical safety – namely, lockout/tagout and eye and face protection.
While PPE is one of the most visible protections for workers, it represents a last line of defense. The National Institute for Occupational Safety and Health (NIOSH) encourages facilities to follow a hierarchy of controls in order to not only better protect employees but reduce or prevent dangers when possible. Plants should remove, replace or isolate hazards, and then address worker behavior.
As infrastructure ages and technologies and codes change, however, many plants struggle to keep their safety program up to date.
The 2020 NEC Adds Four New Rules for Industrial Equipment
The NFPA sets industry standards for electrical safety through three symbiotic documents: the NEC (NFPA 70) guides the installation of equipment, while NFPA 70B directs maintenance and NFPA 70E dictates safe work practices.
Over the last few revision cycles, these codes have evolved to accommodate advances in technology and a better understanding of shock and arc flash hazards. Industrial customers should note four changes to the latest version of the NEC:
- 1. Regulating reconditioned equipment: This update addresses reconditioned equipment for the first time, providing a working definition of “reconditioned” and requiring that original listing marks be removed to clearly identify restored equipment. Learn more.
- 2. Performance testing arc flash equipment: OCPDs 1,200 amps or higher must be performance tested when they are installed. Learn more.
- 3. Labelling available fault current: Available fault current must now be marked on panelboards, switchboards and switchgear – including temporary power equipment. Learn more.
- 4. Increased service entrance protection: The “six disconnect rule” has been changed to ban service panel boards that have six or fewer disconnects without a main. Instead, the code outlines four ways to use up to six disconnects instead of a single overcurrent protective device (OCPD). Each disconnect must be labelled with a distinct clearing time. Line-side barrier rules have also been extended beyond switchboards and panelboards to cover additional service equipment. Learn more.
NFPA 70E-2018 Revises the Assessment of Risk
No matter what safeguards equipment provides, people can make mistakes. How can a supervisor quantify the potential threat presented by energized work?
Previously, NFPA 70E set out five “hazard-risk categories” that specified the levels of PPE and fire-resistant clothing required to withstand potential arc flash exposure. In 2018, NFPA revised the standard to differentiate electrical hazards and risks.
A hazard is defined as the heat energy at a given point in an electrical system – a calculated value that is either present or not, depending on whether equipment is energized. Risk, meanwhile, considers how likely a task is to cause injury, and how severe that injury would be. Hazard is a property of the system; risk is specific to the task performed.
For example, consider operating a circuit breaker disconnect with the enclosure door closed, versus troubleshooting with the enclosure door open. Both situations present the same hazard, because the heat energy of the equipment remains the same – but the latter carries a higher risk, since it exposes a worker to energized components.
Before servicing energized equipment, NFPA 70E-2018 now mandates a risk assessment that considers the potential impact of human error.
Graybar Can Help You Build a Safer Workplace From the Bottom Up
As recent code revisions make clear, electrical safety should be approached holistically. NIOSH visualizes the hierarchy of controls as a pyramid, where each layer builds on the ones below. PPE acts as a capstone, which, to be most effective, should be supported by a safety training program and foundational equipment safeguards.
In a fast-moving industrial environment, however, it can be difficult to take a step back and consider safety proactively instead of responding to individual incidents.
Graybar can help you optimize your infrastructure and training program by leveraging our relationships with leading manufacturers to deliver custom solutions for your facility. By taking a product-agnostic approach, we can cost-effectively improve on existing equipment and develop a tailored safety policy and training program.
At industrial facilities, safety is everyone’s job, but often an employer’s or owner’s responsibility. The latest round of code changes presents an opportunity to take another look at your plant floor and make sure worker protections are keeping pace with advances in technology. While code compliance helps prevent hefty fines and – more importantly – harm to employees, risk management shouldn’t be reduced to a checklist. Electrical safety is an ongoing journey, and Graybar can help you draw the roadmap to guide continual improvement in your facility.