5 Mechanical & Electrical Problems A Maintenance System Can “See” That You Can’t (But Need To)
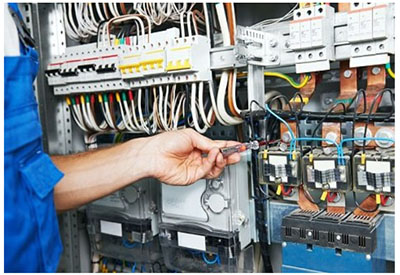
May 11, 2021
Building systems, such as HVAC, consist of thousands of components that work together to keep occupants comfortable and safe. Preventative maintenance helps ensure all these pieces stay in good condition, through inspecting and checking for worn parts.
However, inspections can’t find every issue. Even with a detailed maintenance program in place, you may not uncover some problems until it’s too late. The solution? Using a building maintenance system to reveal hidden issues.
Here are five problems that a maintenance system can “see” that you can’t.
1. Dampers Not Opening/Closing All The Way
When dampers fail to open or close completely, it affects their operation but doesn’t necessarily cause a system malfunction. Unless you’re specifically checking dampers, you won’t find this problem without the help of a building automation maintenance system.
A maintenance system tracks conditions over time to look back at past readings—if they begin deviating from expected values it indicates a potential issue. For example, if normal operations require dampers to be 30% open and they’ve been trending closer to 50% to reach the same conditions, you know something’s off. Problematic dampers left unfixed will increase energy costs and eventually cause equipment damage.
2. Sensor Drift
Sensor accuracy shifts as time goes by, and readings become less and less reliable. Simply looking at a sensor won’t reveal that it needs recalibration because sensor drift happens slowly over time.
An astute technician or facility manager with an eye for unusual output can spot sensor drift using data from a building automation system (BAS). On a heat exchanger, for instance, the temperature going in is typically higher than coming out. If the output sensor is drifting, it may show a lower reading than the input—which doesn’t make sense. Recalibrating drifted sensors keeps equipment running to the proper setpoints and provides accurate feedback so a BAS can keep a building comfortable.
3. Blown VAV Box Fuse
A VAV (variable air volume) box can blow a fuse in a multi-stage electric reheating system without drawing any attention. That’s because even with a blown fuse in the VAV box’s second or third stage, heating continues, making this issue difficult to detect.
A blown VAV box fuse won’t appear in BAS readings, but the result of the blown fuse will. You’ll know something’s amiss when heating takes longer than usual. If raising the heat typically takes 30 minutes, and the system now runs for an hour and a half without reaching its setpoint, there’s a problem. Unaddressed, a blown VAV box fuse will overwork other components, ultimately shortening equipment lifespan.
4. Detached Electrical Contacts
Electrical connections coming detached from contactors can lead to lights not coming on when they’re supposed to—or staying on when they’re supposed to be off. For something like parking lot lights, you’ll notice when they don’t come on at night, but not necessarily when they’re on during the day.
A BAS that displays energy use will be able to point a technician to potential electrical problems. Lighting systems with increased energy use during times that aren’t typical may indicate an electrical issue, such as detached or incorrect electrical contacts. If left uncorrected, improper electrical connections can cause safety issues, unnecessary energy waste, and increased operating costs.
5. Equipment Nearing Failure
Machinery begins to break down as it nears the end of its useful life and will draw more energy than usual to compensate for weakened or worn parts. An older fan, for example, may need more power to achieve normal operation if its bearings are locking up.
An increased power draw indicates a problem, and an experienced building automation technician can view maintenance readings and detect equipment running on the edge of its amp capacity. Preventative maintenance combined with expert BAS analysis can reveal components in need of repair (or replacement), so they can be fixed before equipment fails.
BAS Maintenance Is Critical To Facility Management
Many organizations put time, effort, and resources into maintaining their HVAC equipment but neglect to maintain their building controls. As a key resource for detecting issues and zeroing on maintenance needs, it’s important to include your building automation system as part of a comprehensive facility maintenance plan.
https://info.midatlanticcontrols.com/blog/5-problems-maintenance-system-can-see