Omron’s Perspective On the Factory of the Future
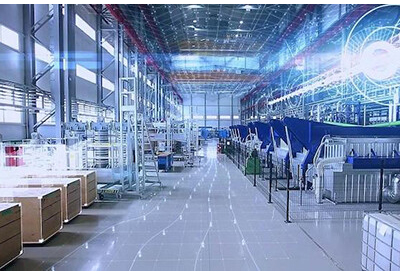
March 15, 2021
There are plenty of burning questions in the manufacturing industry. “How do we increase flexibility?” “How can we ensure consistent quality and accuracy throughout?” “What’s the best way to minimize the impact of recalls?” And the the big one: “What will the factory of the future look like?”
In this globalized era, we need to take on a global perspective when discussing any aspect of manufacturing. For this reason, Omron see remote-work technologies and augmented reality as key innovations that will accelerate this trend towards worldwide operations. Let’s take a look at how these and other nascent technologies will impact the next-generation factory.
Decision-making won’t be marred by distance
The next five to ten years are likely to see a major shift towards remote decision-making thanks to rapid improvements in the collection and transfer of real-time data from machines and works-in-progress. Operations managers on one side of the globe will be able to check data on processes happening on another and troubleshoot machines with relative ease.
This decision-making will be aided by augmented reality in the form of digital manuals that pop up when an operator views a certain part of a machine through special glasses. In the future factory, it’ll also be possible to work with components in a completely different location, further breaking down barriers between distant parts of the world.
Sparking creativity with lights-out manufacturing
Being able to troubleshoot machinery without being physically present enables what’s known as “lights-out manufacturing.” Robots in a lights-out facility work around the clock, maintaining production throughout the night and during other historically unproductive times. Running this type of facility significantly boosts productivity without the costs of extra staffed shifts.
When human workers aren’t burdened with mindless, repetitive tasks anymore, they’ll instead be able to instead focus on more creative tasks, like writing the programs that help robots switch between tasks or coming up with new ways to improve the efficiency of the overall operations.
We’ll see the machines get even smarter
In the next several years, machines will start to “understand” more about themselves and the production processes and will start being able to troubleshoot themselves. With more data at their disposal to “know” when servicing is required, these machines will free up designers to think more about the entire assembly process rather than the nitty-gritty aspects.
New 3D visualization technology will provide a detailed scaffolding upon which new and improved processes can be tested virtually without requiring anything to be built. Manufacturers can see how a new line will fit in a facility, determine what it’s really going to cost, and build it in lighting speed.
https://automation.omron.com/en/us/blog/future-factory-omron