How Print Quality Inspection Helps You Comply With Labeling Requirements
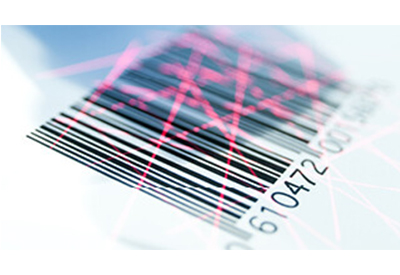
February 16, 2021
Manufacturers can face hefty fines and serious reputational damage when erroneous labels escape into the supply chain. To combat this, it’s essential to install a system that will catch misprints, reveal printer maintenance problems, and prevent debris and foreign matter from obstructing the label. This all starts with print quality inspection.
Some companies take care of this requirement manually. However, manual inspection is quite slow, very prone to mistakes, and often significantly more expensive. GS1 standards for barcodes get updated every year, meaning that inspectors must be retrained on the new requirements.
The advantage of automated inspection
Automated inspection systems are much less error-prone than manual ones, and they’re also more thorough and more easily repeatable across multiple locations. Verification systems offered by Omron inspect not just barcode info, but also human-readable text and logos through advanced LVS and AutoVISION software.
Our in-line verification solutions catch defective labels right away to maintain quality standards throughout production. The inspection software covers a wide variety of needs, including blemish detection and the verification of 1D/2D barcodes and direct part marks (DPMs) to ISO/IEC standards. Omron complies with all of the latest standards for print quality.
When a defective label is found, the verification system can immediately stop the label from printing. The Omron systems also archive results for future FDA inspections and operational analysis. This data can be used to determine whether the printer is breaking down, or which label designs could be responsible for the largest share of errors.
Advantages of in-line inspection vs. off-line spot checking
When production errors are discovered via off-line spot checking, it might be necessary to discard entire runs of labels up until the last verified-compliant one. This wastes both time and resources. However, some customers think in-line inspection is less reliable than off-line inspection because of the challenges of accurately verifying barcodes during production.
Without in-line inspection and barcode verification, however, label production operations are essentially running blind. Print quality can degrade due to a wide variety of factors, including ribbon wrinkles, inconsistent label media, and the like, and this error potential can lead to serious costs and other negative impacts.
By using a tightly-integrated, ISO 15426-compliant print quality and barcode verification system like the Omron V275, manufacturers can achieve 100% label inspection for ISO and UDI needs without sacrificing throughput. The V275 software lets you work with hundreds of inspection templates, create reports, and manage users within a 21 CFR Part 11 production environment.
https://automation.omron.com/en/us/blog/print-verification-label-inspection