Disruptive Technology and the Future of the Automotive Industry
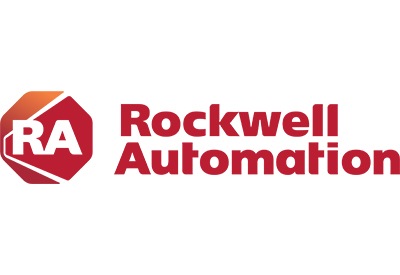
January 19, 2021
By Dominique Scheider, Auto&Tire Industry Manager, Europe, Middle East and Africa region
For years, urban citizens have been unhappy with their mobility experience: too much traffic causing long transportation times, too much noise, poor air quality, and limited parking options, to name but a few of the issues.
Then, in one day, in response to the COVID-19 pandemic, the order to “stay at home” has completely reshaped cities, forcing us to reconsider the way we live our lives and the way we do business. Things we once took for granted are no longer possible. Things we never thought possible are now commonplace. Digital transformation initiatives have been installed and launched in months, especially those focused on remote support.
At Rockwell Automation, we’ve used our technology and solutions to help manufacturers weather this storm. We’ve been able to offer assistance and help our customers adapt to the new normal. And we`ve helped car manufacturers to produce unprecedented quantities of hygienic masks and personal protective equipment in record time. What’s more, many of them found it more economical to install machinery to produce their own supply – removing another risk that could interrupt production.
But our mission to make the world more productive and more sustainable doesn’t end with mask production. These past months have demonstrated how ready people are to move to a new way of living and working, leaving the old ways behind. We’ve seen an enthusiasm for car sharing, cycling and other light e-mobility. We’ve seen a vote for zero emissions, a market for EV-PHEV cars, and a preference to work from home regularly, when possible.
The fallout from the COVID-19 pandemic, coupled with the EU’s CO2-reduction obligations and the rapid shift to e-mobility, poses a real concern for major car companies and Auto-T1 ecosystems. To survive the coming months, these manufacturers need the adaptability and flexibility provided by new technologies.
We have a role to play for this industry, and we are applying this in our own operations to secure our future.
Realizing the Potential of Disruptive Technology
Digital transformation has many facets, but it is built on a foundation of disruptive technology; technology that can advance every aspect of a business. Reimagining automotive production using digital technologies is helping manufacturers and suppliers stay competitive in this time of great change.
For research and development:
With people working from remote locations there are few opportunities to get together for some proper collaborative innovation. This is where Virtual Reality (VR) and Digital Twin simulations come in. Using a real-time 3D model, multiple users can access these designs and work together, sharing ideas and testing concepts. And implementing a new idea in a virtual model is much less risky than trialing something for real.
Many businesses are already well along this road, but some are only just discovering the possibilities because the pandemic has forced them to work in this way. And the advantages they’re seeing are causing them to completely revise their return-on-investment calculations for such strategic investments.
For production control:
For a long time now, car plants have operated using the supervisory control and data acquisition (SCADA) control system architecture. But now, the Industrial Internet of Things (IIOT) is becoming more and more connected, bringing together more “things”, allowing real-time scanning and data collection. This constant stream of data not only enables predictive maintenance, but it also helps operators make critical decisions, more quickly and more accurately.
This technology is still young but growing rapidly – providing even greater levels of connectivity and requiring fewer people on site. That offers considerable benefits to social distancing, and health and safety, as well as opening the door to the future potential of “dark factories”.
For remote assistance:
Getting expertise in the right location has always been a challenge, but even more so in this time of varying travel restrictions and strict social distancing measures. But even here, modern technology has the answers. Augmented Reality (AR) helps employees share real-time instructions and guidance without having to be physically present. When a remote specialist can see exactly what the field engineer is seeing, they can offer precise, step-by-step advice and adapt to any peculiarities specific to the job in hand.
With more employees working remotely, those remaining on site often don’t have the skills they need to keep everything up and running. That’s why Rockwell Automation partnered with PTC to provide access to its FactoryTalk InnovationSuite Vuforia Chalk – a collaborative AR remote assistance tool – and offers virtual training.
A Look into the Future
Ten years from now, these technologies – and technologies like them – will have changed the shape of the automotive industry. Here are four big trends we can expect to see:
1. New vehicle architectures
Already, we’re seeing pioneers lead the charge. Recently, Tesla began producing the rear chassis of the Tesla Model Y using Giga Press at its factory in Fremont, California. And growing trends towards electric vehicles and autonomous driving are changing the requirements of vehicle interiors. New materials, including composites and complex alloys, are becoming available, opening up new manufacturing opportunities – such as a lighter chassis or side panels without compromising passenger safety.
2. Mobility as a Service
Leading manufacturers will soon be developing and producing vehicles on a large scale but with a minimum of platforms, sometimes even sharing a platform with competitors. These platforms will be designed to support low-emission technologies (ZEM/PHEV) and provide advanced electronics and software for an autonomous driving experience. Although, autonomous driving will almost certainly remain on restricted conditions, even 10 years from now. All this demands more sensors around the car and 5G connectivity. We help T1 suppliers to design flexible lines, able to react quickly to market demands. For example, our ICT MagneMotion conveyor is a perfect fit for electronic assembly.
3. New regional brands
Smaller manufacturers, specific to certain countries or regions, will be developing vehicles for specific markets. In some cases, these will employ the platforms of the larger companies, in a win-win deal. But in others, much smaller plants will be used, while importing all the necessary parts. These “automotive micro plants” will be a continuation of today’s “glocalization” trends, relocating jobs and being promoted by local governments. Whether you’re using “micro” or “giga” factories, our Connected Enterprise approach offers scalable IT solutions to help you grow your business.
4. Full traceability of battery and car components
When it comes to lifecycle issues, and for the security of passengers, traceability is critical. It is essential that you can prove that the battery pack in your EV has eco-certification, and that it respects corporate social responsibility (CSR) requirements – “from the mine to the car”. This requires advanced technology and exacting standards. To this end, Rockwell Automation and our partners are collaborating with the European Green Deal set up by the European Parliament.
We can also expect digitalization to make supply chains more adaptable and robust. And imagine city vehicles that transport both passengers and provide last-mile delivery for goods. That’s the effect of big data, connectivity, and the IIOT, creating a total convergence of technologies.