AttaBox Enclosures Provides Guidelines For Effectively Modifying Fiberglass Enclosures With Holes And Cutouts
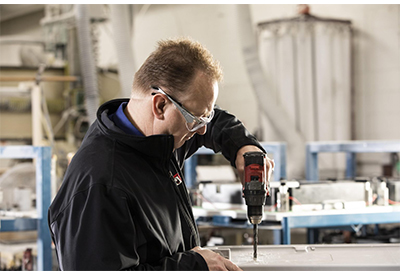
December 9, 2020
One of the benefits of fiberglass enclosures is the ability to create holes and cutouts. They can be modified to allow wire and cable to pass through, or the addition of vents, without the need for heavy machinery.
Physically modifying fiberglass can be effectively achieved if certain guidelines are followed. The comments made in this overview for modifying fiberglass enclosures with holes and cutouts are not intended as a tutorial on machining techniques but as a starting point for understanding how the physical properties of fiberglass respond to modification.
1.) Consider the benefits of factory-based modifications.
Although fiberglass enclosures can be safely and effectively modified on-the-job, there is merit in considering the benefits of ordering enclosures already modified to your specifications by the manufacturer. Fiberglass is a complex material made up of random glass strands in a polyester resin. Such random complexity is a positive strength factor of fiberglass but it affects the way a cutting tool or drill bit passes through it. AttaBox Enclosures is ideally set-up to perform a wide range of accurate modifications, including drilling and cutouts, and to then deliver enclosures to you ready-to-use.
2.) Pay close attention to the tools you use.
The ability to accurately drill holes or achieve cutouts in fiberglass enclosures starts with properly sharpened bits, cutters, and blades. Don’t begin your project without first ensuring that your equipment is in peak condition for use. The most common source of failure mode when drilling holes or making cutouts in a fiberglass enclosure is a dull cutting tool. Dull tools tend to rip or tear the polymer material. This is known as “delaminating” and will, at a minimum, be aesthetically unappealing. In worse case scenarios, delamination resulting from improper modifications can cause downstream assembly and functional performance problems.
3.) Cutouts and the use of a hole saw.
The easiest and least complex method to provide an opening in a fiberglass AttaBox enclosure is to use a fine-toothed hole saw. You must first lay-out the size and location of the cutout, pre-drill a small hole in the center within the cutout area for the hole saw to start, and then carefully cut out the area to be removed. There are methods that require less time and provide more precision, but the use of a hole saw can be accomplished in almost any environment. Keeping the saw perpendicular to the cutting surface, maintaining a consistent sawing action, and using a diamond/carbide impregnated saw or fine-toothed saw will provide the highest quality cutout with minimal edge chipping.
4.) Drilling techniques.
Putting round holes in enclosure walls or through the door of an enclosure is the most common type of cutout. As stated earlier: the single most important factor in doing so is keeping a very sharp tool.
One recommended tool is a carbide-tipped or PCD diamond-tipped hole saw or twist drill bit that will maintain a sharp cutting edge. HSS tools will also work but they will become dull resulting in excessive edge chipping and a poor looking hole. Also recommended: use of high RPM’s and low feed rates when using drills. This reduces chipping around the cutout.
Using a drill with a positive rake angle and thin points or split points can help reduce cutting pressure. Feed rates must also be constant and may even be reduced upon exiting from a hole to reduce flexing of the part when the drill exits. Using a solid back surface to support the part when drilling can also aid in reducing delamination and chipping.
5.) Punching techniques.
Using a standard hole punch, similar to what you would use with metal boxes, will produce a good clean hole but can leave chipped edges if the punch is dull. Once again: maintaining sharp tools is essential to producing clean cutouts. Remember too, that a pilot hole is required before using a standard hole punch. Manual or hydraulic punch actuators can both be used with composite materials.
6.) Routing techniques.
Using a router bit and router produces very clean holes and cutouts but also requires the holes and cutouts to be manually laid-out beforehand. It also demands a steady hand to stay within the layout lines. The use of a jig or fixture to help guide the handheld router or the use of CNC machining centers is helpful to ensure straight edges and clean cutouts. The use of diamond impregnated router bits is preferred for longevity but carbide bits will also work.
https://attabox.com/2020/08/27/drilling-and-modifying-fiberglass-enclosures/