GraceSense Case Study: Preventing Critical Breaker Failures and Extending Equipment Life Using Continuous Temperature Monitoring
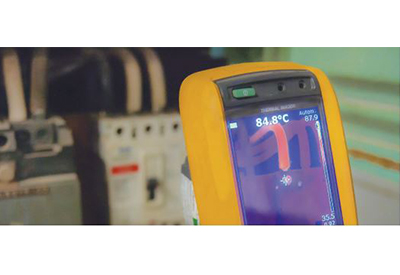
October 20, 2020
PROBLEM: FREQUENT BREAKER FAILURES DUE TO OVERHEATING OF CONTACTS & TERMINATIONS
Excessive inrush currents combined with harmonics triggered by Variable Frequency Drives (VFDs) in large motor applications put severe thermal burden on electrical components that are connected in the system. These conditions often lead to unpredictable early failures in key electrical components such as circuit breakers, bus bars and other terminations. While some of the leading indicators of failure include over heating of contacts, and frequent breaker tripping; others are catastrophic breaker failures that significantly impact the plant productivity metrics and uptime. Breaker failures tend to be very expensive in situations where they are connected to critical feeders, and replacements are either not readily available or difficult to find. In addition, the availability of a spare breaker, and well trained resources to perform the work could take anywhere between couple days to a week.
PATH-TO-SOLUTION
Many facilities use condition monitoring tools such as periodic IR thermography inspections to detect and overcome these breaker failures. Though highly effective, IR thermography reports cannot provide real-time temperature data other than the time the inspection was performed; in most cases the inspections are performed once in a year. Often in situations, it is difficult to simulate or replicate the actual load conditions of the breaker due to variety of operational reasons and other safety constraints. A continuous temperature monitoring solution such as one offered by GraceSense Hot Spot Monitor could diagnose the breaker’s root cause of the failures, by continuously monitoring the temperature data. Most “electrical problems” show up as excess heat that ultimately damages the electrical gear. By continuously monitoring the temperature data and analyzing the data trends of the specific breakers, engineers and plant maintenance personnel can draw databased decisions for unexplained temperature spikes at the LINE and LOAD side stabs of the breaker. After observing the repetitive pattern of temperature spikes over time, one can make operational tweaks to sequence the loads, reduce the inrush currents and manage harmonics. As a result, thermal stresses on the breakers are reduced and catastrophic failures are avoided.
Most large power systems have those “troublesome areas” that require constant monitoring and attention. Perhaps continuous temperature monitoring of this equipment might uncover the root causes for these trouble areas?
UNDERSTAND YOUR DESIGN LIMITS AND USE REAL-TIME DATA TO DRIVE DECISIONS
Many facilities employ electrical power distribution equipment that are decades old and require constant monitoring to keep up and running. As facilities expand their footprint, a progressive addition of capacity over years is applied to their aging power equipment. This leads to their equipment running at a relatively higher load than the originally designed capacity. The real win with continuous remote monitoring is the ability to monitor real-time data on a continuous basis while seamlessly integrating that data into your plant-wide SCADA system. The technology further helps to monitor and analyze trends of temperature data in real-time while your equipment is in fully loaded condition as with the normal use. Additionally, the equipment data is compared to the ambient temperature measurements to better diagnose the severity of the issues and reduce false flags.
Since most “electrical problems” show up as excess heat, a continuous temperature monitoring system could identify other issues beyond the typical hot spots caused by loose connections.
KEY BENEFITS OF CONTINUOUS REMOTE MONITORING:
- • Planned response to potential failures
- • Alarming functions when anomalies are detected
- • Increased uptime and productivity
- • Improved safety culture