Industrial Automation Can Help Critical Manufacturers Adjust to Disruptions Like COVID-19
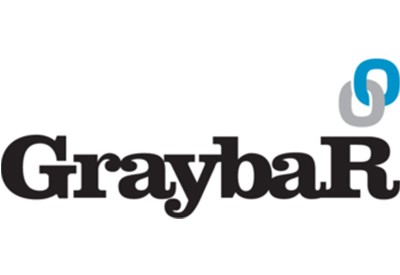
September 29, 2020
As the pandemic sent shockwaves through economies and supply chains across the world this year, manufacturers in critical sectors were forced to adjust quickly. To better weather unexpected crises, as well as industry shifts beyond COVID-19, manufacturers need to increase flexibility and resiliency in their supply chains. Increased automation and data availability in the plant can help.
COVID-19 Disrupts the Food and Beverage Industry
A McKinsey report from July 2020 on the U.S. food supply chain makes clear the scope and challenge of unanticipated changes in demand.
The food and beverage industry, accustomed to relatively stable consumer spending habits, saw rapid, radical changes in demand in a few months. Over the last five years, consumer spending on food in the U.S. had grown by about 4%, distributed relatively evenly between food-service companies (like restaurants) and retail locations (like grocery stores).
Early data predicted business as usual this year – until COVID-19 hit the U.S. in the spring. Social distancing and stay-at-home practices encouraged consumers to stockpile groceries, instead of visiting restaurants. Spending at grocery stores grew by 29% in March 2020, compared to March 2019, while food service locations saw a 27% drop in sales.
Food service customers cancelled orders in a massive wave that stranded stock with suppliers. Since packaging sizes for restaurant kitchens are much larger than those for a home cupboard, they couldn’t redirect that inventory to retail.
To reconfigure packaging lines optimized for food service, plant operators were looking at an investment that would take two to five years to pay itself back, alongside a 40% drop in revenue. And while in-store sales were rising, it wasn’t enough to offset the decline in food-service orders, leaving existing assets under-utilized.
Retail-facing manufacturers have struggled, too. Consumers are shopping differently – looking for more shelf-stable products, for example – and most plants have found limits on their ability to keep up, as well as disruptions to distribution networks.
Plants also face challenges keeping employees working in close quarters safe. When McKinsey released their report, 18 meat processing plants across the U.S. had shut down after employees contracted COVID-19, impacting over a third of the national supply of beef and pork.
With the duration of the pandemic and its long-term impacts on customer demand unclear, manufacturers struggle to optimize operations without raising costs or putting employees at risk. As the situation evolves, “companies will need to rewire for agility versus trying to achieve static optimization states,” the authors of the report conclude.
The Pandemic Isn’t the Only Thing Putting Pressure on Manufacturers
The food and beverage industry today is driven by a “farm-to-fork mentality,” says Jeff Alascio, U.S. End User Business Development Leader for Consumer Packaged Goods at Schneider Electric. Consumers care more about sustainability – they want to know where their food comes from, and how it’s made.
New regulations around food safety also require the ability to quickly track ingredients back to their source during a food poisoning outbreak.
This kind of tracing and transparency requires the collection and calculation of an enormous amount of data along the supply chain.
Meanwhile, manufacturers face constraints on CapEx and OpEx expenses as they try to lower costs and better monitor energy and water usage, raw materials and more to increase the sustainability of operations.
Plant operators want to boost efficiency and yield while increasing the flexibility of their operations, as well as maximizing the availability and value of assets. According to Jeff, most plants report that machines are operating at about 60% overall equipment effectiveness (OEE), “and that’s actually a good number” – but they want to reach 90% or above.
Industrial Automation Solutions Help Plants Operate More Efficiently With Better Data
“Operational improvement, at the end of the day, is all about efficiency and flexibility,” says Simone Gianotti, IIoT Business Development Manager for Industrial Automation at Schneider Electric. In the food and beverage industry, changing consumer preferences mean that “flexibility and time to market are extremely important parameters.”
Simone started his career on the factory floor, working with customers to develop and commission software for machines working, handling and packaging material. After traveling across Europe, Asia and America as a trainer, he moved to the U.S. in 2009. In his role as Motion Product Manager, and then his work with Schneider’s global Smart Machine group, Simone had a front-row seat to the development of the first smart machines.
Industrial automation today works in three layers. Connected devices like drives and push buttons collect information, and pass it to an edge control system made up of PLCs and HMIs, which use that information in real time to keep the factory running. Apps, analytics and services analyze all this data at a higher level to suggest preventative maintenance and offer predictions.
For example, a plant supervisor might wake up to an email first thing in the morning saying a particular cell is on track to run short of raw material by 10 a.m. When they get to the plant to start their shift, they can take immediate action.
“15 years ago, a typical SCADA system would just give you data. It wouldn’t give you actionable opportunities; you had to make a decision on whether or not you were going to use [that data],” says Jeff.
Today’s connected plant can help operators manage performance more effectively in real time and stay one step ahead of maintenance needs to reduce unplanned downtime. Augmented reality tools and HMIs accessible through the cloud can also allow for remote monitoring and management – which is critical during the pandemic.
While the COVID-19 crisis has highlighted the importance of automation solutions, they can also boost a plant’s efficiency once it returns to normal operations.
By implementing an end-to-end automation solution from Schneider, a sugar plant in South Africa was able to improve the reliability of its equipment and reduce downtime, leading to a 20% increase in throughput.
When a Canadian grain company approached Schneider for an automation solution to scale operational practices across its distributed facilities, it saw an 80% reduction in development times and a 10% increase in shipping efficiency.
Ultimately, a connected plant can help manufacturers collect more – and more useful – data, act on it more quickly and learn from it over time. Increasing flexibility and resiliency in the supply chain will set a business up to better weather industry shifts and unexpected crises.