High-Quality Metal Parts for the Airbus A320 Made With Precise, User-Friendly CNC Tech
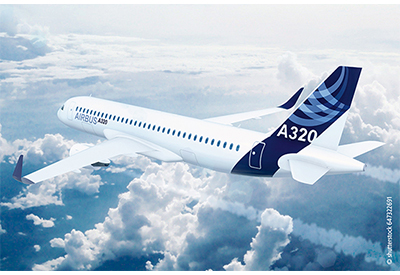
September 21, 2020
In aircraft construction, exceptional component quality and precision are crucial, for obvious reasons. However, sheet-metal aircraft parts are often extremely large, making machining and handling problematic. Working closely with CNC specialist Penta-Tec and with milling specialist A&T – a company that supplies Premium Aerotec, an Airbus subsidiary, with structural components – Harmuth CNC-Frästechnik has built large-format milling machines that use PC-based control technology from Beckhoff to successfully overcome these challenges.
Penta-Tec CNC-Automation GmbH, headquartered in Grödig, Austria, began developing complete CNC machine solutions in the 1990s. As Managing Director Dieter König says: “Even then, our focus was less on classic CNC machine tools and more on applications like architectural model making, wood working solutions for smaller workshops, and the arts and crafts. Our user base, as a whole, was generally less CNC savvy and had a different set of expectations regarding this kind of control system. They wanted ease-of-use and the ability to intervene flexibly at any point in the workflow, plus a lot of little add-on features besides the main NC processing capabilities.”
Penta-Tec chose from the outset to build on PC technology, which at the time was becoming increasingly common in machine control, and went on to develop a fully graphical user interface that incorporated features such as a graphical editor, a 2½D CAM system, tool and material management, and machine operation functionality. According to Dieter König, this broke ground for the subsequent adoption of PC-based control technology from Beckhoff in 2011: “Their unique control solution had become increasingly popular, both in mechanical engineering and among CNC machine builders, and was constantly evolving to accommodate the individual requirements of its broad customer base. At the same time, CNC software and human-machine interfaces for CNC systems were becoming our core area of expertise. We therefore stopped making our own machines and used Beckhoff technology instead, which enabled us to concentrate on creating CNC solutions for customers in the machine building sector.”
PC-based control provides greater flexibility for machine builders
One of these machine builders was Harmuth CNC-Frästechnik, based in Nordenham, Germany, a company that makes 3D milling machines and specialty systems. Managing Director and trained aircraft engineer Andreas Harmuth explains some of their typical requirements: “With large-format milling machines, the dimensions and the rigidity, in particular, are critical factors. The machines range in type from light-duty systems capable of operating dynamically at high speed, to heavy-duty systems with large cutting heads for high-precision face milling, and everything in-between. We can be extremely flexible with the machines we build, largely due to the open Beckhoff control technology, which lets us easily scale things such as the computing power or the number of axes to suit our needs. At the same time, PC-based control offers us a lot of options for remote maintenance. Reliability, too, is important, both with PC-based control technology and with Penta-Tec’s software, as this helps us keep service costs to a minimum.”
The advantages of Harmuth’s milling systems come to the fore in applications such as the fabrication of large sheet-metal parts for the Airbus A320 series of aircraft. The parts are supplied by A&T Manufacturing GmbH in Nordenham, as Managing Director Marc Bochinger explains: “Airbus, or rather Premium Aerotec, the subsidiary responsible for large sheet-metal parts, is our biggest customer. Besides supplying all their material (the sheet aluminum), we also form and machine large and complex structural components for them. What sets us apart at A&T is that we concentrate completely on the customer’s needs and come up with an optimized production and logistics solution in as short a time as possible.”
The power and versatility of standard control technology
Roman Felber, Technical Director at Penta-Tec, also highlights the breadth of production technology in use at A&T: “The big challenge at A&T is the need to constantly implement new machine functionality. Optimizing a production process might call for a workhead spindle or a second spindle, for instance. And this in turn relies on highly flexible control technology that supports a full range of variants as standard. A&T and Harmuth CNC-Frästechnik work together closely to optimize the machines – more than once, if necessary – to maximize their potential in production. PC-based control from Beckhoff covers all our requirements, not least because we can change the way axes are coupled in TwinCAT if we need to.”
In 2010, Penta-Tec found that rising functionality demands were pushing the performance of its proprietary control system to the limits. Says Dieter König: “We needed to handle additional automation tasks, parallel to the actual CNC processing, and our system often had to incorporate special sensors or actuators from different vendors as well. At the same time, both the drive performance available and the flexibility in terms of the number of axes were significantly limited. It became obvious that we needed a new, flexible control system, capable of delivering the performance we needed. After some research and analysis of the controller market, PC-based control technology from Beckhoff soon stood out as the ideal solution.”
First, König says, this was because Beckhoff drive technology – such as the EL7047 stepper motor terminal, AX5000 Servo Drives and AM8000 servomotors – covered every conceivable requirement, from simple auxiliary stepper axes and servo axes to the ability to incorporate linear and hydraulic axes. Second, the exceptional range of EtherCAT Terminals available offered solutions to support any kind of application on the I/O side, particularly given the breadth of specialty hardware available from third-party vendors due to global acceptance of the EtherCAT standard. Third, Windows as the underlying operating system was another key factor in Beckhoff’s favor because it allowed the Penta-NC CAD/CAM/CNC user interface and TwinCAT to run on the same target system – an ideal setup. And fourth, there was the extensive portfolio of IPCs, such as the CX2040 Embedded PC and the CX5120, which were ideally suited to machine control and centralized vacuum control purposes respectively.
TwinCAT NC I as a flexible control platform
Roman Felber, too, highlights the easy interoperability of the two software systems: “Implementing ADS communication between the Penta-NC HMI and the TwinCAT NC I control platform involved little overhead. TwinCAT NC I also provides an affordable platform for a diverse range of CNC applications. With its ability to incorporate auxiliary tangential or gantry axes, for example, it supports economical solutions, even for complex CNC tasks.” For Felber, TwinCAT NC I’s immense flexibility is another benefit. Axis parameters can be changed directly from the PLC, which means correction values based on visual inspections can be fed to the axis position controller in real time. Lead screw error correction, X/Y cross compensation or machine bed leveling, too, can be implemented easily in the same fashion. Also, tangential tracking can be enabled or disabled on a tool-dependent basis – to switch, for example, a milling spindle ordinarily operated as a free-running, speed-controlled asynchronous motor over to servo operation and use it as a tangential axis for blade cutting operations. Highly advantageous, too, are the master/slave coupling feature and the ability to flexibly configure individual axes to form interpolation groups, which allow complex systems to use multiple z-axes either concurrently, or separately for other tasks.
The ability to split interpolation groups and recombine them in other forms is useful. For instance, it makes it possible, in the event of a fault, to manually extract a saw blade, applied at a tangent to perform mitered cuts, from the material it is cutting. To do this, the NC interpolation group is split up. Depending on the miter angle and rotational angle of the C-axis, individual coupling factors are then computed for the X and Y-axes and coupled to the Z-axis. If the Z-axis is then shifted by hand wheel, all three axes travel in such a way that the saw blade withdraws from the material in the exact direction of the cut.
Precise, energy-efficient production of aviation-grade sheet metal
A&T uses large-format milling machines from Harmuth CNC-Frästechnik to fabricate aircraft fuselage panels along with a broad range of structural components milled from aviation-grade sheet metal for the Airbus A320 series of aircraft. For Roman Felber, one of the big challenges with machines of this size is maintaining precision: “With machining surfaces that measure as much as 16 x 4 m, it’s near impossible – economically, at least – for machine builders to achieve precision in the tenth-of-a-millimeter range. We use software to enhance the precision. Once a machine is set up on site, it’s measured up with a laser tracking system, using a set of largely automated functions provided in Penta-NC. This takes account of any machine-dependent tolerances and workpiece-dependent parameters. On machines of this size, several components are often clamped in place at the same time, which also means adjusting for individual tolerances in position and form. By taking these various steps, we can keep the absolute positioning precision to within +/-0.01 mm.”
Vacuum clamping offers a simple and hugely flexible means of fixing sheet metal in place in milling systems but it can easily require 15 to 20 kW or more of suction power, depending on the size of the machine. However, significant energy savings can be achieved by ramping the suction power up or down as needed. Andreas Harmuth adds: “With smaller-scale parts or material that has not yet been machined, the amount of suction – and pump power – don’t need to be so high. However, when a large number of smaller parts are machined, and the air leakage rate increases during the milling process, the power has to be ramped up.” To maximize power savings, the clamping area is divided into as many as 32 sections so that it can adjust the pressure specifically to match a given metal part to be machined. Also, the amount of suction needed to safely secure a given part is calculated according to the material parameters and surface area. An EM3701 pressure measuring terminal records the current suction level and passes it to the PLC as a control value, and once the machining process is complete, the suction power falls back automatically to a pre-set stand-by level that simply prevents the part from slipping. This is a significant advantage, as Marc Bochinger explains: “Compared to simply switching the vacuum control system on and off, the annual energy savings are around 50% to 60%.”
On top of this, says Bochinger, the vacuum controllers from four machines have been consolidated onto a single CX5120 Embedded PC. “The actual suction pressure data for each machine is still processed locally by the EM3701, and then passed, together with the calculated nominal values, to the CX5120 over ADS. If a fault occurs in one of the vacuum pump systems, the suction power of another pump can be boosted instantly to compensate. This redundancy concept essentially eliminates the risk of costly damage to parts through a vacuum clamp system failure. The EM3701 is also used to provide process-dependent control of the suction power, which can help detect problems with the suction head or the suction pipe system. This capability means the system delivers data that’s important for preventive maintenance and so helps safeguard machine availability.”
https://www.beckhoffautomation.com/english.asp?press/news3520.htm