Avoid Costly, Last-Minute Surprises With Virtual Commissioning
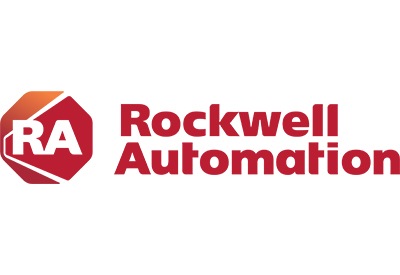
April 13, 2020
By Matthew Masarik, Marketing Manager, Design Software, Rockwell Automation
It’s that moment you dread: You’re doing controls testing on a new machine as a customer’s start-up date approaches, when you discover a problem.
The issue could be almost anything. It could be a functionality problem, like an unexpected stoppage or a missing sensor. Or it could be a last-minute customer concern, like the HMI’s sequence or layout.
Whatever the issue, fixing it can be expensive. Some industrial companies, in fact, report that fixing a machine issue during commissioning can be up to 100 times more expensive than fixing it in the design phase. And of course, there’s also a risk that the issue will cause you to miss your customer’s production start date.
It’s for these reasons that some machine designers are adopting virtual commissioning. This process uses a digital model and simulation of your machine to perform controls testing before you even build a machine. This can help you identify design issues earlier in the build cycle and ultimately help you better meet customer deadlines.
Change What’s Possible
Virtual commissioning is made possible using software that creates a digital twin of your machine design and connects to the real operational logic of its control system. A dynamic digital twin is more than a 3D visual model. You can apply physics to your design and run it, so you can see how it operates and interacts with people or other machines.
You can do all this as soon as your machine design is complete, long before you cut steel or order parts. This can help you take controls testing off the critical path and avoid making changes at the 11th hour. Instead, when you arrive on site, your machine is ready for factory acceptance testing, and you’re not worrying about missing customer deadlines.
Some machine builders are discovering the tremendous savings that virtual commissioning can help them achieve.
One of them is Daifuku Webb, a maker of material handling systems. The company uses virtual commissioning to test PLC code in-house, before it goes to the field. In one project for an airport customer, Daifuku Webb used virtual controls testing to reduce the amount of time its engineers spent in the field from several months to about three weeks.
And the company sees other benefits from virtual commissioning beyond time savings.
System installations go more smoothly because the PLC code functions have already been tested. And the company is able to thoroughly demonstrate the functions of its systems before bringing them to the field.
Easy as 1, 2, 3
Creating a digital twin of your machine using simulation software is a straightforward process that involves three primary steps.
First, you bring in the machine’s CAD. Then, you mockup the machine’s movements and devices like sensors on the CAD. Finally, you connect the CAD to the controller and its tags. And with that, you have an open sandbox where you can begin testing out your machine and its logic digitally, long before you cut steel or order parts.