5 Common Mistakes to Avoid when Implementing Autonomous Mobile Robots (AMRs) in Your Facility
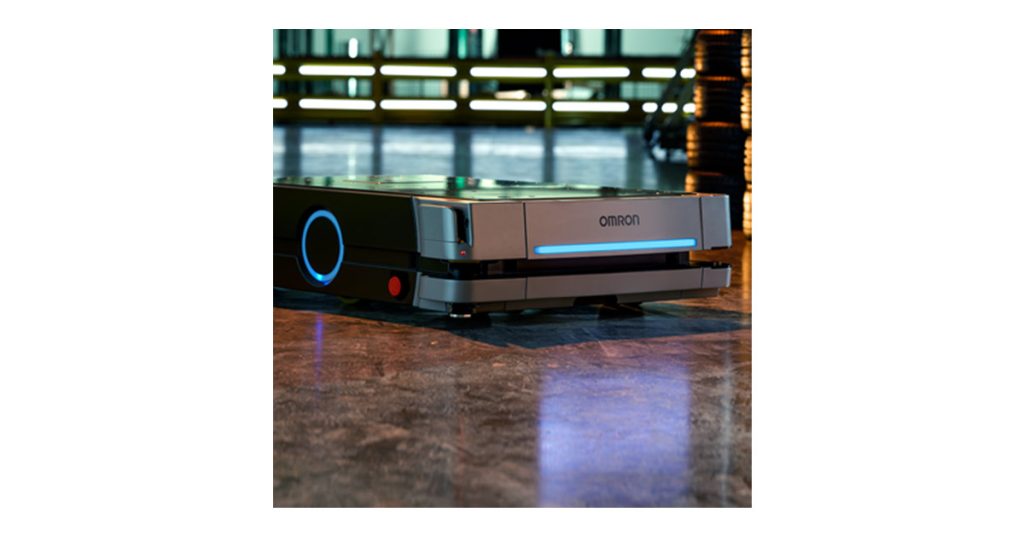
August 22, 2023
As technology advances, autonomous mobile robots (AMRs) have emerged as valuable tools for improving efficiency and productivity in various industries.
From warehouses to manufacturing facilities, these intelligent machines are revolutionizing the way manufacturers handle tasks and streamline operations.
However, deploying AMRs successfully requires careful planning and consideration. In this blog post, let’s explore some common mistakes that people make when implementing autonomous mobile robots in their facilities and provide insights on how to avoid them.
1. Insufficient planning
One of the most significant mistakes made during the implementation of AMRs is inadequate planning. Rushing into the deployment without thoroughly assessing your facility’s needs and requirements can lead to inefficiencies and suboptimal results.
Begin by identifying specific areas or tasks that could benefit from automation. Engage with stakeholders, including employees and management, to understand their pain points and expectations. A well-defined plan that aligns with your facility’s goals will help set the stage for a successful AMR implementation.
2. Lack of compatibility
Another common mistake is overlooking compatibility between existing infrastructure and AMR technology. AMRs are very flexible and can operate in a wide variety of applications, but like most things, there are limits; so it is crucial to assess whether your facility is ready to accommodate AMRs seamlessly.
Consider factors such as floor conditions, lighting, and Wi-Fi connectivity. Evaluate the compatibility of your facility’s layout and infrastructure with the navigation and communication systems required by the AMRs. Conducting a thorough evaluation and addressing any potential limitations in advance will prevent unnecessary setbacks during implementation.
3. Inadequate staff training
While AMRs are designed to work autonomously, it is essential to provide proper training to your staff members. Failure to train employees adequately can hinder the successful integration of AMRs into existing workflows.
Employees should understand how to interact with the robots, handle exceptions, and perform basic troubleshooting. Encouraging open communication and providing ongoing training and support will empower your workforce to embrace AMR technology effectively.
4. Overlooking safety considerations
Safety should always be a top priority when deploying AMRs. Ignoring safety considerations is a significant mistake that can lead to accidents and injuries.
AMRs are built with onboard sensing and safety rated control systems designed to prevent collisions, however every application is different; so it is critical that the AMR is configured properly to ensure safe operation for the application it is tasked with.
For example, there is less of a safety risk with an AMR moving foam pads compared to the same AMR moving 500kg of metal parts stacked high on a pallet due of the physics involved. Both applications are viable and can be done safely, however the AMR must be configured properly to ensure safe operation of each.
Additionally, it’s important to conduct a thorough risk assessment and involve your health and safety team to identify potential hazards and implement appropriate safety measures. Regular safety audits and ongoing monitoring will help maintain a safe working environment for everyone.
5. Neglecting maintenance and support
AMRs, like any other complex technology, require regular maintenance and support to ensure optimal performance. Neglecting this aspect can result in increased downtime and reduced efficiency.
It is crucial to develop a robust maintenance plan that includes routine inspections, software updates, and preventive maintenance. Additionally, it is helpful to establish a strong partnership with the AMR provider or manufacturer to receive timely support and access to spare parts. Proactive maintenance and reliable support will keep your AMRs running smoothly, minimizing disruptions to your operations.
Implementing AMRs in your facility can be a transformative step toward improving efficiency and productivity. By avoiding the common mistakes we’ve reviewed here, you can ensure a successful integration of AMRs into your facility.
Remember, careful consideration of these factors, combined with ongoing monitoring and improvement, will pave the way for a seamless and productive collaboration between humans and robots in your facility.

https://automation.omron.com/en/us/blog/mistakes-to-avoid-when-implementing-AMRs