Rethinking innovation for the Fourth Industrial Revolution
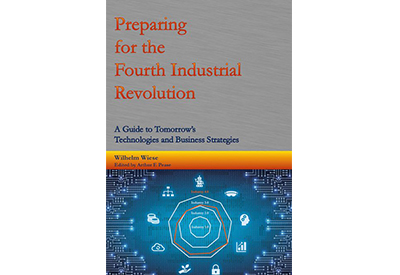
February 4, 2020
With the advent of the Fourth Industrial Revolution and the increasing speed at which products and entire markets are changing, operational excellence has become more business critical for all organizations than ever before. In a world in which development and deployment are a continuous process, development models and practices based on update-and-maintenance cycles of months or even years have become inadequate. Hence, the Fourth Industrial Revolution demands a paradigm shift in terms of bringing new products, technologies and solutions to market in such a way as to enable them to keep pace with expectations.
In this context, an important buzzword is solution development. Many business leaders enthusiastically announce that they plan to digitize their plants or transform their organizations from product companies into solution providers. But why all the hype? Isn’t that what engineering is all about? When it comes to keeping pace with or even staying ahead of the expectations curve, the real challenge is not solution development, but problem identification. To put it bluntly: a business must define the problem before it can propose a solution. And in the context of the Fourth Industrial Revolution, that means figuring out how new technologies may be able to offer competitive advantages over traditional ones. This is the road to identifying value for plant operators and new revenue streams for industrial product and service suppliers.
But that’s easier said than done. What may sound like exciting new productivity stimulating digital strategies when announced at board meetings can quickly turn into run-of-the-mill responses when translated into concrete assignments. By the end of the day, what’s actually delivered is standard solutions that ignite only a few horsepower worth of pull for existing products and services under the umbrella of digital solutions. Furthermore, many such assignments end up being applicable to only very specific areas and are not scalable.
Pseudo digital solutions of this ilk can indeed be good for business and can indeed make plant operators happy, but they neither unleash step changes in productivity to improve the bottom line nor do they create new revenue streams for solution providers that can significantly improve the top line. To take a meaningful slice of the predicted multi-billion-dollar potential of the Fourth Industrial Revolution, companies need to challenge current technologies. Therefore, they need to start from the shop floor to identify domain- or technology-specific issues that can be replicated across sites or domains with the objective of revolutionizing whole industries.
Hence, any solution development must start by identifying the problem statement and the value of a solution. Only after completion of the second step, should an organization initiate the innovation process and evaluate in what ways new Fourth Industrial Revolution technologies can be disruptive and add value for its customers’ businesses.
The vast promise of wicked problems
Where should this overall process begin? A good starting point is the core of today’s very popular design thinking process. A five-phase description of this process is described by Plattner, Meinel and Leifer as: “(re)defining the problem, need finding and benchmarking, ideating, building, testing.” The process may also be thought of as a system of overlapping spaces rather than a sequence of orderly steps: inspiration, ideation, and project implementation may loop back through each other more than once as a team refines its ideas and explores new directions.
Design thinking is especially useful when addressing what Horst Rittel and Melvin Webber referred to as “wicked problems,” which are problems that are ill-defined or tricky. Far from being something to shun, such problems can hold vast promise. Indeed, the real danger lies in limiting our thinking to well-defined problems because these tend to cause us to come up with solutions that are based on standard rules or current technical knowledge.
To create a picture of what wicked problems are in terms of decision-making processes in the context of the Fourth Industrial Revolution, it is helpful to adapt the Johari window.
Originally created by psychologists to support self-help groups, the Johari window can help guide users to the identification of heretofore hidden problems, and thus put them on the road to the identification of novel solutions. The window can be subdivided into four key solution areas, the first of which is incremental solutions. For example, if a problem is known to you as well as to others in an industry, then you can expect that it will probably be solved soon with today’s technologies or with some incremental changes.
The second area is low hanging fruits. Here, problem statements are known to industry experts such as plant operators, who are aware of an improvement opportunity, but a solution provider does not yet know about it. This area can be addressed in customer workshops, often called co-creation workshops, where solution providers start understanding the challenges faced by plant operators and can bring in their technical experts to come up with a solution. The resulting exchange of information is designed to crystalize into well-defined problem statements that have a good chance of providing solutions that can, in turn, be replicated and scaled up.
The third area is hypothetical problem statements. Here, risks are high because the solution provider might have to invest a lot of money in development with no certainty of success since the solution is not considered to be critical or does not add enough value.
Finally, we come to the fourth area: wicked problems. These are – potentially – the fuel of the Fourth Industrial Revolution. Here, the level of risk is obviously high because the innovation process is complex, and some ideas are sure to fail; but solving wicked problems will be disruptive, which means that the resulting solutions stand the highest chances of being hugely successful.
How ABB licked a wicked problem
Recently, ABB addressed a wicked problem in collaboration with a key customer in the chemical industry. The problem was that the customer’s plant operator was occasionally faced with unexpected foaming in their batch reactions. In the chemical and pharmaceutical industries, the term “batch process” refers to the execution of several production steps to generate a final product according to a stringent recipe. The foaming caused product impurities so serious that a batch that required seventeen hours to produce had to be discharged and recycled. In addition, this resulted in many unproductive hours to clean tanks and pipes.
Batch processes target products that follow a high-quality standard. Nevertheless, given the number of variables involved, no two batches are identical. Factors such as the quality of input materials, batch size, temperature, humidity and other environmental factors can interact to create anomalous circumstances. What’s more, managing the production process itself often includes hundreds of process variables with complex interrelations.
Given these factors, detailed batch monitoring is an essential part of understanding and managing this highly dynamic process. But in this case, although the customer had a vast amount of data available, it was not equipped to link the data from more than 100 process variables from several hundred batches with other production data such as raw material specifications, power consumption and process variable measurements.
Working closely with the customer, ABB deployed experts who applied Big Data analytics to determine the root cause of the problem. Their work uncovered suspicious patterns, such as power consumption peaks as well as steam flow anomalies. Finally, they co-invented a prediction concept capable of producing highly accurate early warnings circa 30 minutes before foaming is likely to occur.
Throughout this collaboration the team used ABB’s BatchInsight, a product that combines techniques from business intelligence, classic data analysis and machine learning to support process experts in holistically analyzing batch processes.
Concretely, what does this example tell us? Clearly, it illustrates that disruptive changes in solution development open the door to the implementation of new Fourth Industrial Revolution technologies that can play a major role in identifying wicked, ill-defined problems. This process can then be followed, for example, by an artificial intelligence-based root cause analysis to derive solutions nobody has thought of before. All that’s needed in order to start digging deeper into data and technology is an initial hunch!
But even hunches need a trigger. So, a good starting point is to begin visiting your plants and asking whether there are any productivity or quality issues that managers have not been able to explain. That’s where you’ll hear plenty of hunches. From there, one can apply various interrogative techniques, such as an Ishikawa diagram [5] to explore cause-and-effect relationships. The key factor in applying this iterative interrogative technique for analyzing wicked problems is to not look for their root cause. The technique is applied to define the scope of the data that is needed in order to collect and to determine which technology should be applied to find a cause-and-effect relationship that is not detectable with the data and knowledge about this data that’s in people’s heads. This boils down to a three-step approach.
The first step is about scoping, where the target is to find data that might correlate but which was not considered in this context before. In the second step, the latest technology, such as machine learning or artificial intelligence, is applied to the data to obtain new insights about possible root causes. The third step is about developing a solution. And here’s where things really get exciting. Solution development for wicked problems typically begins with several proof-of-concept studies based on building models or digital twins. These are essential because the outcome of machine learning algorithms is associated with a given level of probability that needs to be proven before an implementation in a real industrial process can be performed.
Can any plant operator, system provider or device manufacturer do this alone? Probably not. But an excellent problem-solving model is to break this process down in three steps: Why-What-How, with the latter distinguishing between how problems are solved in a traditional way and how they should be solved in a collaborative manner to be disruptive.
Solving wicked problems through co-invention
Starting from the ‘Why’, a deep understanding of the customer’s needs, goals and differentiators should be the foundation of the common solution process. Without this, one runs the risk of merely implementing technical fixes and partial solutions rather than the solution itself. In other word, the team needs to understand the target plant’s production processes, value chain and how this impacts plant productivity and the features of the produced products.
Only after developing a clearly defined problem statement is it time to apply domain knowledge and the latest technologies such as Big Data analytics or machine learning to identify the root cause of the problem and thereby “What” needs to be changed.
The third step is to address “How,” which is the core of the paradigm shift from collaboration to co-invention. This is essential because the objective is not to apply an immediate fix for one specific plant or operation area, but of applying Fourth Industrial revolution technologies such as artificial intelligence and autonomous system concepts to making a disruptive change to plant productivity or the features of the produced products that can be replicated in all of the customer’s plants or even scaled up for a whole industry.
All in all, developing solutions for today’s wicked problems offers a high probability of unleashing the potential of many new Fourth Industrial Revolution technologies. Furthermore, the application of solutions to industrial environments will continuously prove and improve machine learning capabilities. Finally, this process will rely on the ability to pre-evaluate solutions, which will require the creation of ever more digital twins. These will, in turn, generate the data that will be the foundation for and accelerate the development of tomorrow’s autonomous systems. In other words, co-invention to solve wicked problem statements will unleash the potential of new technologies and thereby accelerate industries to a level of productivity that is hardly imaginable with today’s technology.
https://new.abb.com/news/detail/56312/rethinking-innovation-for-the-fourth-industrial-revolution