Get More Than You Pay For From AutomationDirect
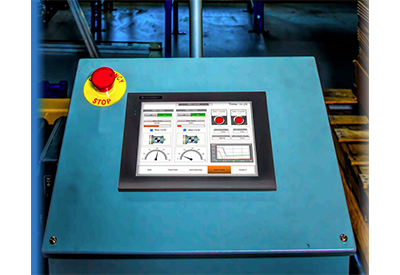
October 6, 2020
Enclosures Today
Enclosures are widely used to house electrical or electronic equipment along with switches, knobs and displays while providing a safe installation that prevents electrical shock to equipment users and protects the contents from the environment.
Today’s enclosures are designed with features and materials that allow safe and protective use in hazardous areas, but also designed to be pleasing to the eye. Enclosures can experience high demands for heat dissipation, radio frequency interference and electrostatic discharge protection, as well as functional, esthetic and commercial constraints.
An important product development related to enclosures is climate control. These systems were created to manage the heat growth due to higher cabinet heat loads and the use of more sophisticated electrical drives and equipment. In addition, enclosures are being installed closer to production lines and equipment, exposing them to harsher environments.
To withstand all this, enclosures today are available in a variety of materials and NEMA ratings designed to protect against surrounding conditions.
Types of Enclosures
Wall-Mount Enclosures
Designed to house electrical controls, terminals, instruments and components. Provide protection from dust, dirt, oil, and water.
Junction Boxes
Designed for use as surface-mounted junction boxes, service boxes, switch boxes and cutout boxes.
Pushbutton Enclosures
Pushbutton enclosures with standard openings to fit 30.5mm and 22.5mm mount pushbuttons, switches and pilot lights. Available in various NEMA ratings for dirt, dust, oil and water protection.
Floor-Mounted and Freestanding Enclosures
Commonly used for machine tool applications to house motor starters, drives, contactors, and PLCs, as well as a wide variety of other electrical and electronic equipment.
Disconnect Enclosures
Used to house disconnects from many manufacturers, these enclosures offer NEMA 4, 4X or 4/12 protection in a wall-mount style, and are also available in NEMA 12 wall mount, floor mount and free-standing versions.
Consoles and Consolets
Typically used to house electrical and electronic controls and/or instruments. Sloped surface models can be used to mount pushbuttons, pilot lights, meters, switches and other devices. Heavy duty construction protects contents from dirt, dust, oil and water.
Custom Cutout Enclosures
A selection of enclosures that can be customized with factory cutouts designed to your specifications, then shipped ready to install components to get up and running quickly.
Wireway and Fittings
Designed to protect wiring against rain, sleet and snow for outdoor installations, or protect against dripping water indoors.
Slope Top Enclosures
Designed to house and protect electrical and electronic components from harsh, dirty environments. Stainless steel models are perfect fit for mounting electrical or high-tech electronic equipment in a variety of indoor and outdoor settings.
Windowed and Clear Covered Enclosures
Enclosures with a window or clear cover allows a view of the inside of the enclosure without opening the door and exposing the internal components.
Enclosures with Knockouts
Designed for use as wiring boxes and junction boxes to house and protect electrical and electronic components from harsh, dirty environments.
Dual Access Enclosures
Designed to protect electrical and electronic controls, components, and instruments in typical industrial environments with dust, dirt, oil and dripping water. Dual access enclosures are designed to provide additional access from the rear side of the enclosure if necessary.
Flush-Mount Enclosures
Enclosures with an external frame that allows it to be recessed in wall. These enclosures are typically used in applications where external space is limited or in high traffic areas.
Padlocking Enclosures
Enclosures with door or a latch that includes a padlock hasp where additional security is required.
Keylocking Enclosures
Enclosures with keylocking latches that provide controlled access for additional security.
Enclosure NEMA Ratings
Those of us who have worked professionally in the U.S. electrical control industries have a good understanding of, and a certain level of comfort with, NEMA standards; most notably as they pertain to electric motors, motor controllers and enclosures. For the most part, American-based companies require that the electrical components and enclosures used in any given project adhere to NEMA standards.
When working with American manufacturing facilities, NEMA standards are still king. NEMA standards describe each type of enclosure in general and functional terms, and specifically omit reference to construction details. In other words, NEMA specifies what an enclosure must do, not how to manufacture it.
NEMA performance criteria and test methods are used by Underwriters Laboratories (UL) and the Canadian Standards Association (CSA) as guidelines for investigation and listing of electrical enclosures. The tested enclosures are then authorized to carry a label by UL or CSA to prove they have passed the required tests and meet the applicable UL and/or CSA standard.
Importance of Enclosure Thermal Management
Most automation and electrical devices must be housed in a control enclosure when used in industrial environments. This includes controllers, drives, power supplies, disconnects, fuses, terminals, relays, contactors and more. Changing temperatures in the plant or outside may demand use of both cooling and heating to maintain an optimal temperature or devices’ safe operation.
There are many reasons to cool or heat an enclosure, some related to unique, site-specific needs. However, the most consistent and common reasons are:
Reasons for Cooling Enclosures
• Remove excessive heat caused by devices housed inside the enclosure
• Extend component life by maintaining low maximum operating temperatures
• Prevent malfunction due to overheating
Reasons for Heating Enclosures
• Control relative humidity inside the enclosure, typically below 65%
• Maintain a consistent temperature inside the enclosure to guarantee optimal operating conditions and prevent condensation.
• For situations where the enclosure may need to be cooled during the day and heated at night
A Few Tips When Selecting an Enclosure
What kind of environment is your enclosure going to be in and what level of protection do you need?
Your enclosure’s primary function is to protect the equipment inside it from the surrounding environment. Refer to the previous section “Enclosure NEMA Ratings” and select a rating that protects against the type of environment where the enclosure will be located. Keep in mind that it is just as important not to over-specify the protection level of your enclosure as it is to underspecify, as increasing the protection level typically increases the cost of the enclosure.
Determine the Security Required
Your enclosure needs to protect its contents from unauthorized access to the components it houses. For low-risk installations, a screw cover, lift-off cover, or single door with clamps may be sufficient. In higher-risk installations, an enclosure with keylocking and/or padlocking capabilities may be needed.
Determine the Enclosure Size
Physical space for your components is not the only requirement. Considerations like heat dissipation and venting must be taken into account. First, determine the height and width for your enclosure by laying out the footprint space needed for your control components. The size of the enclosure will determine if you have the option of a single-door, two-door or wall-mount style. The height and width of your enclosure will determine whether it can or needs to be a wall-mount, floor-mount, or freestanding style enclosure. Next, determine the panel depth and remember that the subpanel mounting takes up a small portion of the depth. Also, any pushbuttons, operator interfaces, indicators, meters, etc., that you plan to mount on the enclosure door will occupy some enclosure depth.
Determine Enclosure Thermal Management Needs
Your enclosure must be able to dissipate the heat generated by the components inside of it either alone or by adding a cooling device. You might be able to side-step additional cooling by upsizing your enclosure to increase the surface area through which heat is transferred to the atmosphere. Always remember that the heat dissipation method you select must be compatible with the enclosure’s NEMA rating. Simple applications may use a simple louver plate for adequate heat dissipation and others will require a fan kit and louver combination for an economical ventilation option. Small enclosures can use a vortex cooler using compressed air. Sealed enclosures may require a heat exchanger or an air conditioner controlling the internal temperature without introducing outside air and its contaminants.
https://cdn.automationdirect.com/static/press/ADC-Enclosures.pdf