What the Growth of Plant-Based Foods Means for Food and Beverage Manufacturers
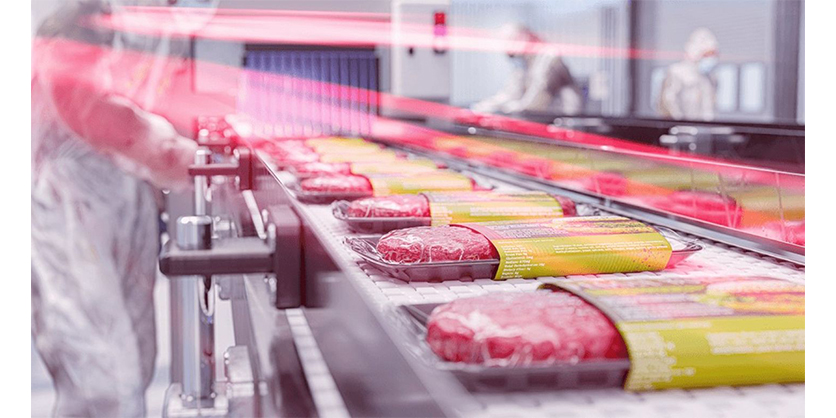
July 11, 2023
There are more plant-based food and beverage products on the market than ever before. Whether it’s oat milk or meat alternatives, the appetite for plant-based foods is bigger than it’s ever been, with 6 out of 10 U.S. households purchasing a plant-based food item in 2022.
The plant-based food market totaled more than $8 billion in 2022, and industry experts project the popularity and demand for plant-based food products will continue to grow and eclipse $160 billion by 2030. This means food and beverage manufacturers from traditional meat titans like Tyson to meat-free pioneers like Impossible Foods are accelerating their plant-based production to meet demand and lead the charge in the plant-based space.
Let’s take a quick look at what the growth of these products means for manufacturers in building an automation infrastructure that promotes efficiency and productivity, and also helps manufacturers overcome a couple challenges unique to this brand of manufacturing.
Food and beverage manufactures will need to launch new production lines
Food and beverage facilities that process a variety of proteins like beer, chicken, or fish operate multiple production lines to avoid health and safety concerns like the potential for cross contamination, but also to operate in a more efficient manner where each line can be scaled based on consumer demand.
These same principles apply to traditional manufacturers adding plant-based lines, and to plant-based processors who have a wide portfolio of products.
For example, a plant-based facility that produces meat-alternative burger patties and a meat-free line of beef jerky needs to operate separate production lines for each product. And because each line needs its own industrial enclosures and enclosure cooling units, manufacturers must prioritize flexibility in enclosure configuration to reduce their automation footprint and streamline the in-field customization process.
Small and compact industrial enclosures like Rittal’s line of Hygienic Design (HD) enclosures are designed to optimize space without sacrificing protection from unauthorized entry or the operational wellbeing of the electronics inside the enclosure. 304 stainless steel construction with smooth corners and seams and 30° angled rooftops help ensure our enclosures are both durable and provide the highest level of sanitary manufacturing. Our small and compact enclosures meet 3-A sanitary standards, are rated NEMA 4X, IP 69K, and are UL and cUL Listed for use in almost any food and beverage application.
What’s more, our small and compact enclosures provide fast, simplified deployments and integrations to help manufacturers maximize the uptime of their plant-based production lines, and the user-friendly engineering makes troubleshooting or customizing our enclosures quick and easy without the need for specialized tools.
Smart enclosure cooling units will rise up the ranks of priority
One of the biggest initiatives in modern manufacturing is the move toward more eco-friendly manufacturing models that reduce energy consumption, better conserve natural resources used in manufacturing, and cut the overall carbon footprint.
For example, increased regulatory standards for sustainable manufacturing like UL/CSA Standard 60335-2-40 have enhanced the importance of efficient climate systems that cut emissions and energy usage.
The growth of the plant-based food market and the need to expand production lines and increase manufacturing output may seem at odds with sustainability practices — especially given how many new plant-based foods are coming to market in 2023 — but smart industrial enclosure cooling units that leverage Industry 4.0 and IIoT technology can offer more precise, targeted cooling that aligns with an eco-conscious mindset.
The new Blue e+ S smart industrial enclosure cooling unit offers lower output categories of .3 kW, .5 kW, and 1 kW without sacrificing the adequate cooling necessary to keep enclosures at optimal operating temperatures.
Using heat pipe and inverter technology, the Blue e+ S provides robust cooling without the need for a compressor, expansion valve, or other regulating elements, thus significantly reducing the amount of energy required to run the unit — in fact, the Blue e+ S can reduce overall energy consumption by 75%.
From a user standpoint, the digital interface of the Blue e+ S makes it easier than ever before for manufacturers to monitor cooling outputs and climate control efficiency via our new Smart Service Portal. Remote monitoring and reporting and LED displays make network alerts or notifications more easier to view, and the digital interface simplifies a variety of user actions such as raising or lowering the internal temperature of the unit.
Make way for retrofitting facilities for warehouse automation
Part of the game food and beverage manufacturers must play in the plant-based food market is accelerating their speed-to-market in order to establish a foothold in this space and remain ahead of their competitors. While the need for speed is critical in all areas of manufacturing, the food and beverage space experienced a similar land rush during the COVID-19 crisis as manufacturers pivoted to the production of pet food as pet ownership skyrocketed during the height of the pandemic.
Retrofitting facilities for warehouse automation helped food and beverage manufacturers ramp up output and bring new production lines online during that time, and retrofitting for warehouse automation can once again help food and beverage companies launch new plant-based food product lines quickly.
While retrofitting does reduce the lead time in establishing new manufacturing sites, it does present some challenges in engineering an automation infrastructure that can be deployed in small facilities or those with more esoteric layouts or floor plans. This is where specifying standard industrial enclosures that are designed with flexibility in mind becomes key to increasing your speed-to-market.
Modular enclosures like Rittal’s TS 8 help designers and engineers easily adapt to space constraints in existing facilities with features like removable panels, interchangeable doors and handles, and a wealth of configuration options that can be completed without the need for specialized tooling.
Not only does this modular design make it easy to customize an enclosure in mere minutes without the need for additional resources or personnel, the TS 8 modular enclosure is also compatible with Rittal’s enclosure handling and transport tools to help assemblers and installers reduce the time and manpower necessary to modify their warehouse automation footprint.
Wherever the growth of plant-based foods takes manufacturers in the coming years, it’s clear that food and beverage companies need an industrial automation partner with the knowledge and experience in optimizing production and increasing efficiency of traditional food and beverage production.
